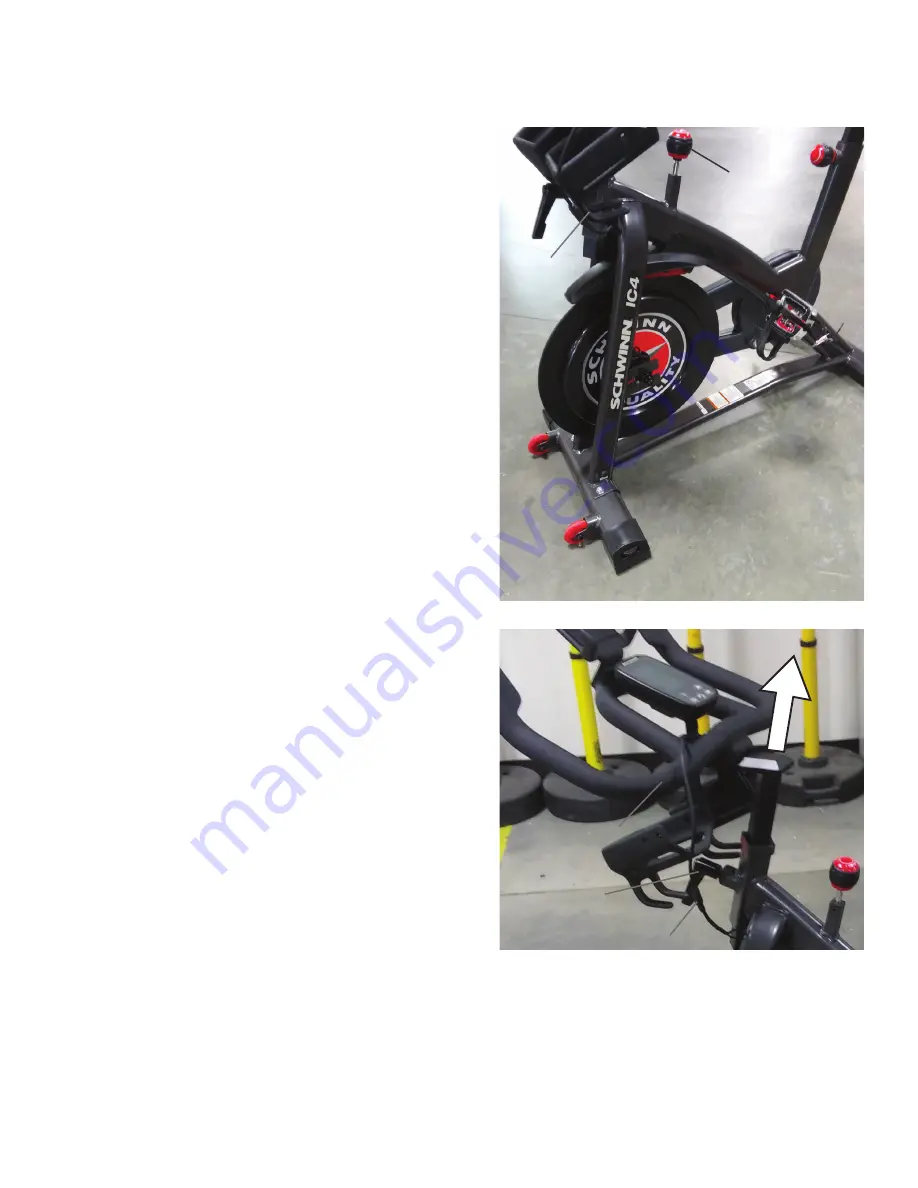
58
Note:
Your machine may not match the images provided exactly.
1.
Unplug the AC Adapter from the wall outlet and machine.
2.
Fully turn the Resistance Knob clockwise to lock the Flywheel into
place.
3.
Remove the Dumbbells from the Handlebars if they are in place on
the Dumbbell Rack.
4.
If only replacing the Seat Post Bushing, skip to Step 15.
5.
Disconnect the Cables that connect the Console to the Frame
Assembly.
NOTICE:
Do not crimp any cables.
6.
Being prepared to support the Handlebars, loosen the Handlebar
Post Adjustment Handle and remove the Handlebar Assembly from the
Frame Assembly. Set the Handlebar Assembly safely aside away from the
work area.
7.
Remove the Handlebar Post Adjustment Handle from the Frame
Assembly.
Resistance Knob
Dumbbell
Rack
Console Cable Connection
Handlebar Post
Adjustment Handle
Handlebar Assembly