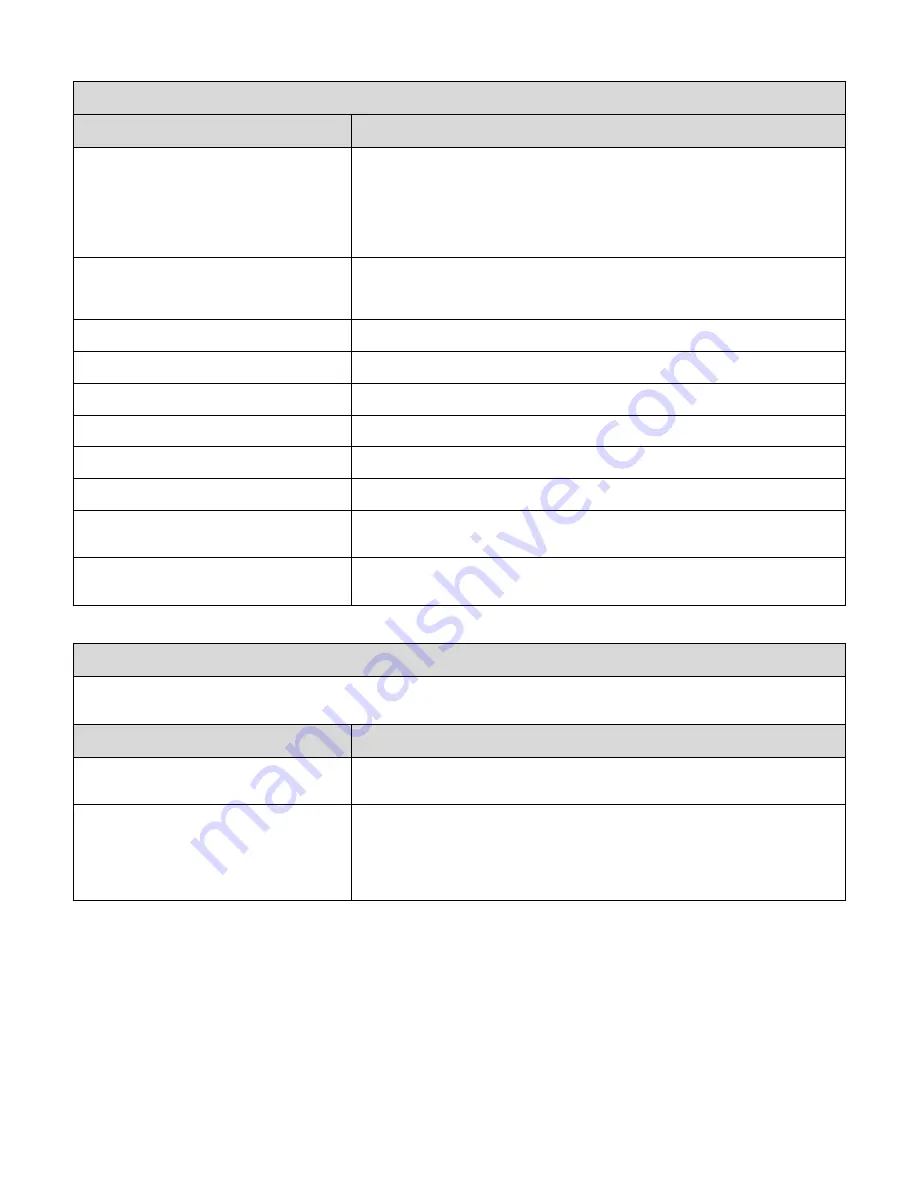
© 2016 Nelson Stud Welding, Inc.
Page 20
All Rights Reserved.
February 2016
Part No. 729-110-042 v1.03
Problem: Cold Weld
Possible Causes
Possible Solutions
Tip on stud is crushed due to excessive
pressure. Occasionally (especially with
aluminum studs), an operator can apply
repeated pressure to the timing tip and
crush or shorten the tip. The shortened tip
reduces arc length/time and does not
properly melt the stud and/or base material.
Ensure plunge is properly adjusted. Refer to Sections 3.3 and 8.4.
Coiled weld or ground cables. This reduces
weld current delivered to the stud. The
coiled cables act like a large inductor and
inhibit the flow of energy.
Ensure weld and ground cables are not coiled during the stud welding process.
Improperly set power supply controls.
Refer to the Section 3 Normal Operation within the Operating the Capacitor
Discharge NCD+ Stud Welding Unit manual.
Improperly formed tip on stud due to
manufacturing process.
Replace stud with one that is correctly formed.
Changes in alloys being welded.
Changes in alloys can usually be compensated for by changing the settings on
the power supply.
Equipment failure.
Refer to the
Section 3 Normal Operation
within the Operating the Capacitor
Discharge NCD+ Stud Welding Unit manual.
Improperly set plunge setting.
Decrease or increase the plunge. Refer to Sections 3.3 and 8.4.
Varying gauges of sheet metal.
Changes in sheet metal can usually be compensated for by changing the
settings on the power supply.
Springs inside weld tool have fatigued and
don’t apply the same pressure.
Return weld tool to Nelson for service.
Dirt inside weld tool prevents smooth
operation and hangs up or slows gun
operation.
Clean weld tool in accordance with section 5.1.
Problem: Arc Blow
Characterized by weld spatter of fillet on only one side of the stud (looks like molten metal was “blown” out from only the one
side of the stud). This problem will often cause incomplete fillet formation on one side of the stud. This incomplete cross
sectional welding may lead to weld failure.
Possible Causes
Possible Solutions
Molten metal runs away from the ground.
Incomplete or insufficient grounding can
cause this problem.
Double Ground. The addition of another ground on opposite sides of the weld
area will reduce this problem. The object will be to always weld between the
grounds. If you need assistance contact your Nelson Representative.
Welding near the edge (1/4 inch or less) of
a piece of metal will potentially cause these
phenomena. Unusual electrical current
patterns are set up near the edges of
metals and this can affect the flow of
molten metal
.
Place another piece of sheet metal of the same type and thickness next to the
edge you are welding. This will “fool” the electrical currents and they will act like
you are welding in the middle of the sheet metal.