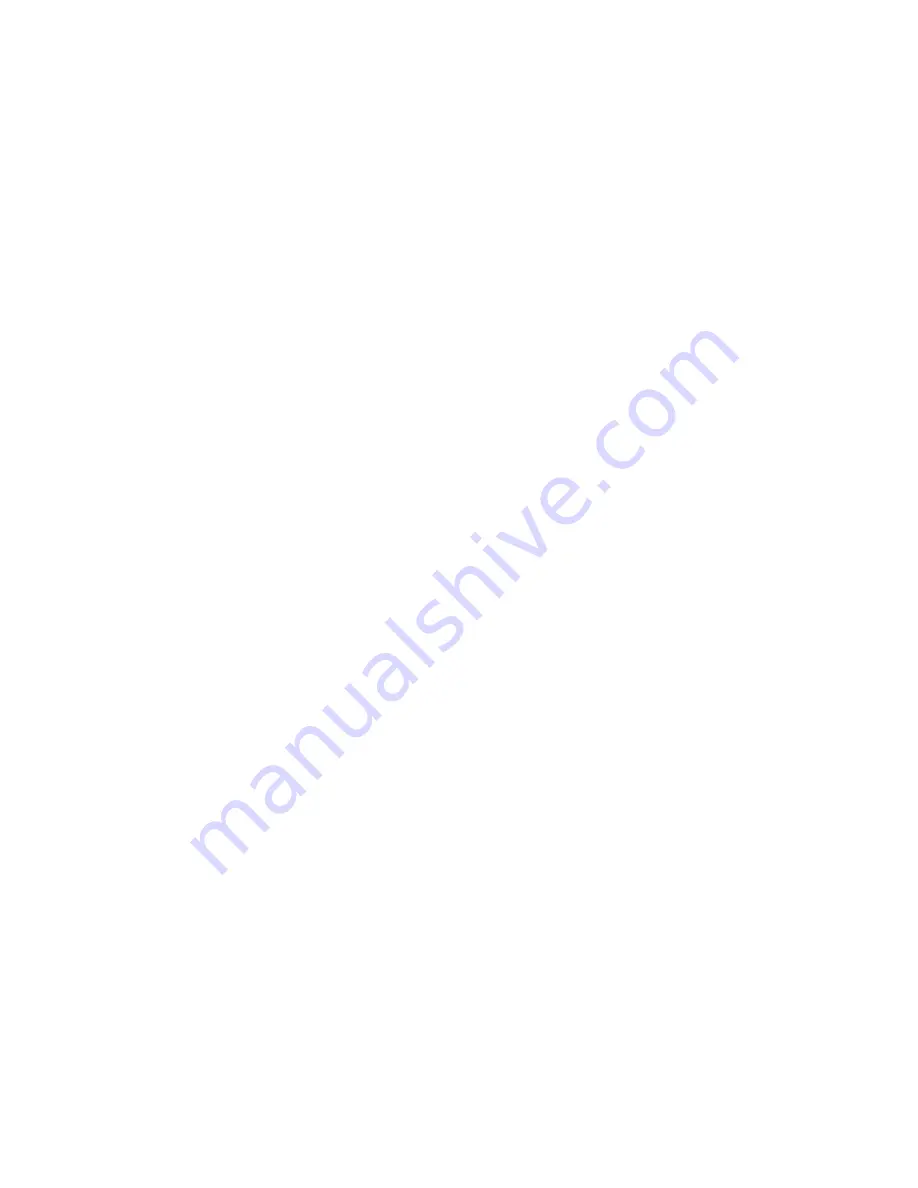
13
AIR FILTERS
Air filters should be inspected monthly and changed as required. At least two changes are usually
required during the heating season—more may be necessary if dusty conditions exist. Remove the filter
gently to prevent dust spillage. Install filters of the same size and type. Check filter markings for correct
orientation.
BLOWER REMOVAL
Disconnect power before removing or servicing the blower. Remove the burner and blower access panels
on the front of the furnace. Remove the nut and bolt that fastens the blower locking plate to the fan
partition and slide the blower locking plate out. The blower is mounted on slide rails which allow it to be
pulled forward for servicing. The wiring harness has sufficient length so that it can be removed without
disconnecting the motor leads. If the capacitor leads need to be removed, short the terminals with an
insulated screwdriver before handling.
BLOWER ADJUSTMENT
This unit is designed for a maximum temperature rise through the furnace of 85
o
F at a maximum external
static pressure of 0.50 inches of water column. However, due to the wide range of static pressures in duct
systems, it is the responsibility of the installer to verify that the temperature rise does not exceed 85
o
F. To
measure the actual temperature rise let the unit operate for at least five minutes. Insert a thermometer
and note the temperature of the warm air supply at a point at least 24 inches upstream from the heat
exchanger surface. Next measure the temperature at the return air grill and take the difference. Air
temperature rise can be lowered by increasing the blower speed; lowering the firing rate; or increasing
undersized supply and return air free area. The furnace will not operate properly and its life will be
decreased if insufficient air quantity passes over the heat exchanger. Similarly, too much air during
heating mode resulting in a temperature rise of less than 65
o
F may cause heat exchanger degradation
due to condensation.
DIRECT DRIVE BLOWER
The installer should select the best speed tap for the specific installation. Recommended speed taps for
heating are given in TABLES 1 (NH3) AND 3 (LFR) GENERAL INSTRUCTIONS. The motor RPM will
vary over a range of static pressures. The blower heating speed can be changed by moving the black wire
harness lead to another speed tap on the terminal block located inside the blower compartment. Refer to
TABLES 2 (NH3) and 4 (LFR), BLOWER PERFORMANCE for airflow data. A second speed for non-
heating modes can be selected using the red wire harness lead. See FIG. 13 and 14 for WIRING
SCHEMATICS.
BELT DRIVE BLOWER – NH3 only
The air delivery (CFM) and temperature can be varied by adjusting the motor pulley. Closing the pulley
increases blower speed and decreases temperature rise. Opening the pulley decreases the blower speed
and increases the temperature rise. A 6 inch diameter blower pulley is required for 0.20 inch w.c. static
pressure. A 5 inch diameter pulley is used for 0.20 inch w.c. static pressure. Correct belt tension allows a
1 inch deflection midway between the pulleys. Too much tension will overload the motor—too little tension
will cause slippage.
Pulley combinations vary according to the fuel input and duct static pressure. Recommended pulley
combinations for heating mode are given in TABLE 1 (NH3), GENERAL INSTRUCTIONS. Refer to
TABLE 2 (NH3), BLOWER PERFORMANCE for air flow data.
An optional two-speed motor is available. The low speed can be used in non-heating mode. If the unit is
not factory wired for a two-speed motor, connect the red wire of the blower wire harness to the correct
motor lead. See FIG. 15 for STANDARD WIRING SCHEMATIC - BELT DRIVE and follow the motor
manufacturer’s instructions. Make sure replacement and retrofit belt drive motors meet or exceed the
OEM motor specifications. Two speed belt drive motors are available from Newmac.
Содержание LFR-72
Страница 17: ...16 FIG 10 TYPICAL OIL TANK PIPING INSTALLATIONS...
Страница 18: ...17 FIG 11 DIMENSIONS CONTROL LOCATION NH3...
Страница 19: ...18 FIG 12 LFR SET UP...
Страница 20: ...19 FIG 13 STANDARD WIRING SCHEMATIC DIRECT DRIVE...
Страница 21: ...20 FIG 14 STANDARD WIRING SCHEMATIC A C READY DIRECT DRIVE...
Страница 22: ...21 FIG 15 STANDARD WIRING SCHEMATIC BELT DRIVE...
Страница 24: ...23 FIG 16 NH3 EXPLODED ASSEMBLY...
Страница 33: ...32 FIGURE 23 COMMON CHIMNEY DRAFT PROBLEMS...