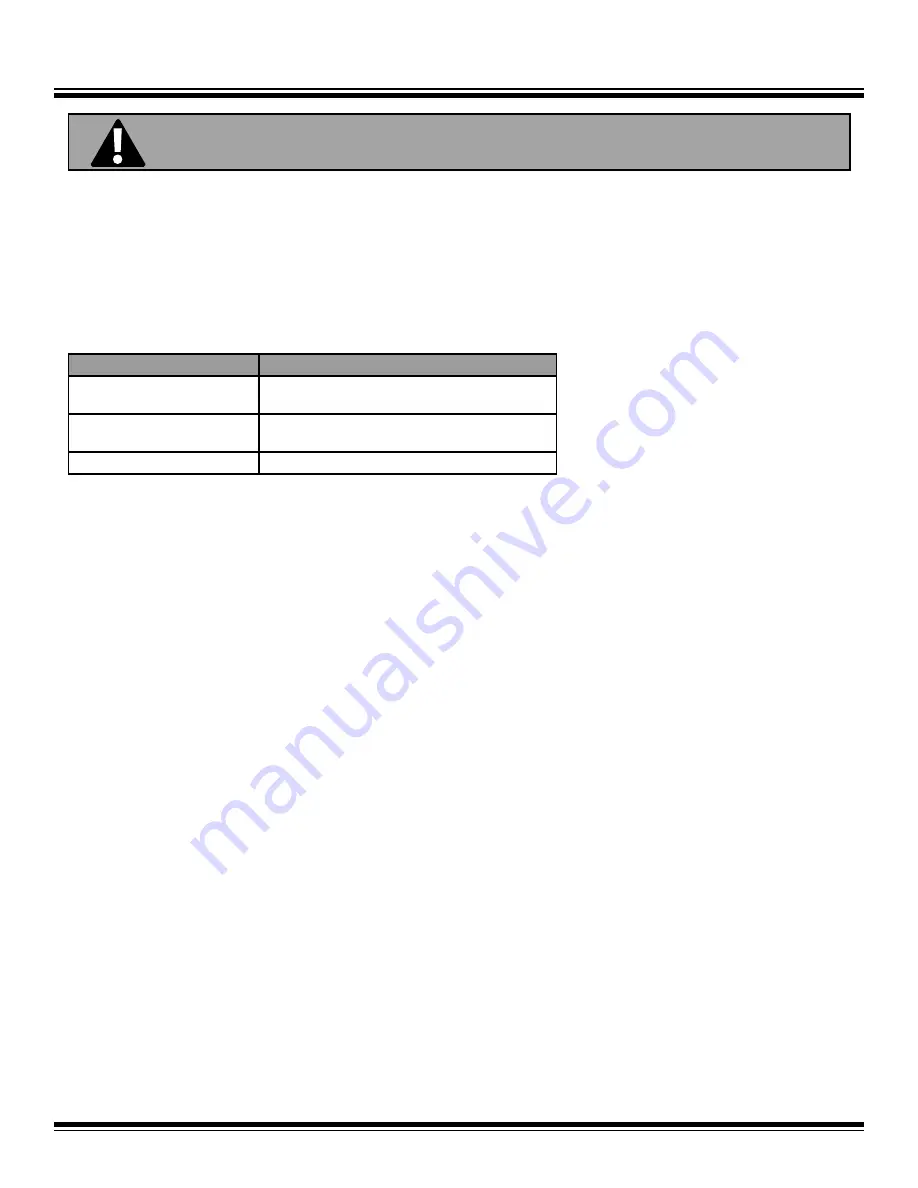
Maintenance
9
WARNING:
PRIOR TO ANY MAINTENANCE OR REPAIR WORK, THE MACHINE MUST BE TURNED OFF AND UNPLUGGED
FROM THE POWER SOURCE.
MAINTENANCE SCHEDULE
Regular maintenance is essential to a safe and long machine life.
The following table will show recommendations about time, inspection, and maintenance for the normal use of the machine. The time indica-
tions are based on uninterrupted operation. When the indicated number of working hours is not achieved during the corresponding period, the
period can be extended; however, a full overhaul must be carried out yearly.
Due to different working conditions, it is impossible to predict how frequently inspections for wear checks, maintenance, and repairs should be
carried out. Prepare a suitable inspection schedule based on the working conditions of the machine.
Operating Hours / Time Period
Inspection Points / Maintenance Instructions
12 hours after repair
Check functionality of all safety devices; check all acces-
sible screw connections for tightness.
Every 3 hours
Check whether there is any foreign matter in the hopper,
feed spout, or blast wheel unit.
Yearly
Complete full overhaul and cleaning of the machine.
BLAST PATTERN AND CONTROL CAGE ADJUSTMENTS
Correct adjustment of the control cage and blast pattern is the most important factor for optimum working conditions. Incorrect adjustment of the
blast pattern can result in uneven cleaning (shadows on the left or right side) and/or extremely high wear on the wheel kit and liners.
Factors That Affect the Blast Pattern
• Worn tune-up kit.
With increased wear of the wheel kit (impeller, control cage), the blast pattern will change.
• Size of the abrasive.
Every change of abrasive requires the blast pattern to be set or to be re-adjusted.
• Position of the control cage.
The control cage has a lateral window; the position of this window determines where the abrasive is fed on
the blast wheel, and where it hits the surface to be treated. After changing the wheel kit or before blasting on another type of surface, the
control cage must be checked and re-adjusted.
Adjusting the Control Cage
The position of the control cage is determined by the control cage fixing plate. The position can be changed in both directions up to 12.5
o
. Never
adjust the control cage or slacken the cage clamps during operation.
1.
Loosen the two screws and re-adjust the control cage fixing plate.
2.
Re-tighten the screws.
3.
Place the machine on a 1/4” (5-8 mm) thick steel plate and blast for 45 seconds at full abrasive load without moving the machine.
4.
Inspect the steel plate; there will be a “hot zone” on the blasted surface, where the machine developed the highest blast intensity. It will
normally be lighter and warmer than the rest of the blast cleaned area. Adjust the control cage until the hot zone is exactly in the middle
of the blast pattern.
5.
The blast procedure can now be started.
If the blast result shows strong blasting on the right side and weak blasting on the left (shadows), turn the upper edge of the control cage 1/8”
(2-4 mm) clockwise. If the blast result shows strong blasting on the left side and weak blasting on the right (shadows), turn the upper edge of
the control cage 1/8” (2-4 mm) counterclockwise.
Содержание HB5
Страница 1: ...Read Manual Before Servicing Machine 402970 Rev C HB5 HANDHELD SHOT BLASTER SERVICE MANUAL ...
Страница 2: ......
Страница 11: ...Parts List and Diagrams 11 OVERVIEW ...
Страница 12: ...Parts List and Diagrams 12 WHEEL DRIVE ASSEMBLY ...
Страница 13: ...Parts List and Diagrams 13 HOUSING ASSEMBLY ...
Страница 14: ...Parts List and Diagrams 14 VALVE ACTUATOR ASSEMBLY ...
Страница 15: ...Parts List and Diagrams 15 BASE SEAL ASSEMBLY ...
Страница 17: ......