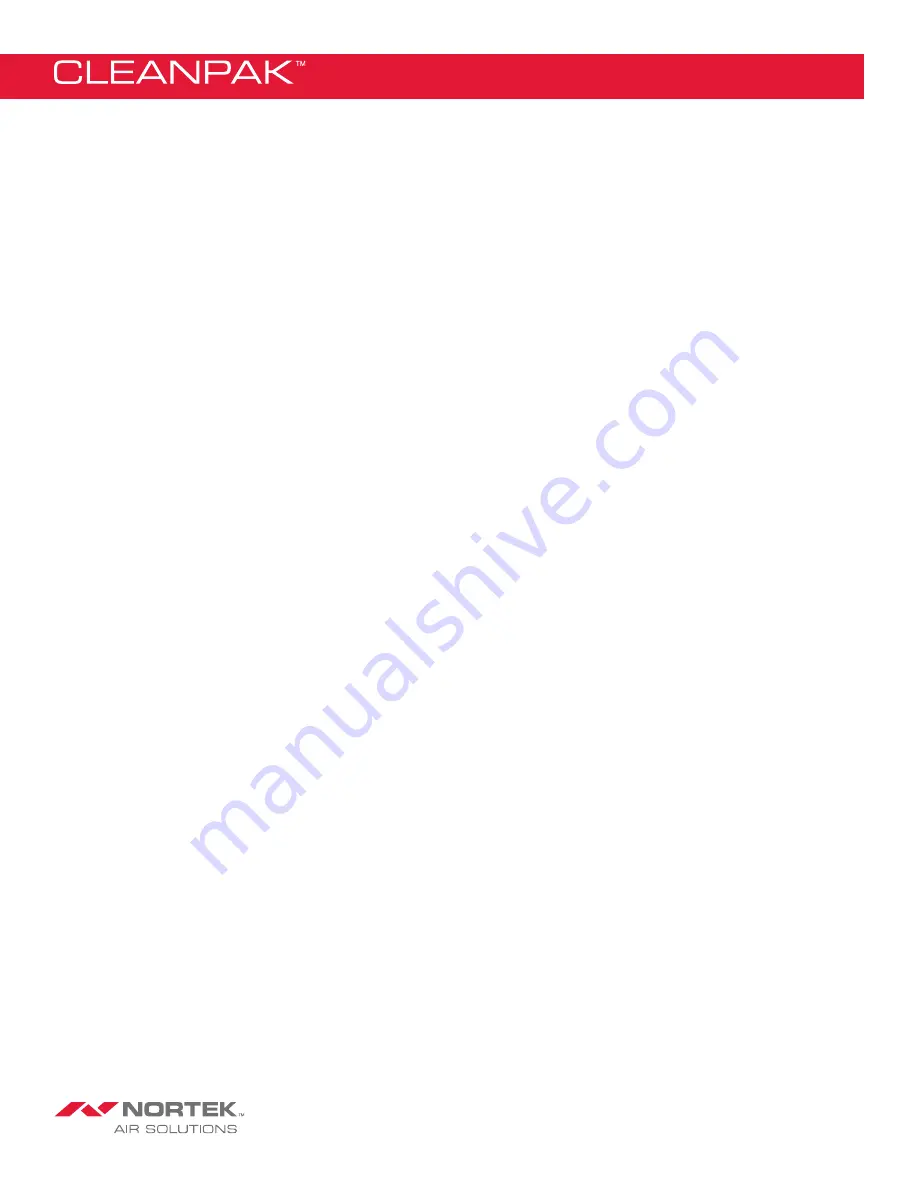
4
standards at the factory. FROM RECEIPT THROUGH
COMPLETE INSTALLATION, THE INSTALLER IS
RESPONSIBLE FOR HANDLING ALL PRODUCTS ON
THE JOB SITE.
After receiving the parts from the shipper, do not
store them outside. Do not store them in high-traffic or
unprotected areas.
All parts should be stored in a controlled environment,
especially when delivered to job sites with variable (hot or
cold) or humid climates. The optimal storage temperature
is 70° F (21° C).
It is the responsibility of the installer to protect the parts
from damage at all times. Manufacturer does not take
responsibility for damage to packaging that may result in
damage to the parts.
All parts should be unpackaged in a manner consistent
with site/project specific protocol requirements.
Avoid double handling of parts.
Unpack all parts in protocol-approved area prior to moving
parts into staging area to be installed.
Wipe down parts as required by protocol taking care not to
scratch painted surfaces.
WHEN UNPACKAGING FILTER MEDIA, TAKE CARE IN
REMOVING THE PLASTIC BAG SO THAT THE MEDIA
IS NOT SCRATCHED IN ANY WAY. DO NOT PUT ANY
TYPE OF FORCE, EVEN BY HAND, ON FILTER MEDIA
INCLUDING FACE SCREEN DURING HANDLING AND
INSTALLATION SINCE IT WILL DAMAGE THE FILTER.
JERKING THE FFU WHEN IN A SIDEWAYS
ORIENTATION OR DROPPING IT CAN DAMAGE
INTERNAL COMPONENTS.
INSTALLATION
Bottom-load final filter frames
If the bottom load final filter frames are provided as an
option, install these frames into the grid system with the
appropriate gel or gasket seal pre-applied to the grid
members. Place FFU atop filter frame.
Prior to installing the final filter, check that the clip is at a
height just below the bottom of the final filter when fully
seated. With the clips against the side of the frame, install
final filter into the frame and then rotate out the clips in the
frame to hold the final filters. Turn the bolt so as to raise the
clip to hold the final filter in place. Note that the bolt is to
be turned counter-clockwise to raise the clip when looking
up from the bottom. The bolt to raise the clip should not be
over-tightened — it should be turned just enough for the
filter to seat completely against the bottom surface of the
top ledge of the frame. Use a miniature ratcheting box-end
wrench to turn the bolt — this is available by contacting the
factory or at automotive stores.
Place FFU atop cartridge.
SCOPE
Supply and hookup of all power wiring, communication
cabling, gateways, PLC, and screen setups, if applicable,
are not in CLEANPAK’s scope.
POWER WIRING
Wire the 277VAC single-phase power into the junction box
on top of each FFU. Check the label for the correct voltage
of the specific unit. This should be performed by a qualified
electrician with all appropriate safety measures. The input
power wiring into the junction box can be as follows (or
follow specific site wiring requirements):
black = hot
white = neutral
green = ground
DIP SWITCHES ON EACH FFU
Where applicable, set the dip switches on each FFU per
the attached address sheet—note that the dip switches are
in binary notation.
CONTROL OF EACH FFU
There are three options for speed adjustment depending
on the system selected:
• Local adjustment knob (no networking): Adjust speed
with potentiometer knob.
Содержание CLEANPAK CPFFU-DC-EB
Страница 1: ...CLEANPAKTM FAN FILTER UNIT MODEL CPFFU DC EB Installation Operation Manual...
Страница 28: ...28 AirCare ACM1015 Advanced Technical Manual COMMUNICATIONS SPECIFICATION Register Descriptions Table 4...
Страница 31: ...31 AirCare ACM1015 Advanced Technical Manual MECHANICAL DIMENSIONS 3 90 3 50 2 15 1 75...