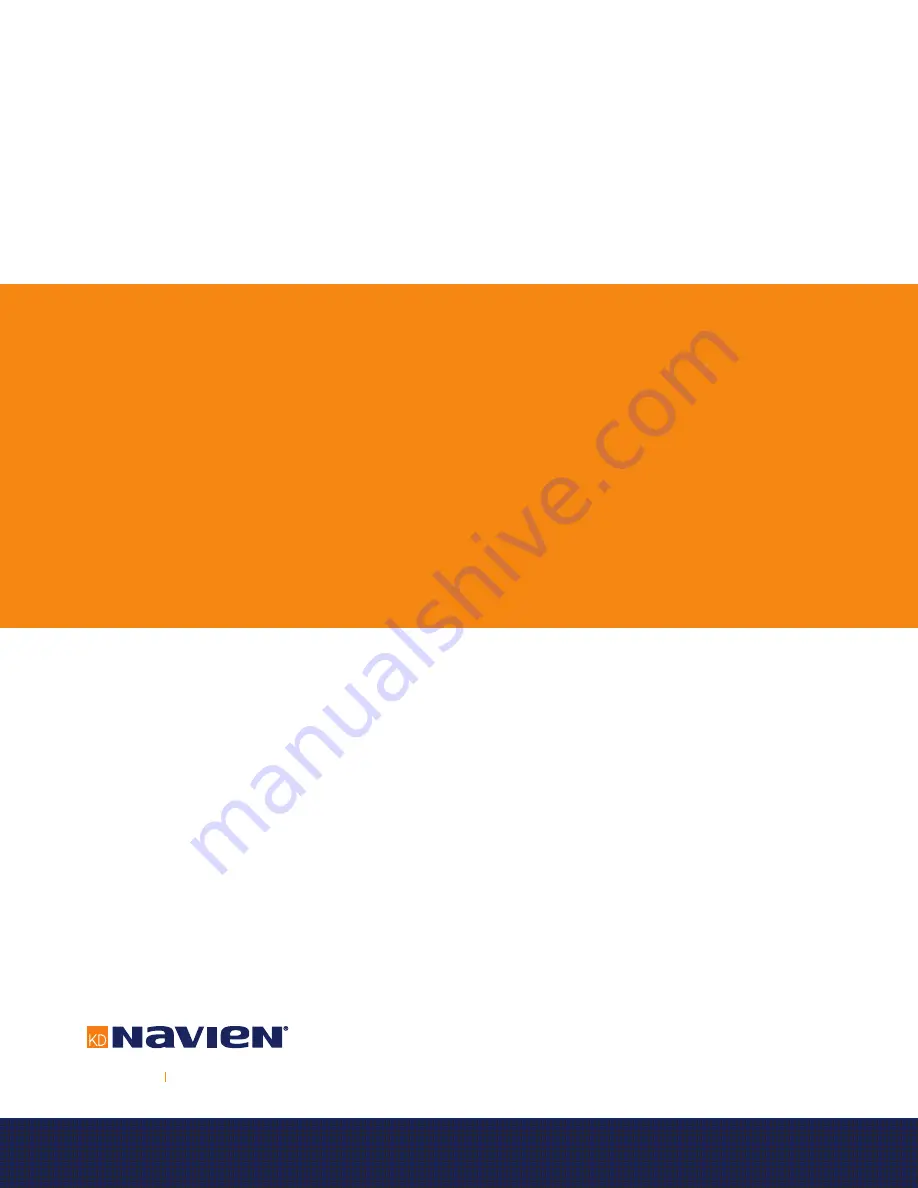
Getting Service
If your boiler requires service, you have several options for getting service:
●
Contact Technical Support at 1-800-519-8794 or on the website: www.navien.com.
●
For warranty service, always contact Technical Support first.
●
Contact the technician or professional who installed your boiler.
●
Contact a licensed professional for the affected system (for example, a plumber or electrician).
When you contact Technical Support, please have the following information at hand:
●
Model number
●
Serial number
●
Date purchased
●
Installation location and type
●
Error code, if any appears on the front panel display.
Navien, Inc
800.519.8794 www.Navien.com
20 Goodyear lrvine, CA 92618
Service Manual
NHB Condensing Boilers
T H E L E A D E R I N C O N D E N S I N G T E C H N O L O G Y
Version: 1.00 (Mar.22.2015)
Содержание NHB-055
Страница 62: ...62 NHB Service Manual Version 1 0 4 7 Ladder Diagram...
Страница 142: ...142 NHB Service Manual Version 1 0 Memo...
Страница 143: ...NHB Service Manual 143 Version 1 0 Memo...
Страница 144: ...144 NHB Service Manual Version 1 0 Memo...
Страница 145: ...NHB Service Manual 145 Version 1 0 Memo...
Страница 146: ...146 NHB Service Manual Version 1 0 Memo...