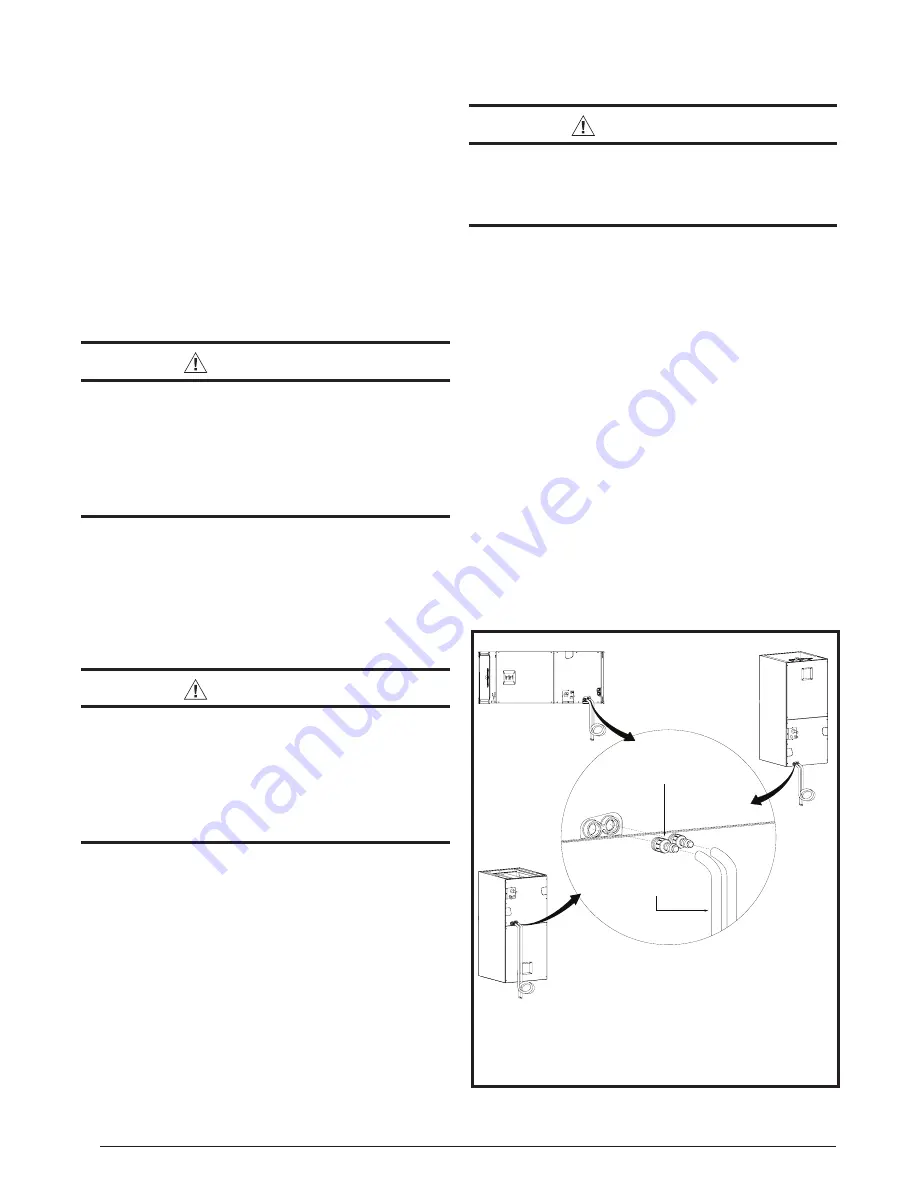
8
Connecting the Linesets
IMPORTANT NOTES FOR HORIZONTAL OR
DOWNFLOW INSTALLATIONS WITH TXV VALVE:
• The sensing bulb must be located flush against the
suction line for optimum heat transfer.
• Avoid attaching the sensing bulb to the lowest part of
the suction line where condensate may accumulate.
• Do not locate the sensing bulb on vertical sections of
the lineset.
• For horizontal lines, the bulb should not be located at
12 or 6 o’clock position of the suction line. The best
location is at 4 or 8 o’clock.
• For additional information on proper sensing bulb
locations, please refer to the valve manufacturer’s
instructions.
1. Remove grommets from line set holes.
CAUTION:
It is recommended that a wet rag be wrapped
around the suction line in front of the close off
plate or the sensing bulb (if TXV is installed)
before applying heat. Failure to keep components
cool during brazing may result in structural
damage, premature equipment failure, or possible
personal injury.
2. Cut off the heat shrink and remove the plug from the
suction line.
3. Route and cut both lineset tubes to proper length in
accordance with the outdoor unit specifications. Verify
the ends are round, clean, and free of any burrs.
4. Position grommet on line set with sufficient distance away
from brazing area. Brazing processes can permanently
damage grommets.
5. Connect the suction and liquid lineset tubes.
CAUTION:
It is recommended that a wet rag be wrapped
around the suction line in front of the close off
plate or the sensing bulb (if TXV is installed)
before applying heat. Failure to keep components
cool during brazing may result in structural
damage, premature equipment failure, or possible
personal injury.
6. Braze the individual connections with dry nitrogen flowing
through the joints.
NOTE:
This will prevent internal
oxidation and scaling from occurring.
7. Wrap the refrigerant lines with pressure sensitive neoprene
or other suitable material especially where the lines enter
the opening in the sheet metal.
8. Evacuate the system of moisture and non-condensables
to prevent low efficiency operation or damage to the unit.
The suggested range of evacuation is 350 - 500 microns.
9. Charge the system with refrigerant. Refer to the outdoor
unit installation manual for additional charging instructions.
10. Check the system for leaks, including the lineset and
the brazed joints.
11. Replace all grommets and properly dispose of all removed
parts.
Condensate Drainage
CAUTION:
The air handler must be level to ensure proper
condensate drainage. An unlevel installation may
result in structural damage, premature equipment
failure, or possible personal injury.
• Methods for disposing of condensate vary according
to local codes. Refer to local codes or authority having
jurisidiction for restrictions and proper condensate disposal
requirements.
• The drain pan that is supplied with this air handler contains
a primary and secondary drain fitting. The condensate is
drained from the unit through two 3/4” female pipe fittings
located on the front side of the unit as shown in
• The drain pan must be drained with field supplied tubing
or pvc pipe and adequately trapped. Both drain tubes
must have a minimum diameter of 3/4” and be trapped
separately.
IMPORTANT: Failure to install a trap may result in
condensation overflowing the drain pan, resulting in
substantial water damage to surrounding area.
• Route both lines to a suitable drain, avoiding sharp bends
and pinching of the lines. The drain should maintain a
minimum horizontal slope in the direction of discharge of
not less than 1” vertical for every 10 ft of horizontal run.
• If the air handler is located in or above a living space where
damage may result from condensate overflow, an auxiliary
drain pan shall be installed under the unit. A separate drain
line should extend from the pan to a conspicuous point
and serve as an alarm indicating that the primary drain
is restricted. As an alternative to a separate drain line,
3/4” Adapter w/
3/4” dia. hose barb
3/4” minimum dia.
PVC or flexible tubing
HORIZONTAL
UPFLOW
DOWNFLOW
NOTES:
1. The drain lines must maintain a downward slope to ensure proper
condensate drainage.
2. Each condensate drain must be trapped separately using a J-Trap or
field supplied loop.
Figure 6. Condensate Drainage Example
Содержание B64EM Series
Страница 27: ...27...