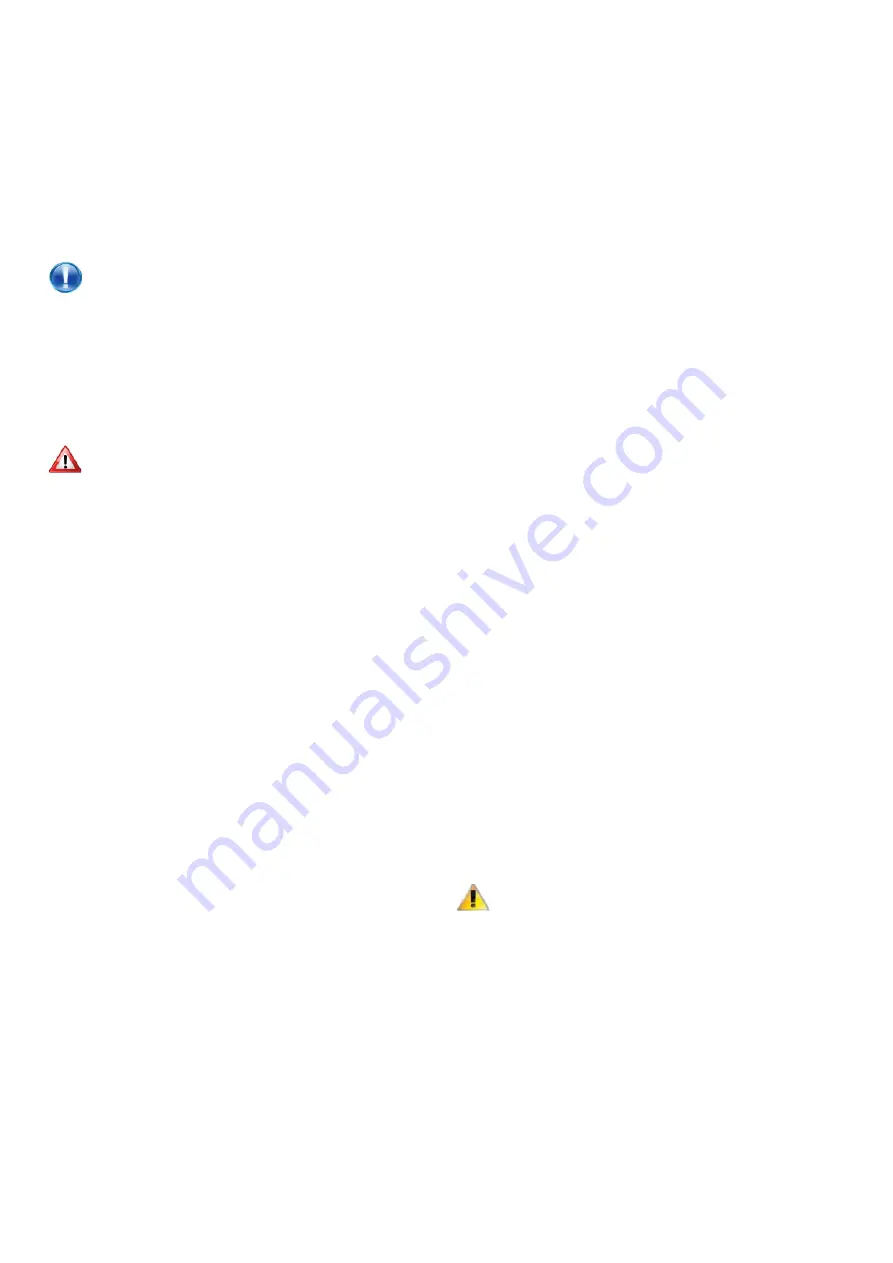
(section B)
(j) Repeat steps 3.1 q, and 3.2 c,e,f.
----------- O R ----------
3 >15s
Burner ignition...
4 <20s
Burner ignition cycle complete
Note:
It is strongly recommended that the separate manual
concerning the operational details of the burner supplied with
the heater as part of the information package is studied prior
to commissioning.
Time intervals within the ignition sequence will vary slightly
from one model to another.
Warning
If burner ignition is not satisfactorily accomplished,
commissioning must not proceed until the reason or fault has
been identifi ed and rectifi ed, if necessary by reference to the
separate burner information or to section 6 of this manual.
(k) Repeat steps 3.2 c,a,
(l) Repeat steps 3.2 d,e,f, allowing the heater to reach thermal
equilibrium.
(m) Adjust room thermostat to its highest setting, and allow
the heater to continue to fi re.
(n) Gradually reduce the temperature setting on the room
thermostat until the burner shuts down, (@ < ambient and
then gradually increase the temperature setting on the
thermostat until heat is called for, (@ > ambient) and the
burner automatically re-fi res.
(o) Re-set time clock to a minimum off period, checking that
the burner shuts down, and then automatically re-lights once
the minimum off period has elapsed (Separate information on
the time clock is contained within the information package
supplied with the heater).
(p) Check limit stat by tripping the fan motor overload re-set
by pressing the reset button on the overload, located on the
heater electrical panel. The time between the fan stopping
and burner shut down should be noted (90 seconds max),
once the burner has shut down the overload on the motor
should be released.
(q) Undertake fl ue gas analysis using approved and calibrated
analysing equipment recording data on the commissioning
card, ie, CO, CO2, net and gross fl ue temperatures.
Record burner oil pump pressure, ambient temperature,
barometric pressure, and smoke reading (0 - 1 Baccarach
scale).
Note (i)
The burner air and oil pressure settings should be only very
fi nely adjusted to achieve a CO2 reading of 12.5% (+/- 0.5%).
Note (ii)
The gross effi
ciency must be approximately 80% sample
taken at 1m above the fl ue spigot point.
Note (iii)
All Cabinet Heaters are test fi red and pre-commissioned as
part of the manufacturing process, if however, during on site
commissioning the data are found to be not in accordance
with the manufacturers data, then the following action is
recommended.
* Re-check all readings and calculations.
* Adjust burner as per manufacturers instructions.
* Consult the Technical Department, details on rear page.
(r) Complete commissioning card and provide operating
instructions for the user, high-light the fact that the
manufacturer recommends that in the interests of safety and
effi
ciency the heater is serviced on a regular basis only by
qualifi ed and competent persons.
The completed commissioning card must be returned to the
supplier (details on rear page) immediately after the
satisfactory completion of commissioning, failure to do so can
invalidate any subsequent warranty claim.
(s) Set all controls to the requirements of the user.
3.3
Commissioning - air delivery system
On free blowing applications the integrity of the fastenings on
the heater top and outlet nozzles must be checked .
Final adjustment for the direction of the air fl ow from the
nozzle hoods should be made, and the hoods should be
secured in the required position by drilling through the two
holes provided in the hood outer ring and fastened in place
using self tapping screws.
Caution
On ducted applications it is necessary that the system is
balanced in order to optimise the effi
ciency of the heater and
the air distribution and delivery system Failure to balance the
system can result in fan motor overloading and premature
component failure, it can also result in an ineffi
cient heating/
ventilation system.
Check that the amount of fan produced air volume is in
accordance with the heater specifi cation, if the volume is too
great the fan can be overloaded. Ensure that the running
current is as per that stated on the heater data plate.
Alternatively, the static pressure should be measured at the
start of the ductwork to confi rm that it is within the
permissible tolerance.
Содержание Reznor 120
Страница 16: ...Flat roof with no parapet Flat roof with structure close to flue outlet Pitched roof not greater than 45...
Страница 17: ...Front View Side View Top View Nozzle Outlet also showing spigot Top View Duct Outlet 1 14 Dimensions...
Страница 28: ...Wiring Diagram 20 45 600 30 40 ON OFF Riello Burner Integral SC SZ 230 50 1ph...
Страница 29: ...Wiring Diagram 20 45 601 60 85 ON OFF Riello Burner Integral SC SZ 230 50 1ph...
Страница 30: ...Wiring Diagram 20 45 602 120 135 ON OFF Riello Burner Integral SC SZ 230 50 1ph...
Страница 31: ...Wiring Diagram 20 45 603 60 300 ON OFF Riello Burner Integral SC SZ 415 50 3ph...
Страница 32: ...Wiring Diagram 20 45 616 30 40 ON OFF Riello Burner Remote SC SZ 230 50 1ph...
Страница 33: ...Wiring Diagram 20 45 617 60 85 ON OFF Riello Burner Remote SC SZ 230 50 1ph...
Страница 34: ...Wiring Diagram 20 45 618 120 135 ON OFF Riello Burner Remote SC SZ 230 50 1ph...
Страница 35: ...Wiring Diagram 20 45 619 60 300 ON OFF Riello Burner Remote SC SZ 415 50 3ph...
Страница 36: ...Wiring Diagram 20 45 604 30 40 ON OFF Riello Burner Integral CP4 230 50 1ph...
Страница 37: ...Wiring Diagram 20 45 605 60 85 ON OFF Riello Burner Integral CP4 230 50 1ph...
Страница 38: ...Wiring Diagram 20 45 606 120 135 ON OFF Riello Burner Integral CP4 230 50 1ph...
Страница 39: ...Wiring Diagram 20 45 607 60 300 ON OFF Riello Burner Integral CP4 415 50 3ph...
Страница 40: ...Wiring Diagram 20 45 620 30 40 ON OFF Riello Burner Remote CP4 230 50 1ph...
Страница 41: ...Wiring Diagram 20 45 621 60 85 ON OFF Riello Burner Remote CP4 230 50 1ph...
Страница 42: ...Wiring Diagram 20 45 622 120 135 ON OFF Riello Burner Remote CP4 230 50 1ph...
Страница 43: ...Wiring Diagram 20 45 623 60 300 ON OFF Riello Burner Remote CP4 415 50 3ph...
Страница 44: ...Wiring Diagram 20 45 612 30 40 ON OFF Riello Burner No Controls 230 50 1ph...
Страница 45: ...Wiring Diagram 20 45 613 60 85 ON OFF Riello Burner No Controls 230 50 1ph...
Страница 46: ...Wiring Diagram 20 45 614 120 135 ON OFF Riello Burner No Controls 230 50 1ph...
Страница 47: ...Wiring Diagram 20 45 615 60 300 ON OFF Riello Burner No Controls 415 50 3ph...
Страница 55: ...5 Parts Lists...
Страница 66: ...Notes...
Страница 67: ...Notes...