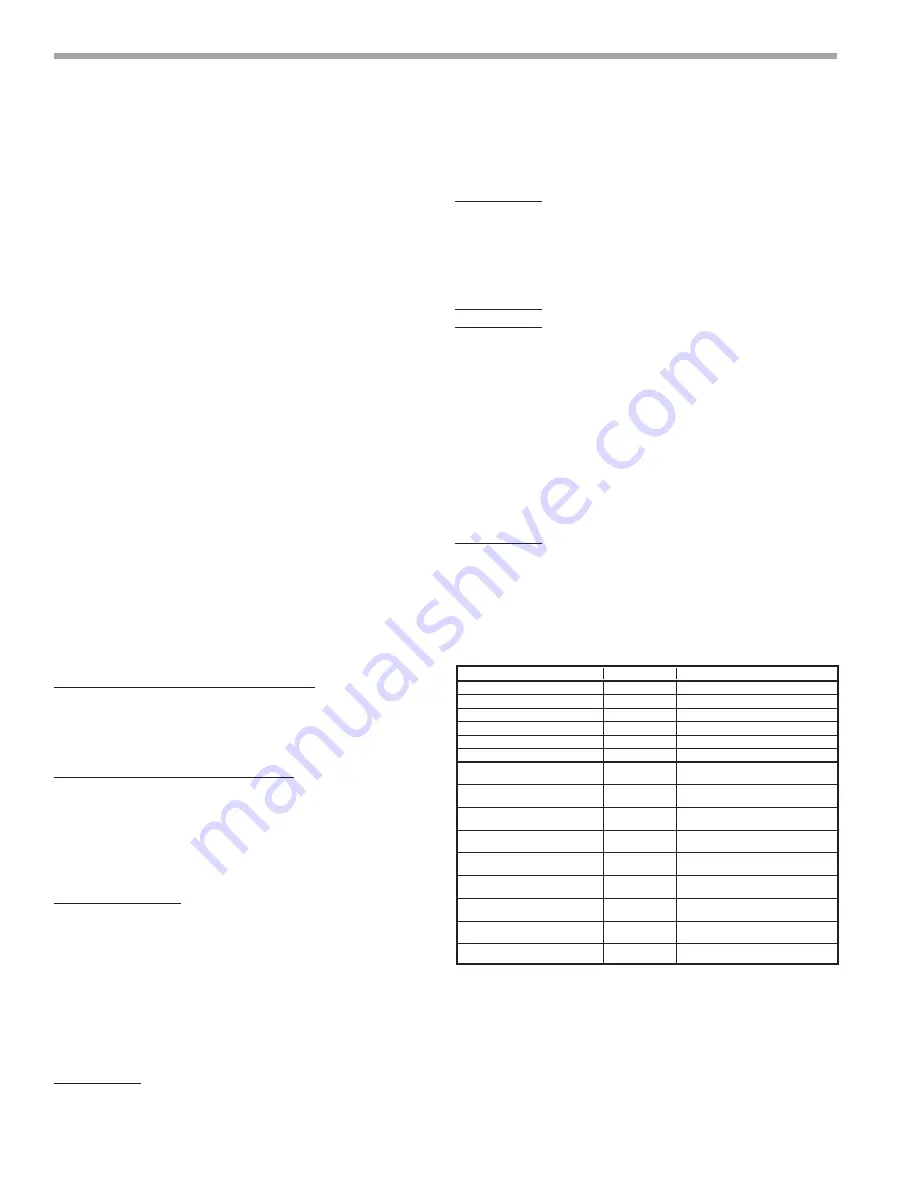
C L I M AT E M A S T E R W AT E R - S O U R C E H E AT P U M P S
C o n s o l e s
R e v. : 3 0 J u n e , 2 0 0 8 B
40
C l i m a t e M a s t e r Wa t e r- S o u r c e H e a t i n g a n d C o o l i n g S y s t e m s
CXM Controls
CXM Control
For detailed control information, see CXM/DXM
Application, Operation and Maintenance (AOM) manual
(part #97B0003N08).
Field Selectable Inputs
Test mode: Test mode allows the service technician to
check the operation of the control in a timely manner. By
momentarily shorting the test terminals, the CXM control
enters a 20 minute test mode period in which all time
delays are sped up 15 times. Upon entering test mode,
the status LED will flash a code representing the last fault.
For diagnostic ease at the thermostat, the alarm relay will
also cycle during test mode. The alarm relay will cycle
on and off similar to the status LED to indicate a code
representing the last fault, at the thermostat. Test mode
can be exited by shorting the test terminals for 3 seconds.
Retry Mode: If the control is attempting a retry of a fault,
the status LED will slow flash (slow flash = one flash
every 2 seconds) to indicate the control is in the process
of retrying.
Field Configuration Options
Note: In the following field configuration options, jumper
wires should be clipped ONLY when power is removed
from the CXM control.
Water coil low temperature limit setting: Jumper 3 (JW3-
FP1 Low Temp) provides field selection of temperature
limit setting for FP1 of 30°F or 10°F [-1°F or -12°C]
(refrigerant temperature).
Not Clipped = 30°F [-1°C]. Clipped = 10°F [-12°C].
Air coil low temperature limit setting: Jumper 2 (JW2-FP2
Low Temp) provides field selection of temperature limit
setting for FP2 of 30°F or 10°F [-1°F or -12°C] (refrigerant
temperature). Note: This jumper should only be clipped
under extenuating circumstances, as recommended by
the factory.
Not Clipped = 30°F [-1°C]. Clipped = 10°F [-12°C].
Alarm relay setting: Jumper 1 (JW1-AL2 Dry) provides
field selection of the alarm relay terminal AL2 to be
jumpered to 24VAC or to be a dry contact (no connection).
Not Clipped = AL2 connected to R. Clipped = AL2 dry
contact (no connection).
DIP Switches
Note: In the following field configuration options, DIP
switches should only be changed when power is removed
from the CXM control.
DIP switch 1: Unit Performance Sentinel Disable -
provides field selection to disable the UPS feature.
On = Enabled. Off = Disabled.
DIP switch 2: Stage 2 Selection - provides selection of
whether compressor has an “on” delay. If set to stage
2, the compressor will have a 3 second delay before
energizing. Also, if set for stage 2, the alarm relay will
NOT cycle during test mode.
On = Stage 1. Off = Stage 2
DIP switch 3: Not Used.
DIP switch 4: DDC Output at EH2 - provides selection for
DDC operation. If set to “DDC Output at EH2,” the EH2
terminal will continuously output the last fault code of
the controller. If set to “EH2 normal,” EH2 will operate as
standard electric heat output.
On = EH2 Normal. Off = DDC Output at EH2.
NOTE: Some CXM controls only have a 2 position DIP
switch package. If this is the case, this option can be
selected by clipping the jumper which is in position 4
of SW1.
Jumper not clipped = EH2 Normal. Jumper clipped =
DDC Output at EH2.
DIP switch 5: Factory Setting - Normal position is “On.”
Do not change selection unless instructed to do so by
the factory.
-Slow Flash = 1 flash every 2 seconds
-Fast Flash = 2 flashes every 1 second
-Flash code 2 = 2 quick flashes, 10 second pause, 2 quick
flashes, 10 second pause, etc.
-On pulse 1/3 second; off pulse 1/3 second
Description of Operation
LED
Alarm Relay
Normal Mode
On
Open
Normal Mode with UPS Warning
On
Cycle (closed 5 sec., Open 25 sec.)
CXM is non-functional
Off
Open
Fault Retry
Slow Flash
Open
Lockout
Fast Flash
Closed
Over/Under Voltage Shutdown
Slow Flash
Open (Closed after 15 minutes)
Test Mode - No fault in memory
Flashing Code 1
Cycling Code 1
Test Mode - HP Fault in memory Flashing Code 2
Cycling Code 2
Test Mode - LP Fault in memory Flashing Code 3
Cycling Code 3
Test Mode - FP1 Fault in memory Flashing Code 4
Cycling Code 4
Test Mode - FP2 Fault in memory Flashing Code 5
Cycling Code 5
Test Mode - CO Fault in memory Flashing Code 6
Cycling Code 6
Test Mode - Over/Under
shutdown in memory
Flashing Code 7
Cycling Code 7
Test Mode - UPS in memory
Flashing Code 8
Cycling Code 8
Test Mode - Swapped Thermistor Flashing Code 9
Cycling Code 9
Table 7a: CXM/DXM LED And Alarm
Relay Operations