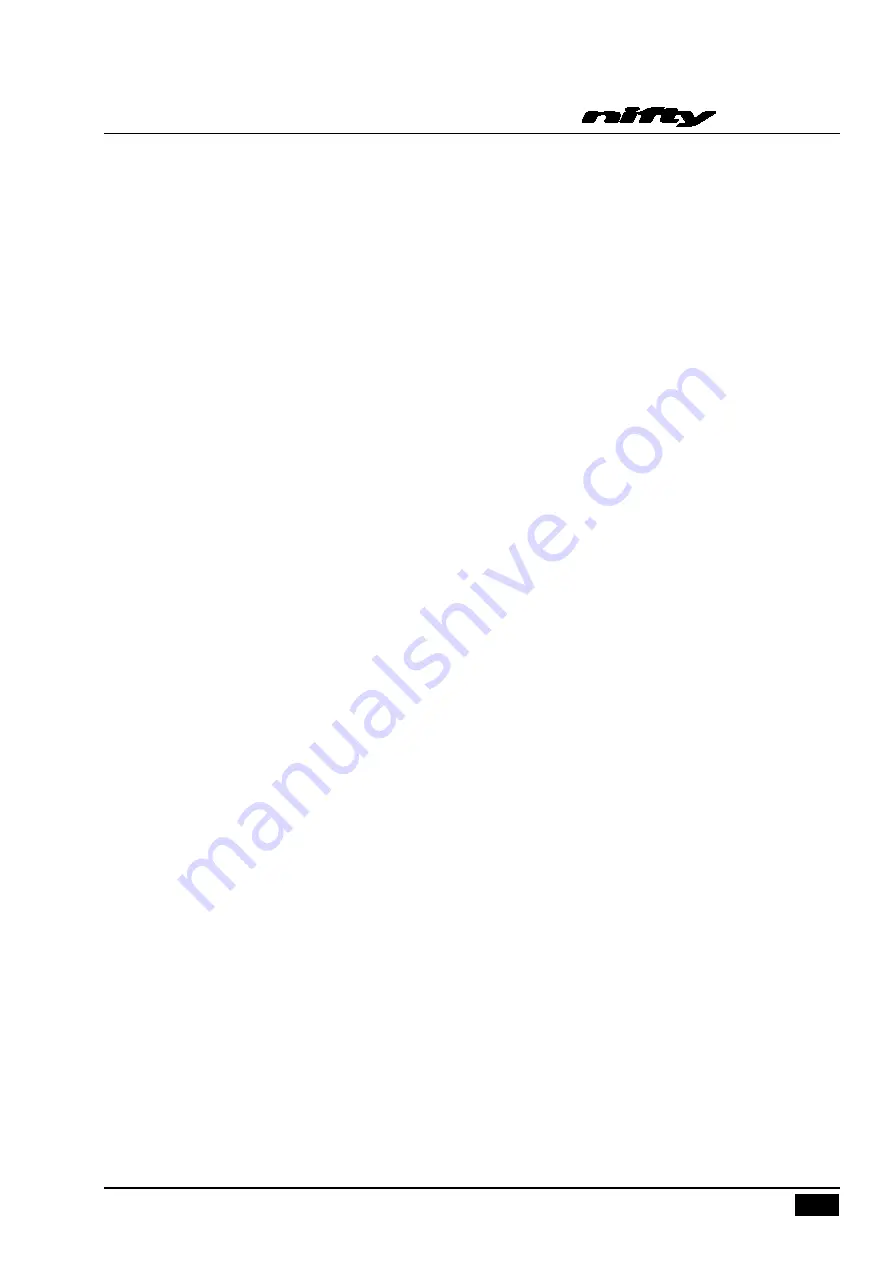
SD210 Series
Operating & Safety Instructions
English / USA – 07/11
Issue 06
33
4.7.5
INSPECTION
The cage weigh system is controlled through the detection printed circuit board, part number P16164.
This PCB is connected directly to a safety micro-switch and monitors the function of the cage weigh
system. The two relays are configured such that both need to operate to permit safe operation of the
assembly. Should either of them fail, an error signal is generated which can be seen on the printed
circuit board itself. This occurs if pressing the green button does not allow the machine to operate, no
overload signal to be given, with no load in the cage. In this case, open the cage pushbutton box or
separate box containing the PCB and look at the printed circuit board.
There are three LED’s (Light Emitting Diodes) on the board, Red LD1 for ‘Overload’, Red LD2 for ‘Relay
1/2 failed’ and Green LD3 for ‘Machine enable’. The first indicates the overload when the machine is
turned ‘On’, the second indicates a relay failure when the green button is pressed, and the third shows
the machine is enabled, again when the green button is pressed.
The failure signal is generated if either relay fails to respond to the ‘safe’ cage weigh signal from the
safety micro-switch, either due to a coil or contacts failing or if a contact sticks in place due to
welding. Under either circumstance the ‘enable’ signal is blocked, instead generating the error
message, illuminating the red LD2. The machine will not operate under this situation. The red error
signal from LD2 requires the board to be changed, as the relays are not serviceable items.
4.7.6
MAINTENANCE
The cage weigh mechanism is supported on maintenance-free precision needle roller bearings for
smooth running and friction-free operation. The accuracy of the entire assembly and in particular the
hysteresis is dependent on these components. Keeping them free of dust and dirt is recommended;
and an occasional application of WD40 to the external faces should keep them mobile and deny the
entry of dust and moisture.
The hysteresis is the amount of load required to be removed before the system re-sets allowing
continued operation.
If the assembly is subjected to any external impact force, typically whilst manoeuvring the machine
under power, or in the case of trailer units, whilst being reversed into position, the cage assembly will
require close inspection. If there is evidence of any deformation in any part of the structure, then the
advice of a Niftylift Service technician should be sought. Physical damage to the assembly is liable to
render the cage weigh system inactive, or to affect the accuracy of the result. Under no circumstance
permit a damaged machine to enter service without performing a thorough inspection and calibration of
the weigh assembly.
For this reason it is not recommended to restrain the machine in transit using strap or chains passed
through or over the cage itself. This is particularly true of the electronic load cell system, which could
be permanently damaged by the application of such excessive external forces. Whilst the mechanical
system could be considered to be more robust in operation, the same restraint forces that could be
generated through ratchet straps and the like, is likely to cause some severe deformation in the
lightweight cage structure. Use only the designated tie-down points on your Niftylift when strapping
the machine down for transport. Failure to observe this instruction could render the machine un-
usable, and a considerable repair bill for the damaged components.