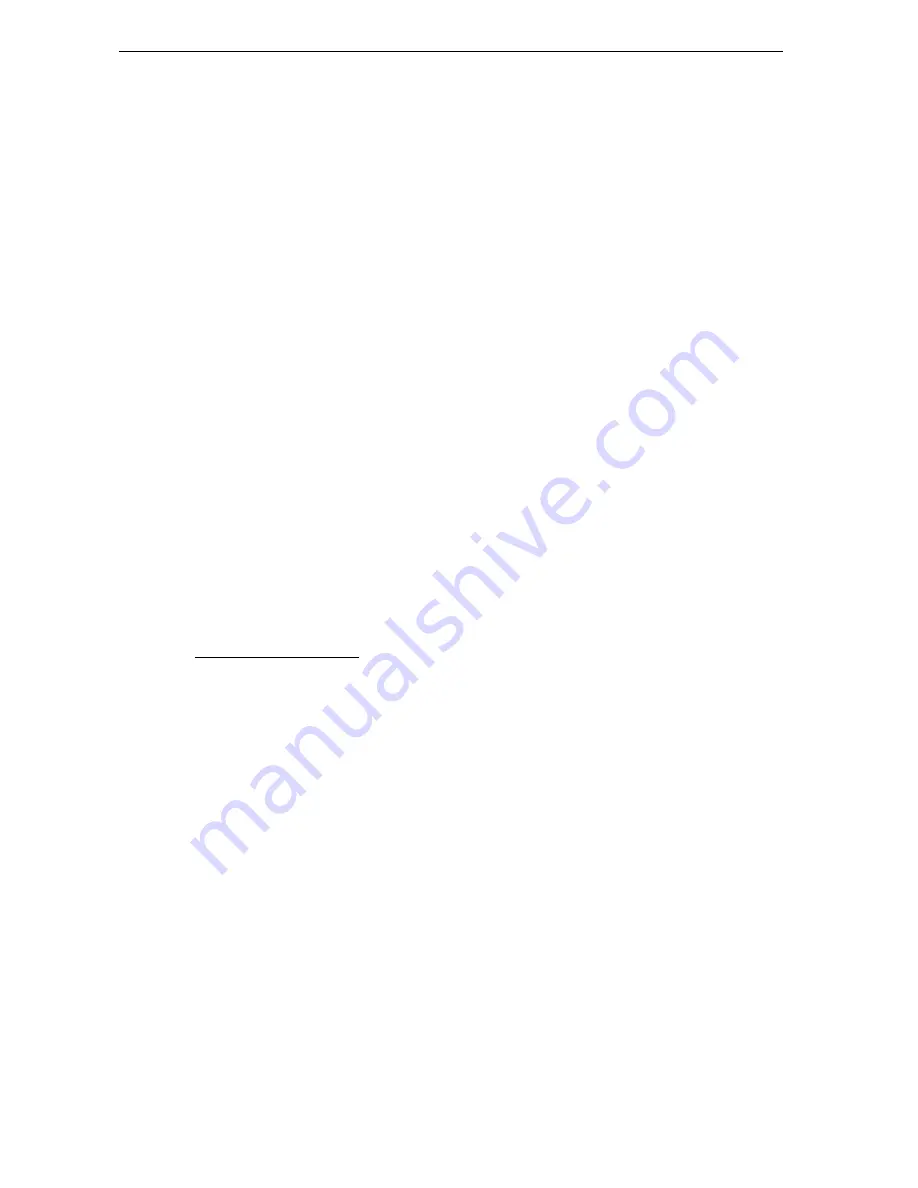
GEO
M12
HARDWARE
SETUP
PROCEDURE
Page 25/90
Ensure that motor hoists, hoist control systems and ancillary rigging components are currently certified
as safe and that they pass a visual inspection prior to use.
Ensure that public and personnel are not allowed to pass beneath the system during the installation
process. The work area should be isolated from public access.
Never leave the system unattended during the installation process.
Do not place any object, no matter how small or light, on top of the system during the installation
procedure. The object may fall when the system is flown and is likely to cause injury.
Secondary safety steels must be installed once the system has been flown to the operating height.
Secondary steels must be fitted irrespective of requirements of the local safety standards applicable to
the territory.
Ensure that the system is secure and prevented from pivoting around the motor hoist.
Avoid any form of excessive dynamic loading to the assembly (structural computations on GEO M12 &
MSUB18 Rigging System are based on a 1/1.2 factor for hoist or motor acceleration).
NEVER attach any item to the GEO M12 & MSUB18 system other than the GEO M12 & MSUB18
accessories.
When flying outdoor systems ensure that the system is not exposed to excessive wind or snow loads and
is protected from rainfall.
In case of wind greater than 8 on Beaufort scale (72km/h
– 45mph), a touring system has to be landed or
an additional securing has to be implanted.
For fixed installations, wind loading has to be taken into account in accordance to the national standards.
The GEO M12 & MSUB18 Rigging System requires regular inspection and testing by a competent test
centre. NEXO recommend that the system is load tested and certified annually or more frequently if local
regulations require.
When de-rigging the system ensure that the same duty of care is given to the procedure as for the
installation. Pack GEO M12 & MSUB18 components carefully to prevent damage in transit.
6.1.2 Ground Stacking Safety
Statistically, many more injuries occur due to unstable ground stacked PA systems than those associated
with flown systems. There are several reasons for this fact, however the message is clear:
Always survey the supporting structure upon which a ground stack is to be built. Always look beneath PA
wings to inspect the deck support and if necessary ask for the stage scrims and dressings be removed to
allow access.
If the stage surface slopes, as it does in some theatres, ensure that the system is prevented from sliding
forwards due to vibration. This may require the fitting of timber battens to the stage floor.
For outdoor systems ensure that that the system is protected from wind forces which might cause the
ground stack to become unstable. Wind forces can be huge, especially upon large systems, and should
never be underestimated. Observe meteorological forecasts, calculate the “worst case” effect upon the
system prior to erection and ensure that the system is secured appropriately.
Take care when stacking cabinets. Always employ safe lifting procedures and never attempt to build
stacks without sufficient personnel and equipment.
Never allow anyone, whether operators, artists or members of the public to climb onto a ground stacked
PA system. Anyone who needs to climb over 2m (6 ft) high should be fitted with suitable safely equipment
including a clip-on harness. Please refer to local Health and Safety legislation in your territory. Your dealer
can help with advice on access to this information.
Содержание GEO M12 Series
Страница 13: ...CONNECTION DIAGRAMS Page 13 90 3 3 GEO M12 passive mode and MSUB18 NXAMP4x1mk2 Bridge Stereo ...
Страница 14: ...Page 14 90 CONNECTION DIAGRAMS 3 4 GEO M12 passive mode NXAMP4x2mk2 3 5 MSUB18 NXAMP4x2mk2 ...
Страница 15: ...CONNECTION DIAGRAMS Page 15 90 3 6 GEO M12 passive mode and MSUB18 NXAMP4x2mk2 ...
Страница 16: ...Page 16 90 CONNECTION DIAGRAMS 3 7 GEO M12 passive mode NXAMP4x4 ...
Страница 17: ...CONNECTION DIAGRAMS Page 17 90 3 8 GEO M12 active mode NXAMP4x4 ...
Страница 18: ...Page 18 90 CONNECTION DIAGRAMS 3 9 MSUB18 Omni Mode NXAMP4x4 ...
Страница 19: ...CONNECTION DIAGRAMS Page 19 90 3 10 MSUB18 Cardio Mode NXAMP4x4 ...
Страница 20: ...Page 20 90 CONNECTION DIAGRAMS 3 11 GEO M12 passive mode and MSUB18 NXAMP4x4 ...
Страница 57: ...GEO M12 HARDWARE SETUP PROCEDURE Page 57 90 6 4 5 MSUB18 and GEO M12 flown with Touring Bumper ...
Страница 73: ...TECHNICAL SPECIFICATIONS Page 73 90 8 3 3 VNT EXBARM12 Parts X1 X 2 Dimensions Weight 11 kg 25 4 lb ...
Страница 74: ...Page 74 90 TECHNICAL SPECIFICATIONS 8 3 5 VNT GSTKM10M12L Parts X1 Dimensions Weight 9 7 kg 19 8 lb ...
Страница 75: ...TECHNICAL SPECIFICATIONS Page 75 90 8 3 6 VNT GSTKM10M12S Parts X1 Dimensions Weight 7 kg 15 4 lb ...
Страница 76: ...Page 76 90 TECHNICAL SPECIFICATIONS 8 3 7 VNT MNSTKM12 Parts X1 Dimensions Weight 3 kg 6 6 lb ...
Страница 77: ...TECHNICAL SPECIFICATIONS Page 77 90 8 3 8 GMT LBUMPM12 Parts X1 X1 Dimensions Weight 10 5 kg 23 1 lb ...
Страница 78: ...Page 78 90 TECHNICAL SPECIFICATIONS 8 3 9 GMT EXBARM12L Parts X1 X2 X2 X1 Dimensions Weight 9 7 kg 21 4 lb ...
Страница 79: ...TECHNICAL SPECIFICATIONS Page 79 90 8 3 10 GMT FLGM12 Parts X1 Dimensions Weight 1 kg 2 2 lb ...
Страница 80: ...Page 80 90 TECHNICAL SPECIFICATIONS 8 3 11 MST WBMSUB18 Parts X1 Dimensions Weight 7 2 kg 15 9 lb ...
Страница 81: ...TECHNICAL SPECIFICATIONS Page 81 90 8 3 12 MST DOLLYMSUB18 Parts X1 Dimensions Weight 10 kg 22 lb ...
Страница 82: ...Page 82 90 TECHNICAL SPECIFICATIONS 8 3 13 MST COVMSUB18 Parts X1 Weight 2 2 kg 5 lb ...
Страница 83: ...TECHNICAL SPECIFICATIONS Page 83 90 8 3 14 MST COV2MSUB18 Parts X1 Weight 3 5 kg 7 7 lb ...
Страница 84: ...Page 84 90 TECHNICAL SPECIFICATIONS 8 3 15 GMT 2CASEM12 Parts X1 Dimensions Weight 35 kg 77 lb ...
Страница 85: ...TECHNICAL SPECIFICATIONS Page 85 90 8 3 16 GMT 3CASEM12 Parts X1 Dimensions Weight 56 kg 123 lb ...