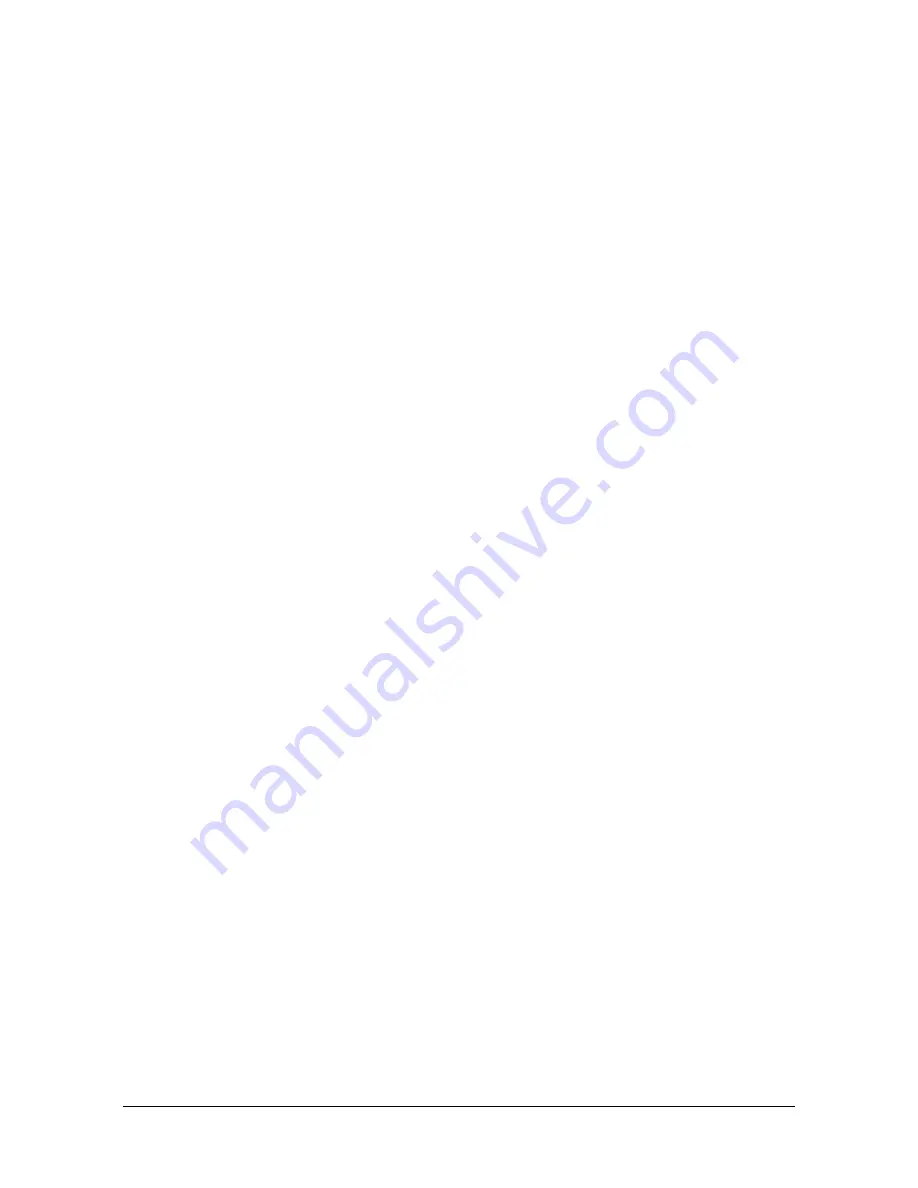
Manual, F/T Sensor, Axia90
Document #9620-05-B-Axia90-03
Pinnacle Park • 1031 Goodworth Drive • Apex, NC 27539 • Tel:+1 919.772.0115 • Fax:+1 919.772.8259 •
B-24
4.2.1 Avoid Overloading the Sensor During Tool Transformation
It is possible for the user to set a reference point of origin that does not detect that a torque is
applied to the customer tooling, and by extension, the sensor. Torque is the force multiplied by the
distance of that force from a reference point of origin. If the customer reference point of origin is
at the same point at which a force is applied, the distance from that force to the customer reference
point of origin is zero. Any force that is multiplied by a distance of zero yields zero torque. The
software tool transformation reports that no torque is applied to the sensor. However, the sensor’s
point of origin has not changed, and the force is still applied at a distance from the sensor’s point of
origin. Therefore, if the customer is evaluating overloading conditions, the customer should use the
sensor’s point of origin as the reference point.
4.2.2 Tool Transformation Functionality Through a
Communication Interface
The user defines a reference point by inputting a parameter set that is a series of (3) displacements
(D
x
\ D
y
\ D
z
) and (3) rotations (R
\ R
\ R
z
). For commands that write a parameter set and units,
refer to the appropriate manual in
.
5. Maintenance
5.1 Periodic Inspection
With industrial-type applications that frequently move the system’s cabling, inspect the cable jacket for signs
of wear. While the Axia sensor is IP67 rated, keep debris and dust from accumulating on or in the sensor.
Clean the surface of the sensor with isopropyl alcohol.
5.2 Periodic Calibrating
Periodic calibration of the sensor and its electronics is required to maintain traceability to national standards.
The sensor cannot be calibrated in the field; return the sensor to ATI for recalibration. Contact an ATI
to request a Returned Materials Authorization (RMA) for
recalibration. ATI recommends annual accuracy checks (refer to
Section 3.6—Accuracy Check Procedure
If the sensor does not meet the performance requirements of the user application and fails the accuracy
check, return the sensor to ATI for recalibration.