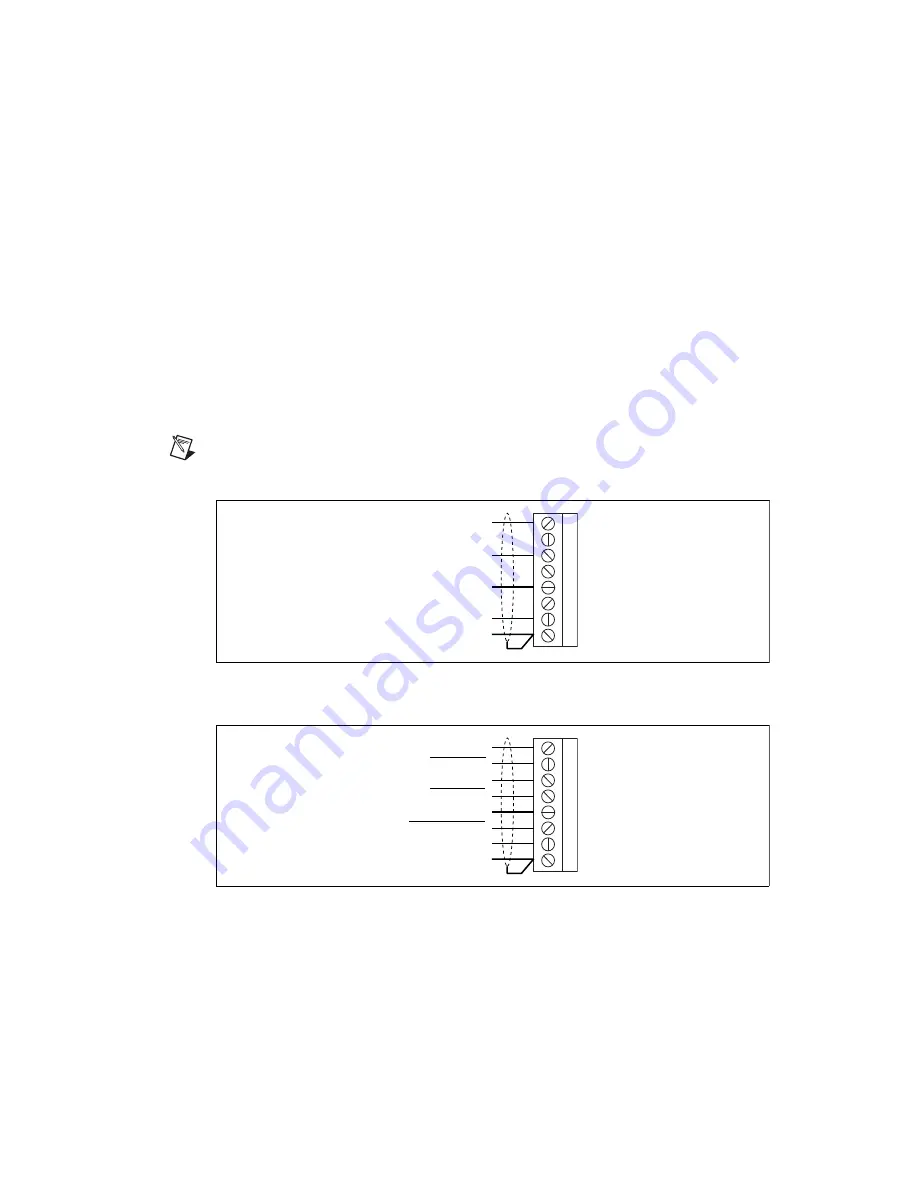
©
National Instruments Corporation
19
MID-7654/7652 Servo Power Motor Drive User Guide
5.
Plug the servo motor cables into the servo motor terminals of the MID-7654/7652. The cables must
be placed over the bottom mounting plate of the rear guard.
6.
Re-attach the protection cover
a.
Insert the tab of the protection cover, shown in Figure 9, into the slot on the bottom mounting
plate.
b.
Lower the protection cover over the servo motor cables and secure it to the side of the bottom
mounting plate using the two screws you removed in step 4.
7.
Ensure that the rear guard is held securely in place before reconnecting your MID-7654/7652 to a
power outlet.
Encoder Terminal Blocks
For quadrature incremental encoder signals, each MID-7654/7652 axis has a separate 8-position
removable screw terminal block. Where applicable, the MID-7654/7652 accepts two types of encoder
signal inputs: single-ended (TTL) or differential line driver. You can accommodate open-collector
output encoders by using 2.2 k
Ω
pullup resistors to +5 VDC.
Figure 12 shows the typical encoder wiring pin assignment for single-ended signal input.
Note
The dotted loop indicates a shielded cable. A line above a signal indicates that the signal is
active low.
Figure 12.
Typical Single-Ended Encoder Wiring Pin Assignment
Figure 13 shows the typical encoder wiring pin assignment for differential line driver signal inputs.
Figure 13.
Typical Differential Line Driver Encoder Wiring Pin Assignment
If the encoder cable length is greater than 10 ft, use encoders with line driver outputs for your
applications. Power for a +5 V encoder—generated by a power supply inside the MID-7654/7652—is
available on pin 7.
1
2
3
4
5
6
7
8
Encoder A
Encoder B
Encoder Index
+5 V
Digital Ground
1
2
3
4
5
6
7
8
Encoder A
Encoder A
Encoder B
Encoder B
Encoder Index
Encoder Index
+5 V
Digital Ground