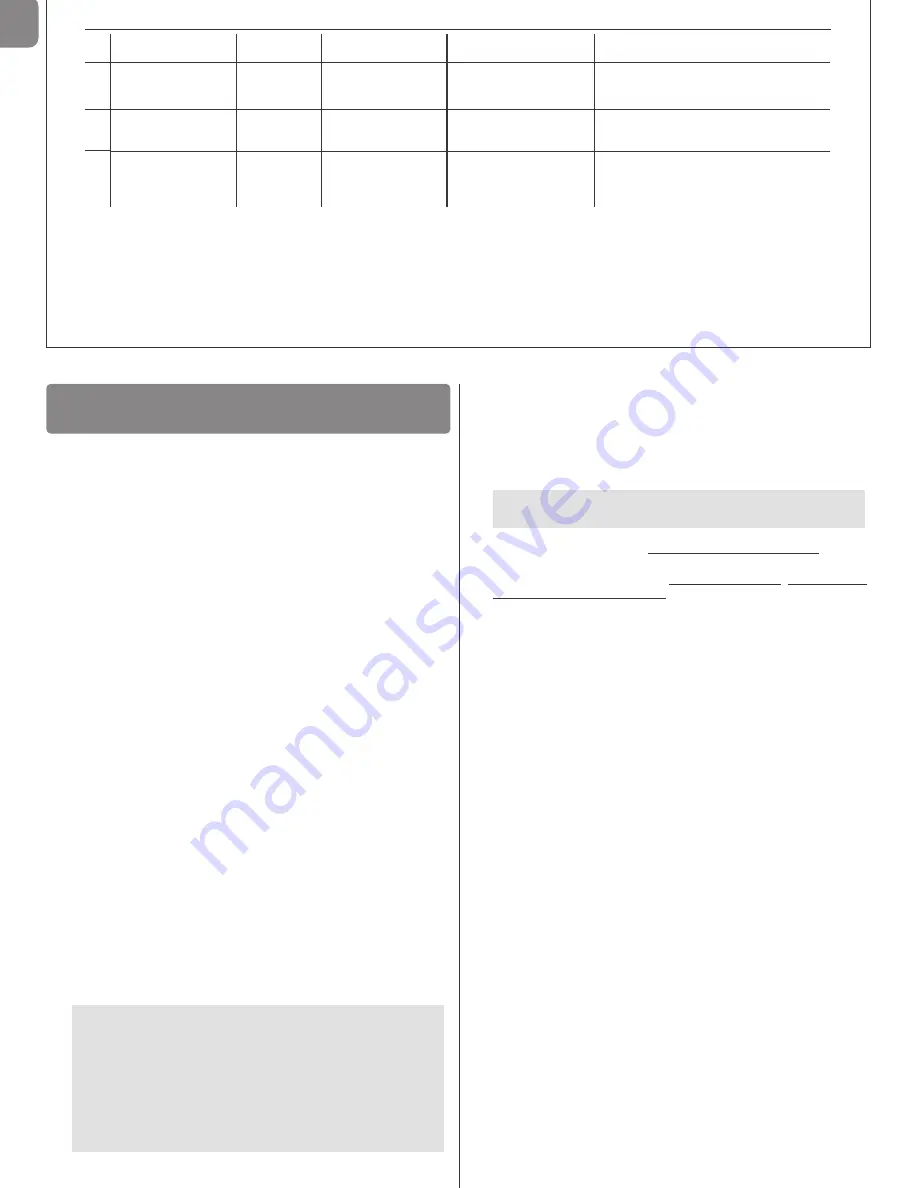
STEP 5
5.1
– INSTALLING THE AUTOMATION COMPONENTS
WARNINGS
• Incorrect installation may cause serious physical injury to those working
on or using the system.
• Before starting automation assembly, make the preliminary checks as
described in STEP 3.
After laying the electric cables, proceed with assembly of the mechanical parts
of the guides and gearmotor, in the sequence specified below.
01
.
Insert the guide in the seat on the gearmotor (
fig. 11
).
02
.
Insert the travel limit mechanical stop (
a
) in the guide and move it close to
the gearmotor; then position plate (
b
) onto the stop and secure the assem-
bly by means of a screw (
fig. 12
).
Note
–
The screw must NOT be tight-
ened excessively
as the limit stop must later be moved to its final position.
03
.
Use two screws to secure the ends of the chain into the groove on the car-
riage plate (
fig. 13
).
04
.
Fit the spring on the support supplied (
fig. 14
) and insert the assembly in
the carriage plate (the plate not used to secure the chain) (
fig. 15
).
05
.
Join the two carriage plates; insert the screw in the support of the drive
pulley; position the drive pulley in the chain and mount the assembly onto
the drive bracket with the pin supplied (
fig. 16
).
06
.
Insert the chain and carriage inside the guide, taking care to observe the
following:
Fig. 17-a)
position the side of the carriage with the chain fixed with the
screws on the same side as the contro unit cover;
Fig. 17-b)
position the carriage to approx. mid-way on the guide.
07
.
Pass the chain around the pinion of the gearmotor and close the assembly
with the protection cover (
fig. 18
).
08
.
Insert the bracket on the end of the guide and secure the two elements by
means of a nut and washer (
fig. 19
).
09
.
Tension the chain by tightening the nut on the screw of the drive bracket
(
fig. 20
).
CAUTION
– if the chain is tensioned excessively, this may
cause excessive stress and damage the gearmotor; if under-ten-
sioned this may cause unpleasant noise.
10
.
11
.
CAUTION!
– If the door is up-and-over, use the drive rod supplied
with the oscillating arm for this operation.
FOR UP-AND-OVER DOORS ONLY
If the door to be automated is “up-and-over” (projecting or non-pro-
jecting -
fig
.
1
), the
oscillating arm mod. SPA5 must be fitted
(
fig.
21
). Then proceed with assembly of the various arm components.
IMPORTANT
– Take care to move the arm as close as possible to
the handle of the door.
For assembly of the drive rod, refer to point
11
.
Note
– for assembly of the accessory, follow the instructions supplied
in the pack.
Before fitting the drive rod, cut this to a length that ensures observance of
recommended distance
E
shown in
fig. 3
. Then use screws and nuts to
secure one end of the drive rod to the bracket (the one to be fixed to the
door or oscillating arm) and the other end to the carriage (
fig. 22
).
12
.
Fix one end of the manual release cord to the carriage and the other end
to the knob (
fig. 23
).
Note
– Ensure that the manual release knob is posi-
tioned at a maximum height of 180 cm from the ground.
13
.
•
If the door is SECTIONAL:
establish the length of distance
B
consider-
ing the constraints of values
A
and
E
(
fig. 3
).
• If the door is UP-AND-OVER:
establish the length of distance B con-
sidering the constraints of value
F
(
fig. 4
).
Note
– If values A, E or F allow, the automation can also be fixed directly
onto the ceiling (minimum 4 mm).
14
.
Fold the two ceiling mounting brackets to an “L” and mount in the vicinity
of the gearmotor, by means of screws and nuts (
fig. 24
).
Note
– choose the most suitable hole on the brackets to observe distance
B
selected in point
13
.
5.2
– FIXING THE AUTOMATION TO THE WALL, CEILING, AND
DOOR
After assembly of the guide and gearmotor, fix the automation to the wall, ceil-
ing and door as follows.
01
.
Using a suitable means of support (ladder, poles or similar) lift the gearmo-
tor from the ground an position at the required height so that the guide
brackets are placed against the ceiling and wall above the door (
fig. 25
).
IMPORTANT
–
(
fig. 25-a
)
align the guide and gearmotor with the vertical
axis of the door and perpendicular to the latter (90° angle).
Note
– In the ca -
se of up-and-over doors, the guide must be aligned with the oscillating arm.
Also ensure observance of the values
A
,
B
,
E
in
fig. 3
and values
B
,
F
in
fig. 4
.
02
.
Check the position of the guide, which must be perfectly horizontal, and
mark the 4 bracket fixture points, after which drill the relative holes and
insert the plugs (
fig. 26
).
03
.
Fix the automation to the ceiling and wall using screws and plugs suited to
the support material (
fig. 27
).
Notes:
• Depending on the type of wall, the bracket at the end of the guide can be
fixed by means of the rivets or screws and plugs.
• Take care when choosing the method of bracket fixture to the ceiling,
taking into account the following:
– the bracket at the end of the guide must withstand the force required to
open and close the door;
– the ceiling mounted brackets must withstand the weight of the gearmotor.
In both cases possible wear and deformation over time must be taken into
account.
04
.
Use a saw to cut off the excess section of the ceiling-mounted brackets
(
fig. 28
).
05
.
(With the door closed)
Pull the release knob and slide the carriage until the
anchoring bracket is positioned on the upper edge of the sectional door,
or until it reaches the connection of the oscillating arm (up-and-over door).
IMPORTANT
! – Perform the operations below the door CLOSED
INSTALLATION: COMPONENT ASSEMBLY
AND CONNECTIONS
Note 1
– The cables required for the set-up of the system (not included in the pack) may vary according to the quantity and type
of devices envisaged for the installation..
Note 2
– The connections to terminals 1-2 (Stop), 4-5 (Step-step) and 3-5 (Photo) can be made using a single cable with several
internal wires.
CAUTION!
–
The cables used must be suited to the installation environment; for example a cable type H03VV-F for indoor envi-
ronments is recommended.
Technical specifications of electric cables
(
note 1
)
A
B
C
Devices
Safety
photocells
Control
pushbutton
Safety pushbutton
– sensitive edges –
etc.
Terminals
3 - 5
3 - 4
1 - 2
Maximum admissible length
20 m (
note 2
)
20 m (
note 2
)
20 m (
note 2
)
20 m (
note 2
)
Function
PHOTO
input
Input
STEP-STEP
STOP
Input
Cable type
TX
Cable 2 x 0,25 mm
2
RX
Cable 3 x 0,25 mm
2
Cable 2 x 0,25 mm
2
Cable 2 x 0,25 mm
2
E
N
Содержание Shel50Kit
Страница 2: ......
Страница 15: ...9 6 7 8 a b c d l e f h m g g...
Страница 17: ...19 17 a 17 b 20 22 18 M8 R8 x 24 V8 x 45 21 23 M6 V6 x 18...
Страница 18: ...24 V6 x 14 M6 B 4 400 mm 25 90 25 a 26 29 30 28...