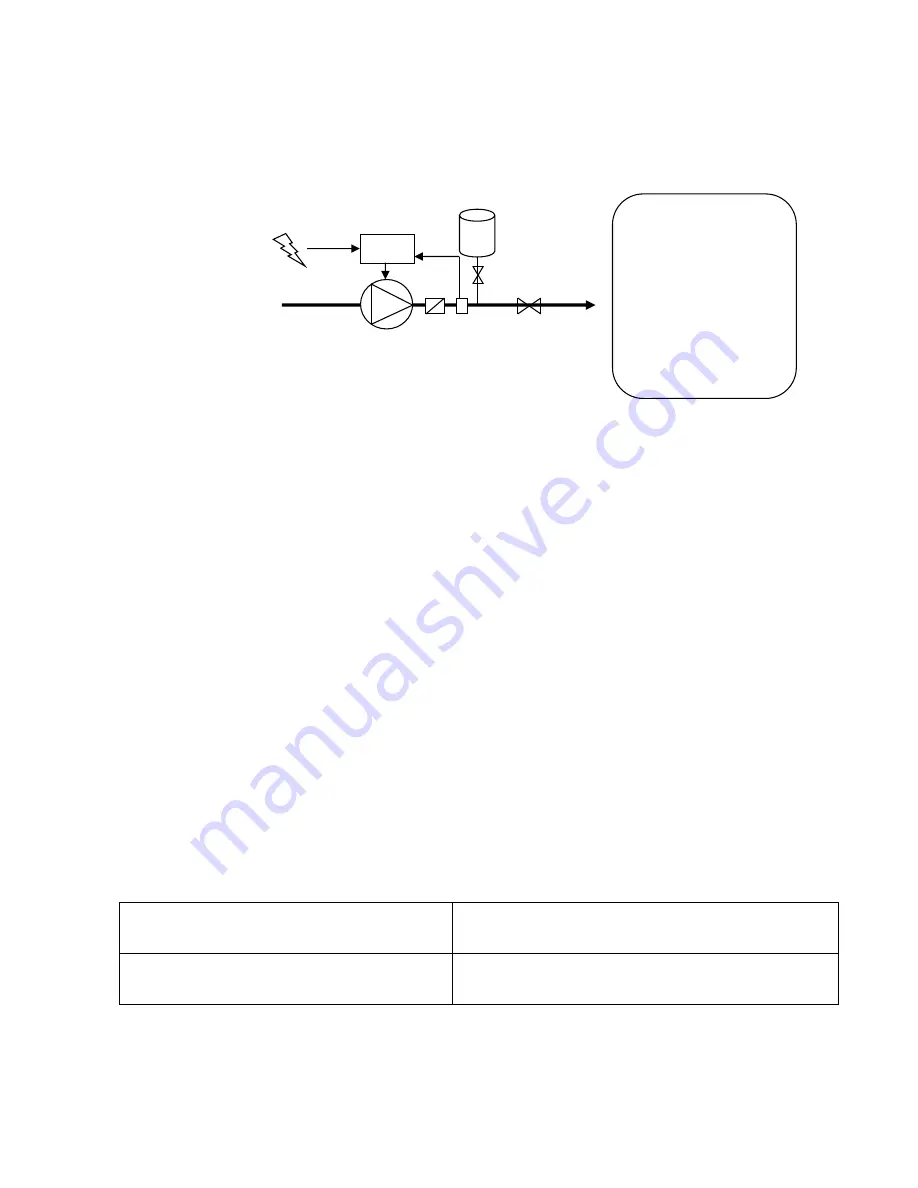
7
4.2 MIDA Installation for constant pressure control
MIDA controls the pump speed to maintain constant pressure at a set point independent of the water demand in the system.
A basic schematic is shown below:
4.2.1 Pressure tank
Installation of a pressure tank in the hydraulic system is recommended to compensate leakage of water in the system (or
during minimum water demand) and to avoid continuous start/stop cycling of the pump (check the appendix for more
information). Selecting the proper volume and pre-charge pressure of the tank is very important; smaller tank volumes will
not compensate adequately for minimum water usage or leakage, while larger volumes make it more difficult for MIDA to
control the pressure evenly.
Recommended tank volume is equal to the 10% of the maximum water flow of the system (expressed in volume unit/min)
Example:
if the max water flow is 50 liters/min, the pressure tank should have a capacity of 5 liters
If the max water flow is 20 gpm, the pressure tank should have a capacity of 2 gallons
Pre-charge pressure of the pressure tank should be at least 80% than the set-pressure of the system.
Example:
if the set-pressure of the system is 4 bar, the pre-charge pressure of the tank should be 3.2 bar
If the set-pressure of the system is 60 psi, the pre-charge pressure of the tank should be 48 psi
4.2.2 Pressure sensor
MIDA requires a pressure sensor with a linear output signal within the range 4 – 20 mA. The pressure transducer can be
powered by any range of DC Voltage which includes the value 15 V dc.
MIDA accepts the signal of a second pressure sensor in order to:
realize constant differential pressure (AN1 – AN2).
substitute first pressure sensor when it fails
SENSOR 1
AN1: 4-20 mA (-) signal
+15V: 15 Vdc (+) power supply
SENSOR 2
AN2: 4-20 mA (-) signal
+15V: 15 Vdc (+)
power supply
MIDA
1
2
3
5
4
1: pump
2: check valve
3: pressure tank
4: valve
5: valve
6: pressure sensor
6