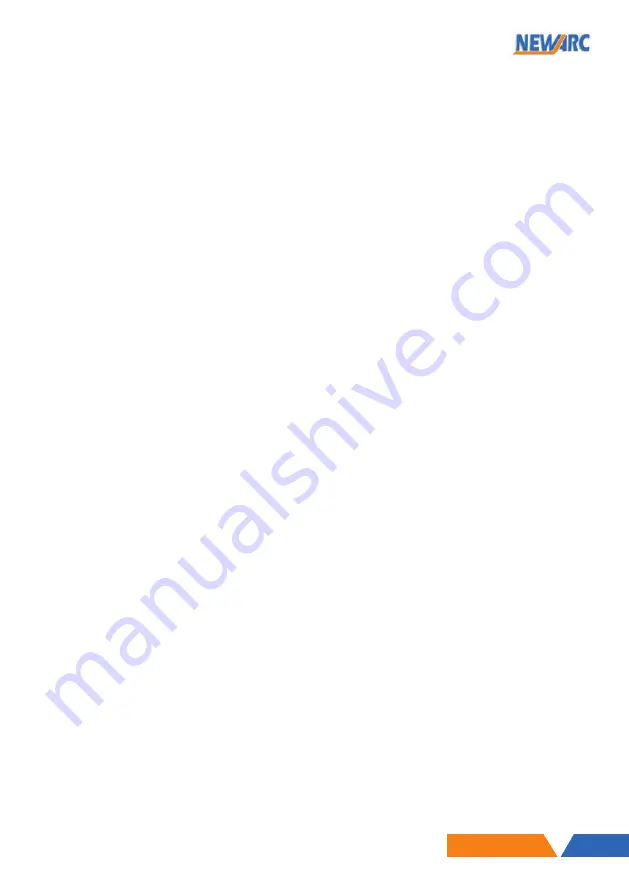
WFU12-4C
17
Fitting wire spool
The feed rollers must always be selected to match the size of the electrode wire being used. The feed
rollers fitted to the wire-feeders normally have two different sized grooves.
• Make sure that the outlet wire guide located inside the torch adapter is of the correct size for the wire
being used.
• Open the pressure lever on the wire drive assembly.
• Remove the retaining nut on the spool holder and fit wire spool so that the locating pin on the spool
holder fits into corresponding hole in the wire reel.
• Replace the retaining nut on the spool holder.
• Release the end of the wire from the spool and cut off the bent length, take care that the wire does not
spill off the spool
• Insert the wire through the rear wire guide, over the drive rollers and through the outlet wire guide so
that approximately 5cm of wire is protruding from the torch adapter.
• Close the pressure roller ensuring that the wire lays in the drive roll groove.
Connecting the Welding Torch
• Make sure that the liner and contact tip fitted to the torch are of the correct size for the wire being used.
• Attach the welding torch to the torch adapter on the wire feed, making sure that the torch liner
retaining nut goes over the wire protruding from the torch adapter.
• Line all the connections on the torch up with their relevant sockets in the torch adapter and screw the
torch onto the wire feeder.
NOTE!
The torch should screw easily onto the wire feeder, if any resistance is felt - do not force the torch
onto the wire feeder.
Feeding the Wire through the torch
• Set the wire feed speed control to about half way.
• Keeping the welding torch as straight as possible press the wire inch button until the wire is fed
through the torch and out through the contact tip.
• The wire pressure lever adjuster should be set so that when the wire is restricted at the welding torch
the drive rollers will slip. Setting the tension too high may cause the wire to build up inside the wire
drive assembly as well as cause excessive loading of the motor which will result in a reduced duty cycle.
Adjusting Brake Tension
• Remove the spool-retaining nut.
• The head of the brake adjusting screw is now visible in the centre of the spool holder.
• Turn the screw clockwise to tighten the brake and anti-clockwise to slacken it.
• It is advisable to check the tension every time a new spool of wire is fitted as it is the extra weight of a
full spool that generally causes problems with the spool over-running and wire spilling off the spool.
Connecting the Gas Hose
A Gas hose suitable for use with Argon or CO2 up to a pressure of 10 bar (150 psi) should be connected
between the pressure regulator on the gas cylinder and the gas connection on the rear of the wire feed
unit. Do not over-tighten this connection.
NOTE!
The pressure regulator should be set between approximately 3 and 5 bar for normal use.