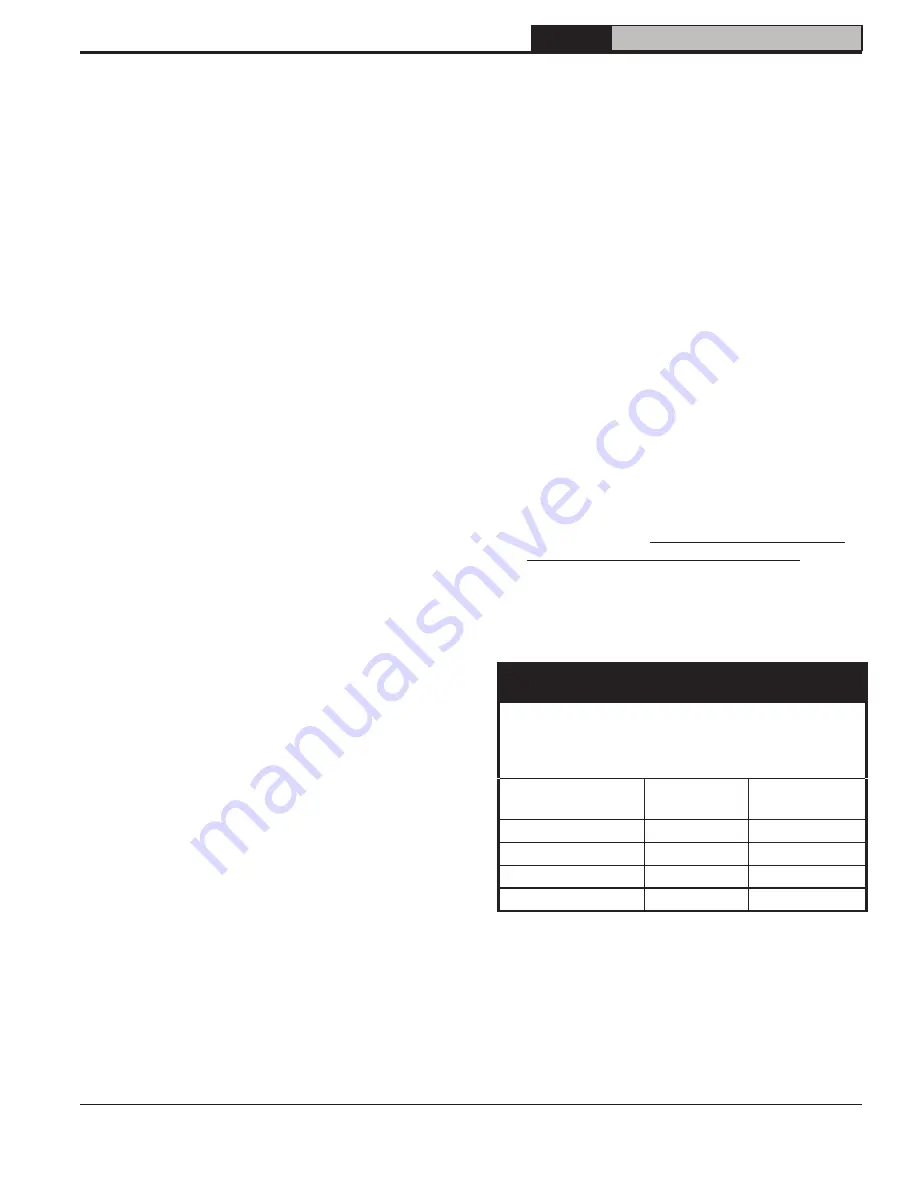
33
111079-01 - 12/20
FR
Installation & Service Manual
A. WATER BOILERS:
1.
Filling of boiler and system.
GENERAL
—
In a hot water heating system,
the boiler and entire system (other than the
expansion tank) must be full of water for
satisfactory operation. Water should be added
to the system until the boiler pressure gauge
registers 12 psi. To insure that the system is
full, water should come out of all air vents when
opened.
2. BOILING OUT OF BOILER AND SYSTEM
.
The
oil and grease which accumulate in a new hot
water boiler can be washed out in the following
manner:
a. Remove relief valve using extreme care to
avoid damaging it.
b. Add an appropriate amount of
recommended boil out compound.
c. Replace relief valve.
d. Fill the entire system with water.
e. Start firing the boiler.
f. Circulate the water through the entire
system.
g. Vent the system, including the radiation.
h. Allow boiler water to reach operating
temperature, if possible.
i. Continue to circulate the water for a few
hours.
j. Stop firing the boiler.
k. Drain the system in a manner and to a
location that hot water can be discharged
with safety.
l. Remove plugs from all available returns
and wash the water side of the boiler as
thoroughly as possible, using a high-
pressure water stream.
m. Refill the system with fresh water.
3. Add appropriate boiler water treatment
compounds as recommended by your
qualified water treatment company.
4. Make pH or Alkalinity Test.
After boiler and system have been cleaned
and refilled as previously described, test the
pH of the water in the system. This can easily
be done by drawing a small sample of boiler
water and testing with hydrion paper which
is used in the same manner as litmus paper,
except it gives specific readings. A color chart
on the side of the small hydrion dispenser
gives the reading pH. Hydrion paper is
inexpensive and obtainable from any chemical
supply house or through your local druggist.
The pH should be higher than 7 but lower
than 11. Add some of the washout chemical
(caustic soda), if necessary, to bring the PH
within the specified range.
5. Boiler is now ready to be put into service.
B. EXCESSIVE MAKE-UP WATER
A leaky system will increase the volume of
make-up water supplied to the boiler, which can
significantly shorten the life of the boiler. Entrained
in make-up water are dissolved minerals, salts
and oxygen. When the fresh, cool make-up
water is heated in the boiler, the minerals fall
out as sediment, the salts coat the inside of the
boiler, and the oxygen escapes as a gas. The
accumulation of sediment eventually isolates the
water from contacting the cast iron. When this
happens the cast iron in that area gets extremely
hot and eventually cracks. The presence of free
oxygen or chloride salts in the boiler corrodes the
cast iron from the inside. More make-up water and
higher concentrations of contaminants damage
the boiler sooner. Our warranty does not cover
corrosion and sediment-related damage. Clearly
it is in everyone’s best interest to prevent this type
of failure. You can do your part by ensuring that
your system is leak-free, keeping leakage to less
than 2 percent of the boiler water volume each
month. Refer to Chart below.
IMPORTANT
IMPORTANT
IF, DURING NORMAL OPERATION, IT IS NECESSARY
TO ADD MORE WATER THAN INDICATED BELOW,
CONSULT A QUALIFIED SERVICE TECHNICIAN
TO CHECK YOUR SYSTEM FOR LEAKS.
Boiler Series
Gallons Per
Month
Gallons Per
Year
FR-HGS
0.2
2.4
FR-122
0.4
4.8
FR-147/173
0.8
9.6
FR-205/232
0.9
10.8
C. ATTENTION TO BOILER WHILE NOT IN
OPERATION
1. IMPORTANT
IF BOILER IS NOT USED DURING WINTER
TIME, IT MUST BE FULLY DRAINED TO
PREVENT FREEZE DAMAGE.
2. Spray inside surfaces with light lubricating or
crankcase oil using gun with extended stem so
as to reach all corners.
10
Maintenance and Service Instructions