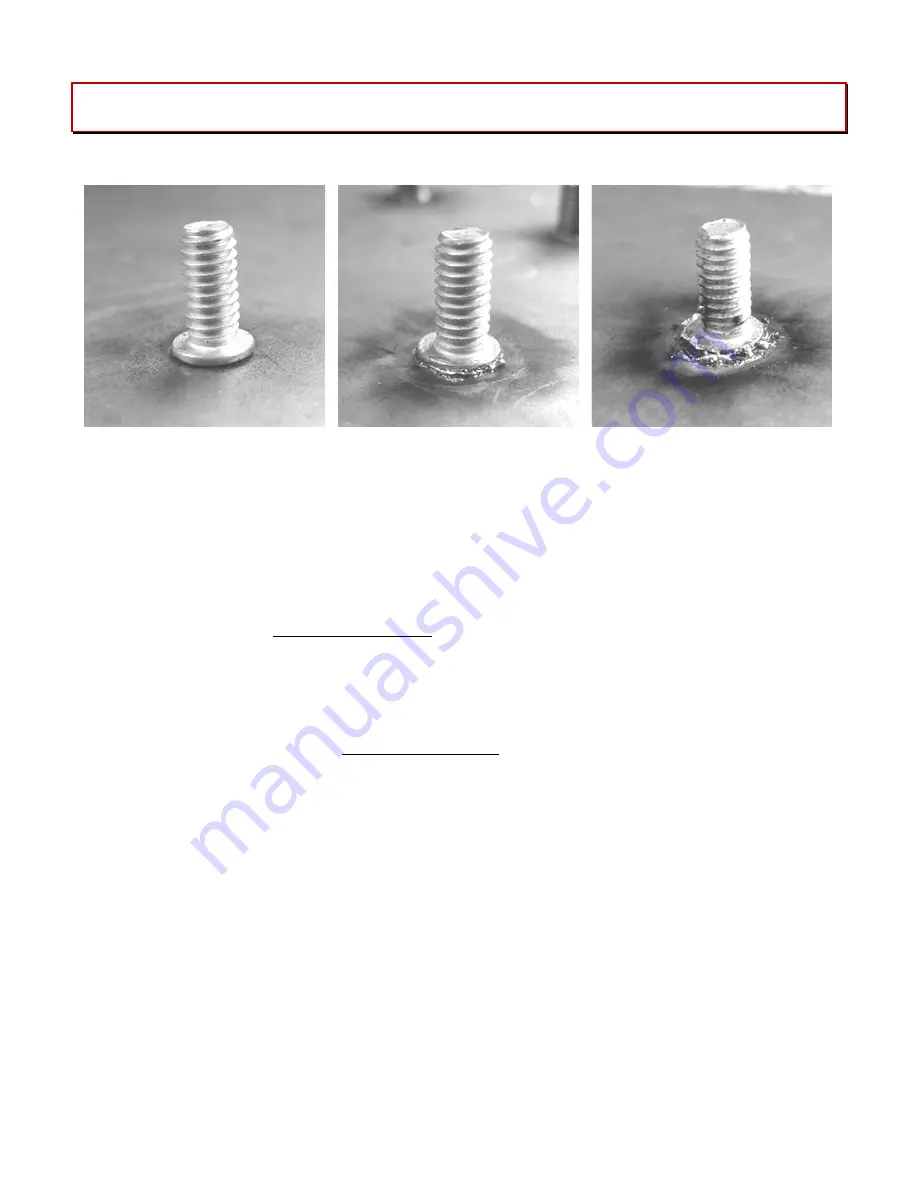
© 2016 Nelson Stud Welding, Inc.
Page 18
All Rights Reserved.
February 2016
Part No. 729-110-042 v1.03
6 Troubleshooting
6.1 Visual Weld Inspection and Weld Parameter Adjustments
Situation:
Cold Weld
Situation:
Acceptable Weld
Situation:
Hot Weld
Figure 6.1 Weld Quality Visual Inspection
6.2 Weld Quality Physical Inspection and Weld Parameter Adjustments
If visually inspecting the welds reveals a questionable weld, the weld should be physically tested. Initial weld set
ups should also be physically tested.
Suggested physical tests for steel and stainless steel studs are as follows:
4
Bend Test.
Stud to be tested shall be bent away from its vertical axis 90° or until failure. Failure should occur
in the stud shank, or, on thin plate, a full stud diameter plug of base metal should be torn out.
5
Torque Test.
Stud shall be torqued until a pre- specified loading is attained or until the stud fails. On thin
plate, a plug of the base material should tear out.
Physical test procedures for inspecting (magnesium) aluminum alloy studs are:
1.
Bend Test.
The stud to be tested shall be bent, using a bending tool approximately 15° away from its vertical
axis before the stud breaks in the shank or the base material fails.
2.
Torque Test
. The stud to be tested shall be torqued in the conventional manner by applying torque until a
predetermined torque load is reached or the stud fails.
6.2.1
Recommendations
Before starting any stud welding operation, or after the equipment has remained idle for a period of time, trial or
test studs should be welded to a plate for testing. Testing should continue until there is no failure of a test stud.
NOTE: Do not bend aluminum studs by striking with a hammer, always use a bending tool. The stud weld should not
be damaged, only the stud shank or the base material.