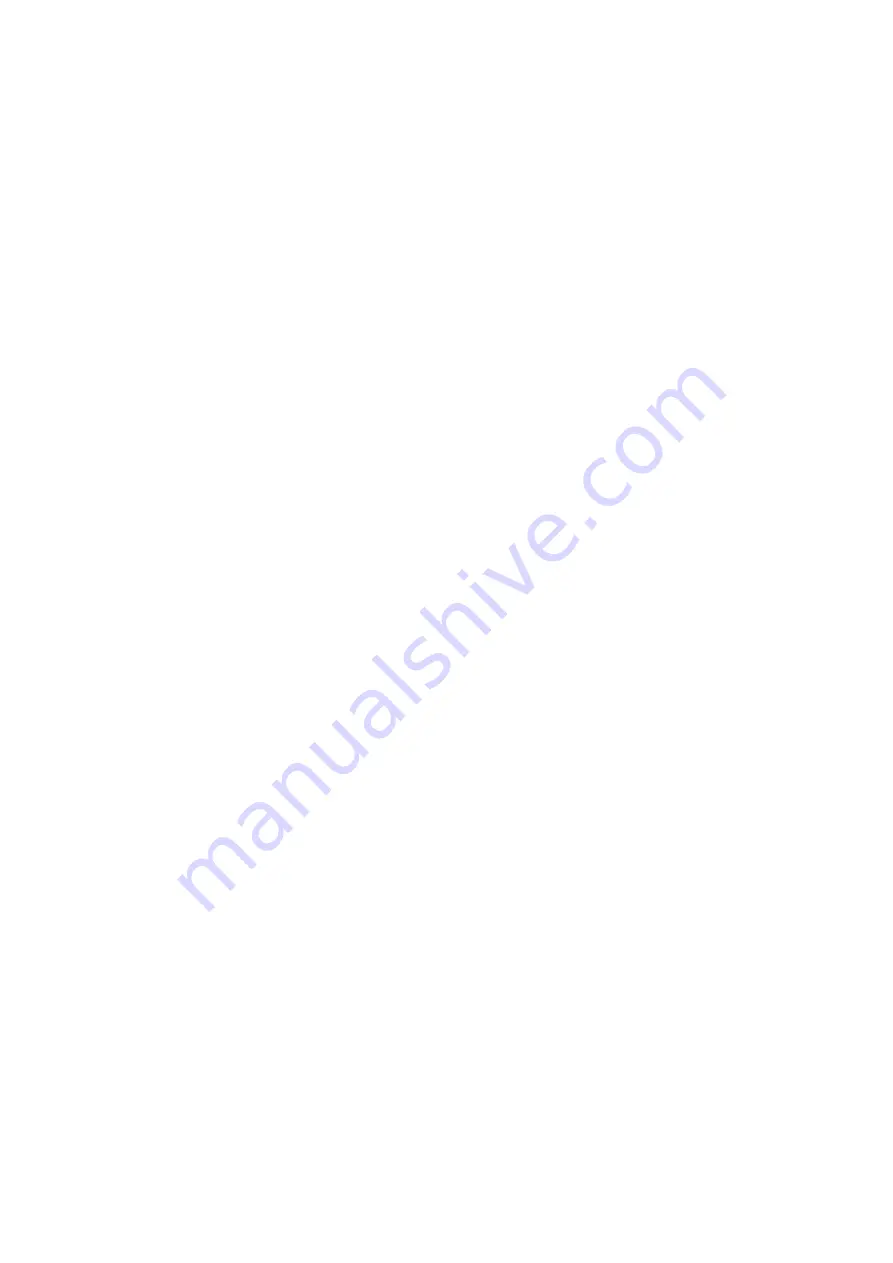
Basic description of PCL series
-22-
■
Mechanical input signals
The following four signals can be input for each axis:
1) +EL --- When this signal turns ON while operating in the positive direction, the motor stops immediately,
or decelerates and stops.
2) -EL --- When this signal turns ON while operating in the negative direction, the motor stops immediately,
or decelerates and stops.
3) SD --- Used as a deceleration signal or a deceleration stop signal by a software setting.
4) ORG --- Input signal for a zero return operation
The input logic for the +EL/-EL signals can be changed with hardware.
The input logic of the SD/ORG signals can be changed with software.
■
Servomotor I/F
The following interface can be provided for the following three signals on each axis.
1) INP --- Input a positioning complete signal that is output by a servomotor driver.
2) ERC --- Output deflection counter clear signal, sent to a servomotor driver.
3) ALM --- Input an alarm signal that is output by a servomotor driver.
When this input signal goes ON, the motor stops immediately, or decelerates and stops.
The input/output logic of the INP, ERC, and ALM signals can be changed with software.
The ERC signal is a pulse output and the pulse length can be selected.
■
Output pulse specification
Select either common pulse or two pulse mode. The output logic can be selected.
■
Emergency stop signal input
When this signal goes ON, all the axes stop immediately. While this signal is ON, no axis can be operated.
■
Interrupt signal output
An interrupt signal can be output by 17 types of errors and 19 types of events. The error interrupt causes are
always unconditionally output. However, the event causes can be set in the registers.