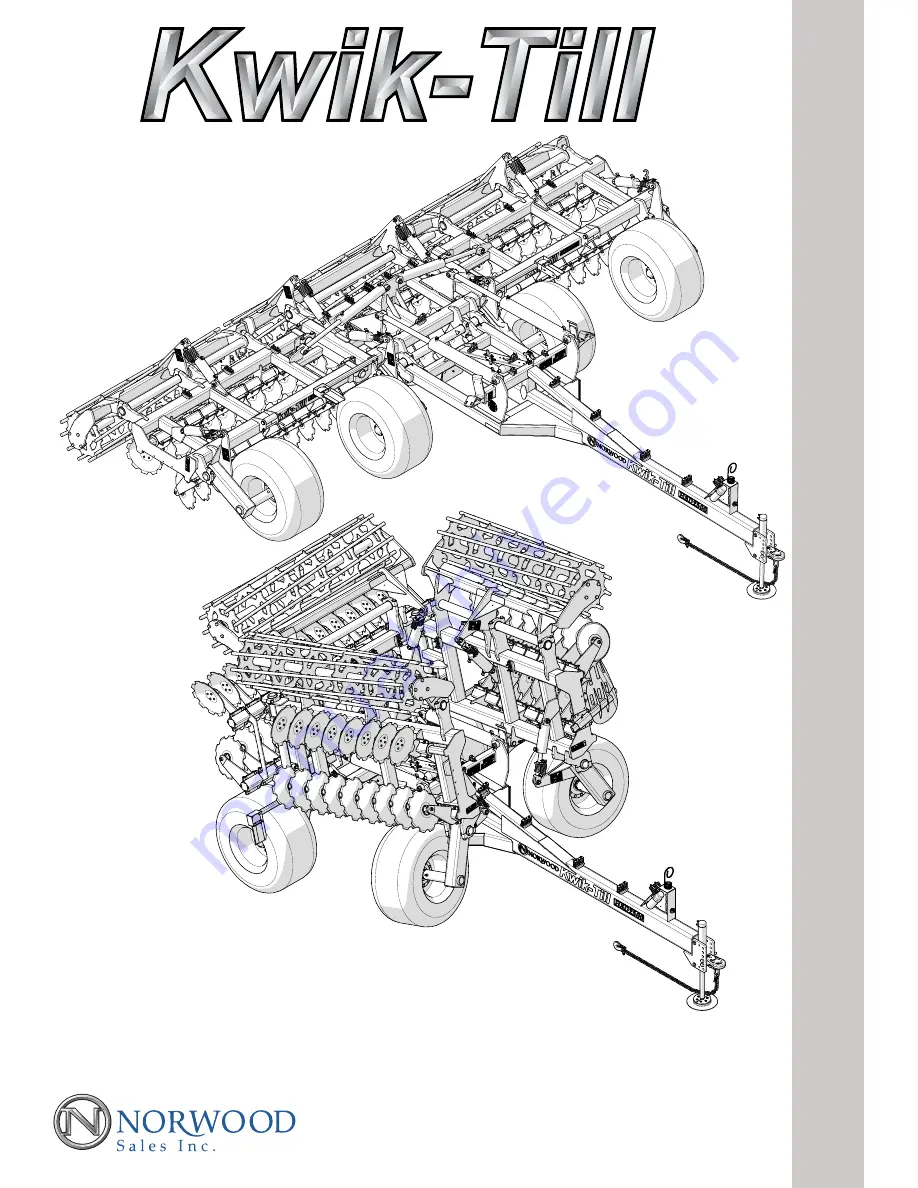
11202 38th St S, Horace, ND 58047
P/N 55-5-00131
Operator’s Manual
Models: HSD2500, HSD3000, HSD3500, HSD4000, & HSD4500
(Kwik-Till 3-Section Drawn High Speed Disk
Model HSD2500 Shown in Transport Position)
Kwik-Till
3-Section Drawn
High Speed Disk
(Kwik-Till 3-Section Drawn High Speed Disk
Model HSD2500 Shown in Field Raised Position)
Содержание Kwik-Till HSD2500
Страница 2: ......
Страница 10: ...1 4 1 GENERAL INFORMATION This Page Is Intentionally Left Blank...
Страница 31: ...2 SAFETY INFORMATION 2 21 Fig 2 10 Warning Decal P N 90 44 0395 Fig 2 11 Safety Decal Location See Fig 2 10...
Страница 33: ...2 SAFETY INFORMATION 2 23 Fig 2 14 Warning Decal P N 90 44 0396 Fig 2 15 Safety Decal Location See Fig 2 14...
Страница 34: ...2 SAFETY INFORMATION 2 24 Fig 2 16 Warning Decal P N 90 44 0508 Fig 2 17 Safety Decal Location See Fig 2 16...
Страница 36: ...2 SAFETY INFORMATION 2 26 Fig 2 22 Danger Decal P N 90 44 0399 Fig 2 23 Safety Decal Location See Fig 2 22...
Страница 91: ...4 WORKING OPERATIONS 4 25 Fig 4 69 3 Rear Roller Deflector Locations A A...
Страница 92: ...4 WORKING OPERATIONS 4 26 This Page Is Intentionally Left Blank...
Страница 134: ...5 MAINTENANCE 5 42 This Page Is Intentionally Left Blank...
Страница 144: ...8 FORMS AND DECLARATIONS 8 2 This Page Is Intentionally Left Blank...
Страница 152: ...i 6...
Страница 153: ......