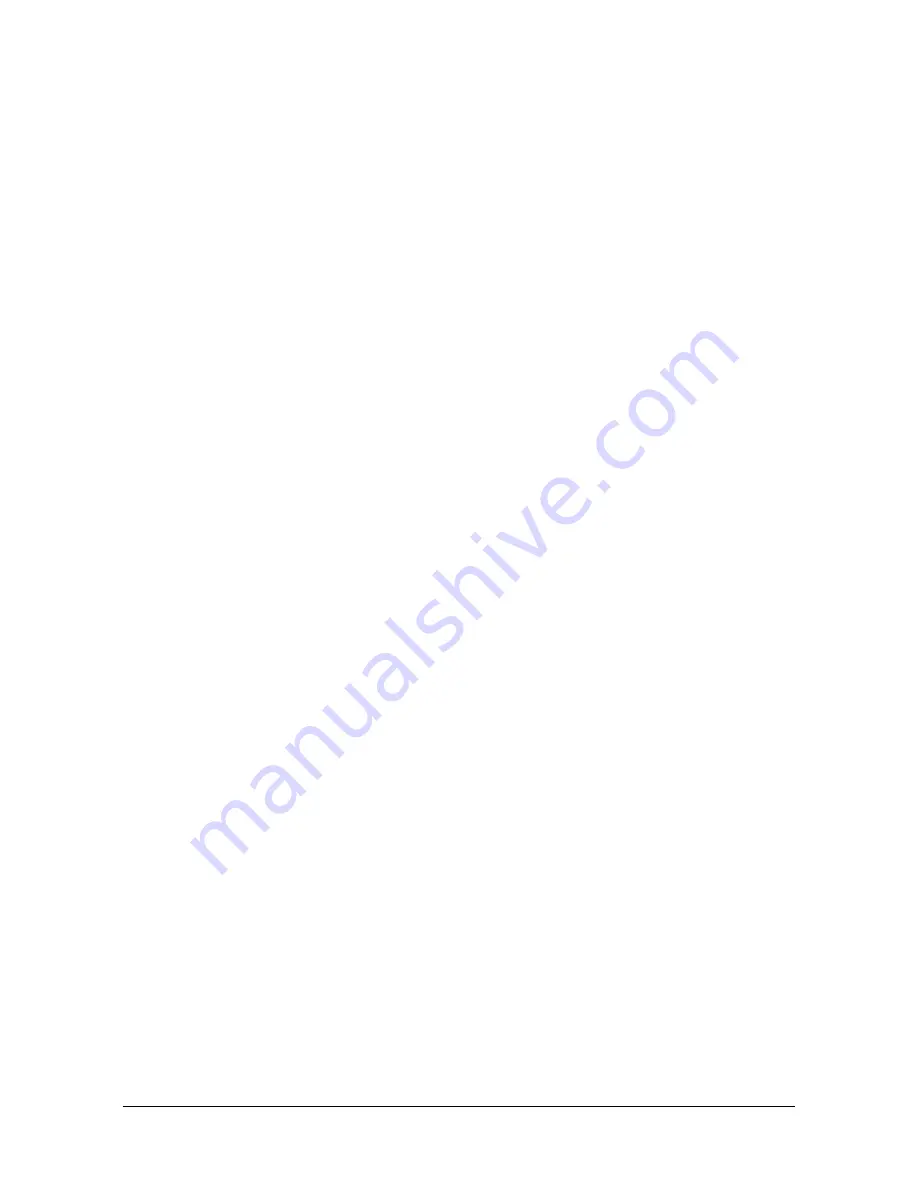
Manual, F/T Sensor, Axia90
Document #9620-05-B-Axia90-03
Pinnacle Park • 1031 Goodworth Drive • Apex, NC 27539 • Tel:+1 919.772.0115 • Fax:+1 919.772.8259 •
B-30
8. Terms and Conditions of Sale
The following Terms and Conditions are a supplement to and include a portion of ATI’s Standard Terms and
Conditions, which are on file at ATI and available upon request.
ATI warrants to Purchaser that force torque sensor products purchased hereunder will be free from defects in
material and workmanship under normal use for a period of one (1) year from the date of shipment. The warranty
period for repairs made under a RMA shall be for the duration of the original warranty, or ninety (90) days from
the date of repaired product shipment, whichever is longer. ATI will have no liability under this warranty unless:
(a) ATI is given written notice of the claimed defect and a description thereof with thirty (30) days after Purchaser
discovers the defect and in any event, not later than the last day of the warranty period and (b) the defective item
is received by ATI not later than (10) days after the last day of the warranty period. ATI’s entire liability and
Purchaser’s sole remedy under this warranty is limited to repair or replacement, at ATI’s election, of the defective
part or item or, at ATI’s election, refund of the price paid for the item. The foregoing warranty does not apply to any
defect or failure resulting from improper installation, operation, maintenance, or repair by anyone other than ATI.
ATI will in no event be liable for incidental, consequential, or special damages of any kind, even if ATI has been
advised of the possibility of such damages. ATI’s aggregate liability will in no event exceed the amount paid by the
purchaser for the item which is the subject of claim or dispute. ATI will have no liability of any kind for failure of
any equipment or other items not supplied by ATI.
No action against ATI, regardless of form, arising out of or in any way connected with products or services supplied
hereunder, may be brought more than one year after the cause of action accrued.
No representation or agreement varying or extending the warranty and limitation of remedy provisions contained
herein is authorized by ATI, and may not be relied upon as having been authorized by ATI, unless in writing and
signed by an executive officer of ATI.
Unless otherwise agreed in writing by ATI, all designs, drawings, data, inventions, software, and other technology
made or developed by ATI in the course of providing products and services hereunder, and all rights therein under
any patent, copyright, or other law protecting intellectual property, shall be and remain ATI’s property. The sale
of products or services hereunder does not convey any expressed or implied license under any patent, copyright,
or other intellectual property right owned or controlled by ATI, whether relating to the products sold or any other
matter, except for the license expressly granted below.
In the course of supplying products and services hereunder, ATI may provide or disclose to Purchaser confidential
and proprietary information of ATI relating to the design, operation, or other aspects of ATI’s products. As between
ATI and Purchaser, ownership of such information, including without limitation any computer software provided
to Purchaser by ATI, shall remain in ATI and such information is licensed to Purchaser only for Purchaser’s use in
operating the products supplied by ATI hereunder in Purchaser’s internal business operations.
Without ATI’s prior written permission, Purchaser will not use such information for any other purpose of provide or
otherwise make such information available to any third party. Purchaser agrees to take all reasonable precautions to
prevent any unauthorized use or disclosure of such information.
Purchaser will not be liable hereunder with respect to disclosure or use of information which: (a) is in the public
domain when received from ATI, (b) is thereafter published or otherwise enters the public domain through no fault
of Purchaser, (c) is in Purchaser’s possession prior to receipt from ATI, (d) is lawfully obtained by Purchaser from a
third party entitled to disclose it, or (f) is required to be disclosed by judicial order or other governmental authority,
provided that, with respect to such to maintain the confidentiality of such information.