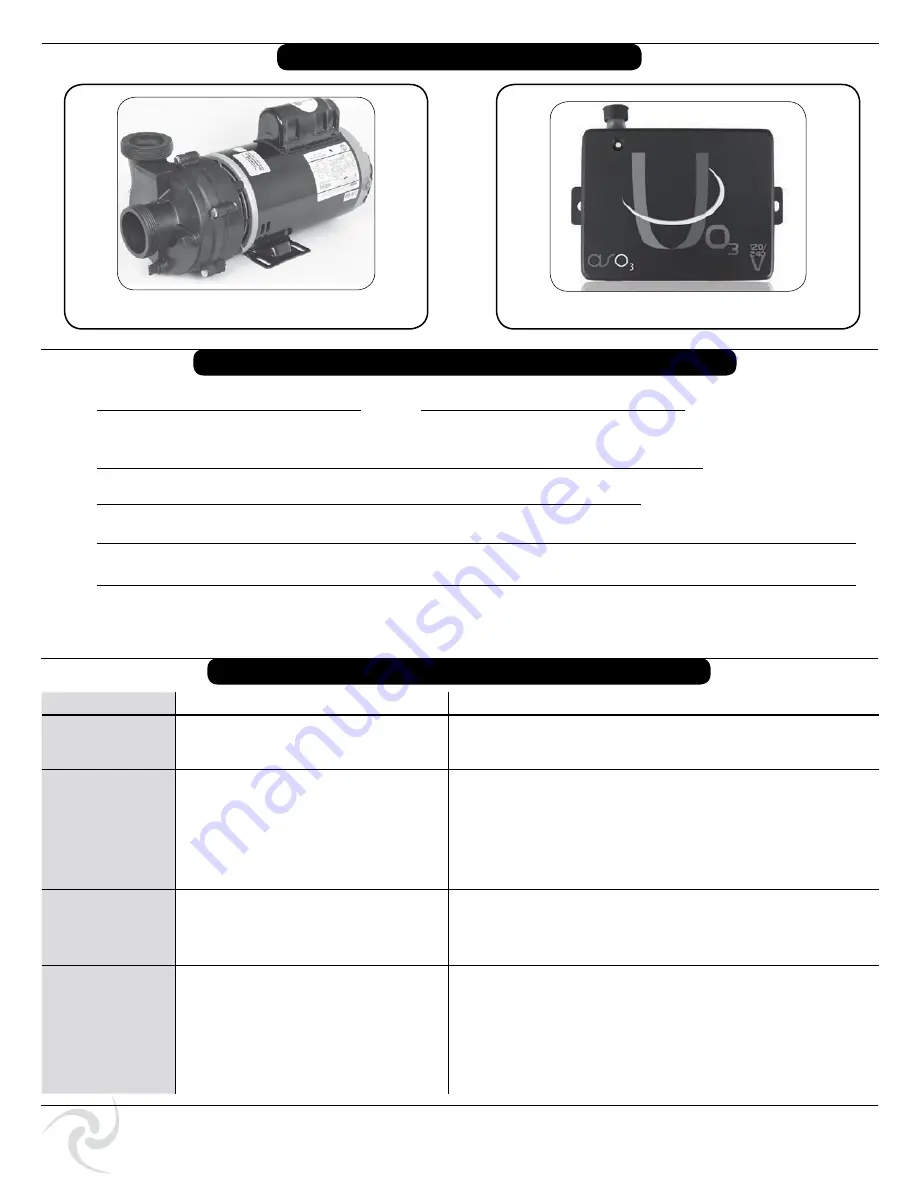
8
ELECTRONIC EQUIPMENT
, continued
Pump with Motor (may vary per model)
Ozone Generator (optional)
COMMON EQUIPMENT PROBLEMS AND SOLUTIONS
COMMON WATER PROBLEMS AND SOLUTIONS
Symptoms
Solutions
1. No jet action (air lock)
Shut-off T-valves must be in the up position.
Loosen pump/motor unions to allow air out.
2. GFCI keeps tripping
New install: incorrect GFCI wiring.
3. Water in equipment area Check: drain cap, equipment pump/motor unions, pump drain plug.
4. Only a portion of the jets work
Check that individual jets are open. Turn whirlpool diverter jet(s).
Note: If problem persists after performing the suggested solutions, contact your Dealer to
assist in resolving the problem. Any other problems not listed above, contact your Dealer.
Problem
Cause
Solutions
Calcium deposits
on shell surface
Hard water.
pH, total alkalinity not in balance.
pH, total alkalinity not in balance.
Damaged or dirty filter.
Addition of incompatible chemicals.
Low chlorine level.
Buildup of oils, soap, foreign matter.
Copper or iron metals in Hot Tub due
to water supply or corrosion of heater.
Total alkalinity, pH are low.
pH, total alkalinity not in balance.
Low calcium hardness.
Inadequate oxidation.
Addition of incompatible chemicals.
Buildup of body oils and/or
contaminants.
Clean with a non-abrasive Hot Tub surface cleaner. Test water,
adjust pH as needed. Add a stain and scale control chemical.
Add a water clarifier. Circulate for a minimum of 30 minutes.
After water has cleared, clean filter cartridge with a filter cleaner
or replace if necessary. Test chlorine and pH levels, adjust if
necessary. Change water.
Add an iron/stain and scale remover.
Test pH, adjust if necessary.
Add an anti-foam agent.
Add shock.
Adjust chlorine level.
Test pH, adjust if necessary.
Take water sample to dealer to check total alkalinity and
calcium hardness. Change water.
Cloudy water
Colored water
Excessive Foam