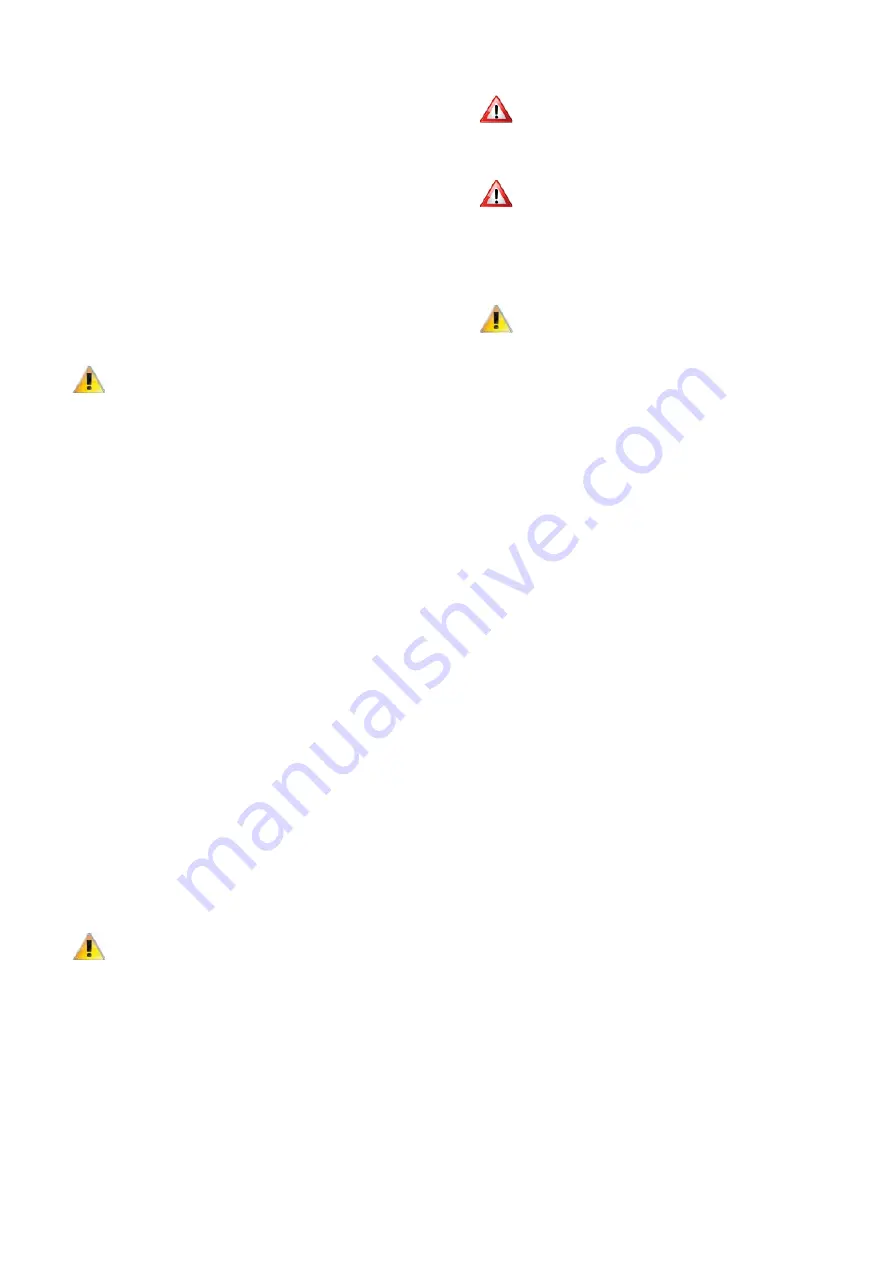
(b) If the current drawn is greater than the stated running
current, in most probability this will be caused by insuffi
cient
static pressure within the ductwork, in which case system
resistance should be increased through the introduction of a
damper placed as close to the start of the ductwork as
possible, thereby resulting in a reduction in drawn current.
The damper should be adjusted until the current is in
accordance with that stated on the data plate.
(c) If the current drawn is too low the duct outlet grilles will
require opening to reduce static pressure and increase air
volume, if this is not the case overheat cut outs can be caused.
Caution
The Fan Belts must be rechecked on completion of
commissioning ensuring that the tension is correct and
the pulleys are in alignment
3.4
Commissioning - hand over
(a) Upon full and satisfactory completion of commissioning,
a record of commissioning information (contact, date, etc)
should be left with the heater, a copy of which must also be
forwarded to the supplier (details on rear page)
(b) The commissioning engineer must ensure that the user is
familiar with the safe and effi
cient use of the heater, detailing
the function of all controls, and main components.
(c) The user should be made aware of the following in
particular
(i) Lighting, shutdown, and operational information.
(ii) Safety features, data plate, and labelling.
(iii) The requirement for regular inspection - especially if the
heater is within a more demanding environment - and the
need for regular servicing carried out by competent and
qualifi ed persons.
(d) Section 8 ‘User Instructions’ should be left with the
customer upon satisfactory completion of the commissioning
and hand-over.
Caution
After approximately 100 hours of running, the tension of the
fan belts must be checked to ensure that they are correct and
that they have not stretched. See section 4.2.5 for further
instructions.
4.0 Servicing.
S
ervicing must be carried out on a regular basis, the
maximum interval between services being 1 year.
Warning
It is a requirement that only suitably qualifi ed and competent
persons are allowed to undertake servicing.
Warning
Before any maintenance or servicing work is carried out the
heater must be shut down and allowed to cool, and have the
oil and electric supplies to it turned off at the supply valve and
isolator respectively.
Caution
Certain component parts are factory sealed and are designed
so as to be tamper proof. Usually such items do not require
servicing, and therefore should not be tampered with.
Failure to comply with this can invalidate any warranty, and
can also lead to premature failure.
The following parts fall within this category: room thermostat,
time clock, frost thermostat, sequential controller, and fan and
motor.
Reference should be made to the separate information
covering the operational details of the burner and timer.
Only approved spare/replacement parts can be fi tted, failure
to comply with this can compromise the safe and effi
cient
running of the heater, and can also invalidate any warranty
claim.
4.1
Planned Servicing
In order to maintain the effi
cient operation of the heater it is
recommended that the following planned servicing and
preventative maintenance programme is adopted by the user.
Quarterly Inspection
(a) Visual inspection of the burner
(b) Clean and check spark electrode
(c) Clean and check photocell
(d) Check overheat safety is operational
Bi-Annual Inspection
(a) As per quarterly inspection, plus...
(b) Combustion check
(c) Smoke test
Annual Inspection
(a) As per half year inspection, plus...
(b) Heat exchanger and cleaning
(c) Electrical connections
(d) Main fan motor
(e) Main fan assembly
(f) Pulleys
(g) Fan belts
(h) Oil supply including fi lter
Содержание Reznor 120
Страница 16: ...Flat roof with no parapet Flat roof with structure close to flue outlet Pitched roof not greater than 45...
Страница 17: ...Front View Side View Top View Nozzle Outlet also showing spigot Top View Duct Outlet 1 14 Dimensions...
Страница 28: ...Wiring Diagram 20 45 600 30 40 ON OFF Riello Burner Integral SC SZ 230 50 1ph...
Страница 29: ...Wiring Diagram 20 45 601 60 85 ON OFF Riello Burner Integral SC SZ 230 50 1ph...
Страница 30: ...Wiring Diagram 20 45 602 120 135 ON OFF Riello Burner Integral SC SZ 230 50 1ph...
Страница 31: ...Wiring Diagram 20 45 603 60 300 ON OFF Riello Burner Integral SC SZ 415 50 3ph...
Страница 32: ...Wiring Diagram 20 45 616 30 40 ON OFF Riello Burner Remote SC SZ 230 50 1ph...
Страница 33: ...Wiring Diagram 20 45 617 60 85 ON OFF Riello Burner Remote SC SZ 230 50 1ph...
Страница 34: ...Wiring Diagram 20 45 618 120 135 ON OFF Riello Burner Remote SC SZ 230 50 1ph...
Страница 35: ...Wiring Diagram 20 45 619 60 300 ON OFF Riello Burner Remote SC SZ 415 50 3ph...
Страница 36: ...Wiring Diagram 20 45 604 30 40 ON OFF Riello Burner Integral CP4 230 50 1ph...
Страница 37: ...Wiring Diagram 20 45 605 60 85 ON OFF Riello Burner Integral CP4 230 50 1ph...
Страница 38: ...Wiring Diagram 20 45 606 120 135 ON OFF Riello Burner Integral CP4 230 50 1ph...
Страница 39: ...Wiring Diagram 20 45 607 60 300 ON OFF Riello Burner Integral CP4 415 50 3ph...
Страница 40: ...Wiring Diagram 20 45 620 30 40 ON OFF Riello Burner Remote CP4 230 50 1ph...
Страница 41: ...Wiring Diagram 20 45 621 60 85 ON OFF Riello Burner Remote CP4 230 50 1ph...
Страница 42: ...Wiring Diagram 20 45 622 120 135 ON OFF Riello Burner Remote CP4 230 50 1ph...
Страница 43: ...Wiring Diagram 20 45 623 60 300 ON OFF Riello Burner Remote CP4 415 50 3ph...
Страница 44: ...Wiring Diagram 20 45 612 30 40 ON OFF Riello Burner No Controls 230 50 1ph...
Страница 45: ...Wiring Diagram 20 45 613 60 85 ON OFF Riello Burner No Controls 230 50 1ph...
Страница 46: ...Wiring Diagram 20 45 614 120 135 ON OFF Riello Burner No Controls 230 50 1ph...
Страница 47: ...Wiring Diagram 20 45 615 60 300 ON OFF Riello Burner No Controls 415 50 3ph...
Страница 55: ...5 Parts Lists...
Страница 66: ...Notes...
Страница 67: ...Notes...