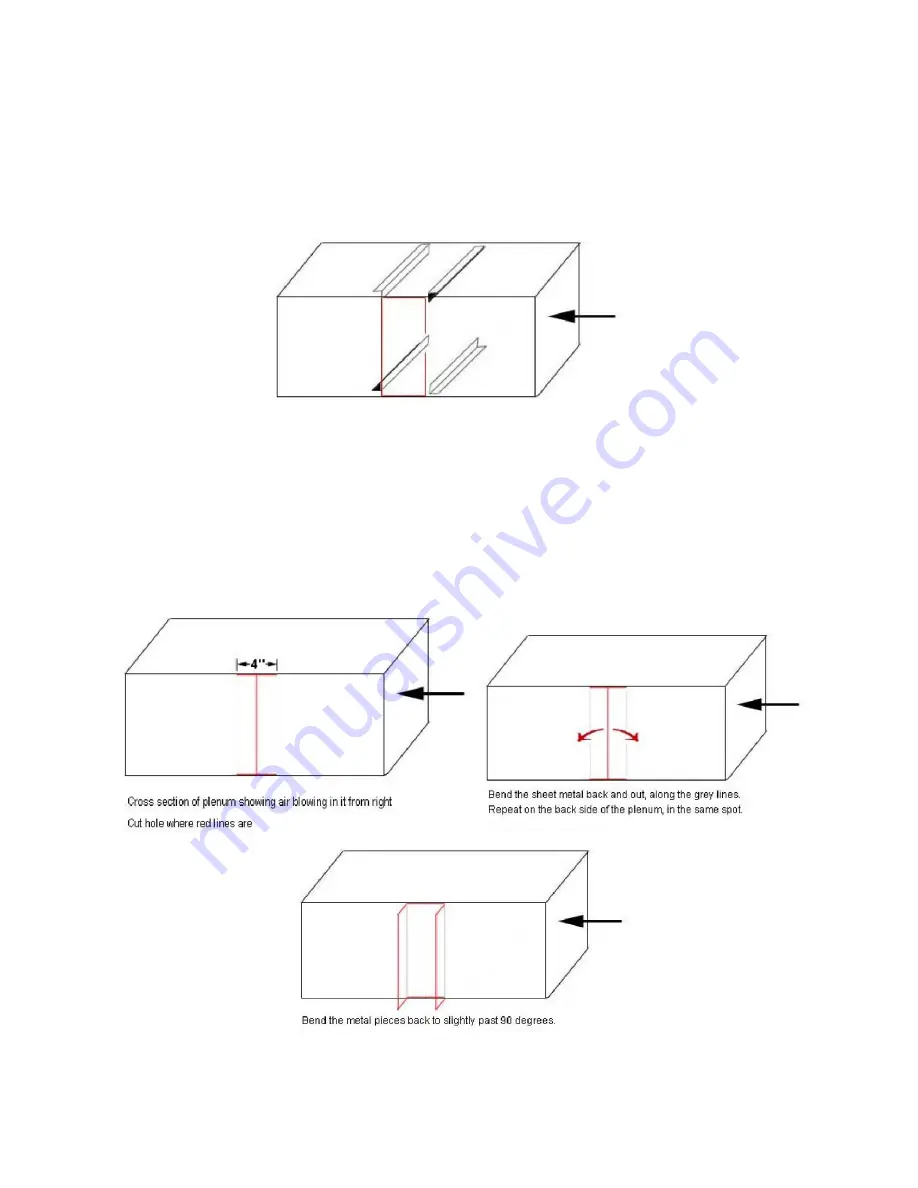
Page
15
of
31
Slide the heat exchanger into the hole for a test fit. Ideally the header and tubes (F) should stick out
of the plenum.
While test fitting try to determine how much tape is needed around the frame of the heat exchanger
to seal and keep air from flowing around it. A different amount (thickness) may be needed on
different sides.
The heat exchanger must be secured
so it won’t move
up or downstream in the plenum. Fabricate
some
‘L’ shaped braces
and install the proper width apart as shown below (Dimension C). Secure
in place using pop rivets or self tapping screws.
Slide the heat exchanger carefully into the plenum to check the fit again. Once proper fitting is
verified, you can seal off the ends of the heat exchanger and the hole you made in the plenum with
foil or duct tape.
I. Installing In A Small Plenum
You can install a heat exchanger in a plenum that is smaller than the length of the heat exchanger
as follows. Make cuts at the top and bottom of the plenum, usually 4 inches long (the width of the
heat exchanger) as shown below. You may need to do this on both sides of the ductwork
depending on the heat exchanger size.
Slide the heat exchanger through the front hole to the back hole so it protrudes out the front and
back of the plenum the same amount. Ideally the core of the heat exchanger will be entirely within
the plenum.