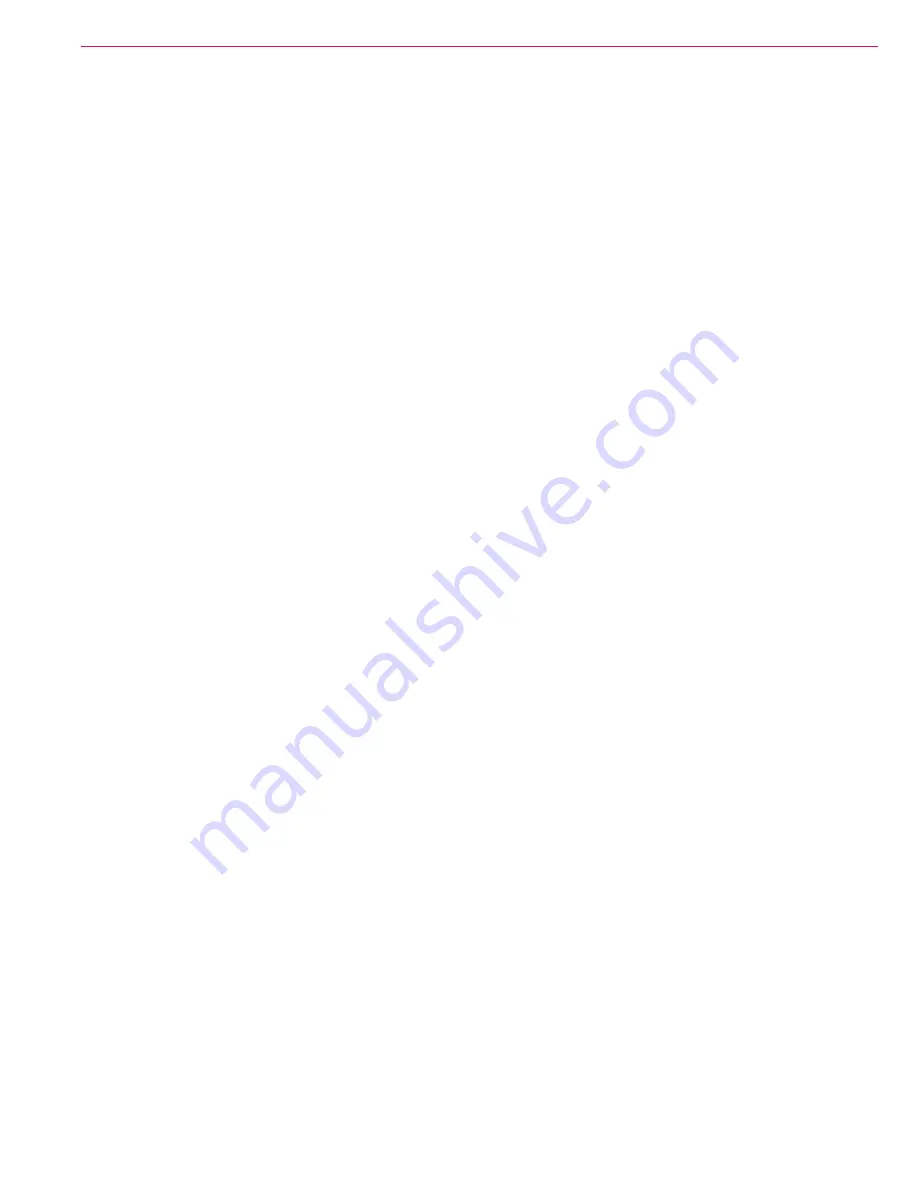
Table of Contents
3
Service Manual – SC351
Scrub System, Disc 39
Functional Description 39
Wiring Diagram 39
Component Locations 40
Maintenance and Adjustments 42
Troubleshooting 43
Removal and Installation 45
Specifications
48
Solution System 49
Functional Description 49
Wiring Diagram 49
Component Locations 50
Troubleshooting 52
Removal and Installation 53
Specifications
54
Squeegee System 55
Functional Description 55
Component Locations 56
Maintenance and Adjustments 57
Troubleshooting 59
Wheel System, Non-Traction 60
Component Locations 60
Specifications
61