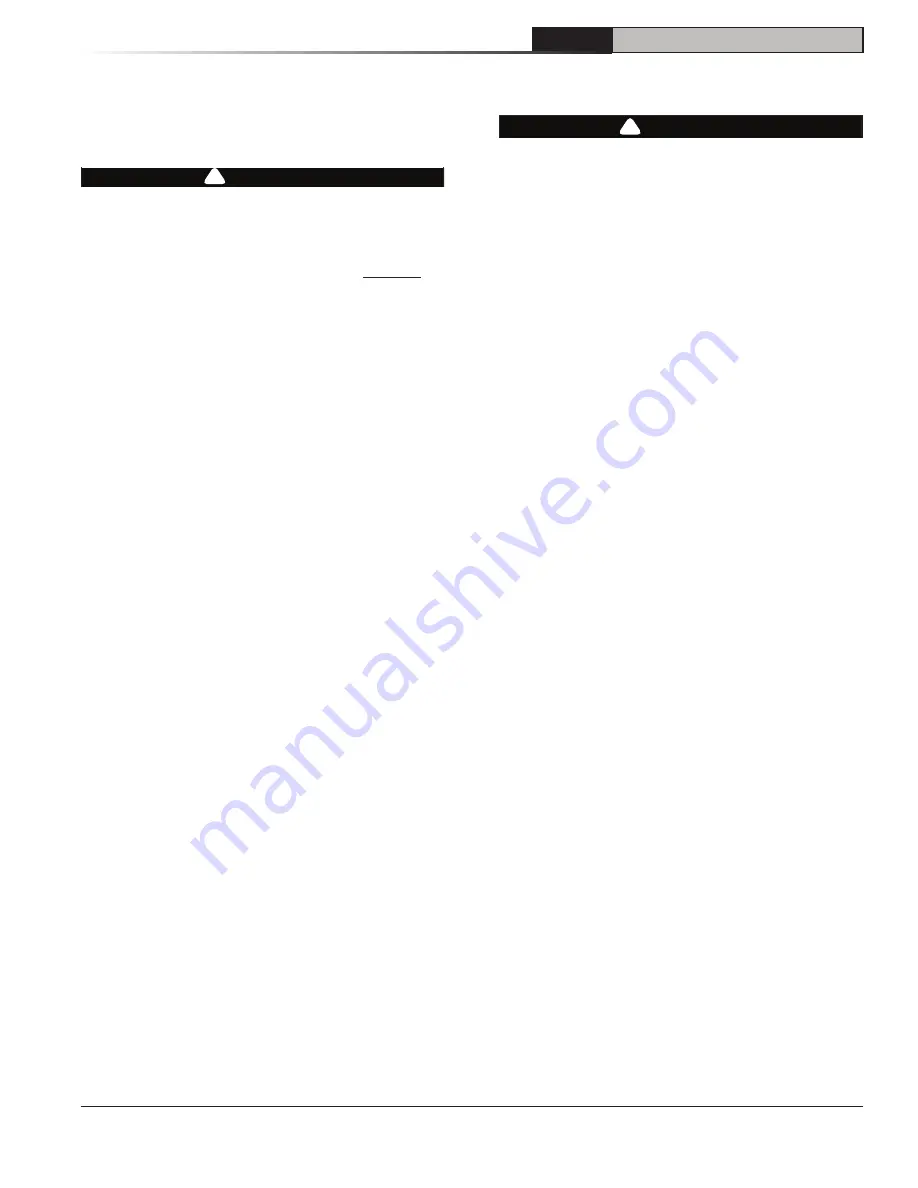
11
110772-01 - 5/20
CL
Installation & Service Manual
A. CONNECT TANKLESS HEATER PIPING as
shown in Figure 4-1. See Table 4-2 for Tankless
Heater Rating.
THE FOLLOWING GUIDELINES SHOULD BE
FOLLOWED WHEN PIPING THE TANKLESS
HEATER:
1. FLOW REGULATION — If flow through the
heater is greater than its rating, the supply of
adequate hot water may not be able to keep
up with the demand. For this reason a flow
regulator matching the heater rating should
be installed in the cold water line to the heater.
The flow regulator should preferably be located
below the inlet to the heater and a minimum of
3’ away from the inlet so that the regulator is
not subjected to excess temperatures that may
occur during “off” periods when it is possible
for heat to be conducted back through the
supply line. The flow regulator also limits
the flow of supply water regardless of inlet
pressure variations in the range of 20 to 125
psi.
2. TEMPERING OF HOT WATER — Installation
of an automatic mixing valve will lengthen the
delivery of the available hot water by mixing
some cold water with the hot. This prevents
the possibility of scalding hot water at the
fixtures. In addition, savings of hot water will be
achieved since the user will not waste as much
hot water while seeking a water temperature.
Higher temperature hot water required by
dishwashers and automatic washers is
possible by piping the hot water from the
heater prior to entering the mixing valve. The
mixing valve should be “trapped” by installing
it below the cold water inlet to heater to prevent
lime formation in the valve. Refer to Figure 4-1.
3. FLUSHING OF HEATER — All water
contains some sediment which settles on the
inside of the coil. Consequently, the heater
should be periodically back washed. This
is accomplished by installing hose bibs as
illustrated and allowing water at city pressure
to run into hose bib A, through the heater, and
out hose bib B until the discharge is clear. The
tees in which the hose bibs are located should
be the same size as heater connections to
minimize pressure drop.
4. HARD WATER — A water analysis is
necessary to determine the hardness of your
potable water. This is applicable to some
city water and particularly to well water.
An appropriate water softener should be
installed based on the analysis and dealer’s
recommendation. This is not only beneficial to
the tankless heater but to piping and fixtures
plus the many other benefits derived from soft
water.
WARNING
Install automatic mixing valve at tankless heater
outlet to avoid risk of burns or scalding due
to excessively hot water at fixtures. Adjust
and maintain the mixing valve in accordance
with the manufacturer's instructions. DO NOT
operate tankless heater without mixing valve.
NOTICE
During summertime operation, the
normal water line on a steam boiler can be raised
1", from 22-5/8" to 23-5/8" (see Figure 1-1) for
improved tankless heater performance on steam
boilers.
Use street elbow fittings in tankless in and out
connections to assure adequate clearance of
piping.
4
Tankless and Indirect Water Heater Piping
CAUTION
Use of hard water with a tankless coil will, over
a short period of time, reduce the output of the
coil, reduce flow due to increased pressure
drop and reduce the useful life of the coil.
!
!
Содержание CL3-105SE
Страница 34: ...34 110772 01 5 20 CL Installation Service Manual This Page is Intentionally Blank...
Страница 36: ...36 110772 01 5 20 CL Installation Service Manual Bare Boiler Assembly 13 Service Parts continued...
Страница 38: ...38 110772 01 5 20 CL Installation Service Manual CL Steam Boilers Trim and Controls 13 Repair Parts continued...