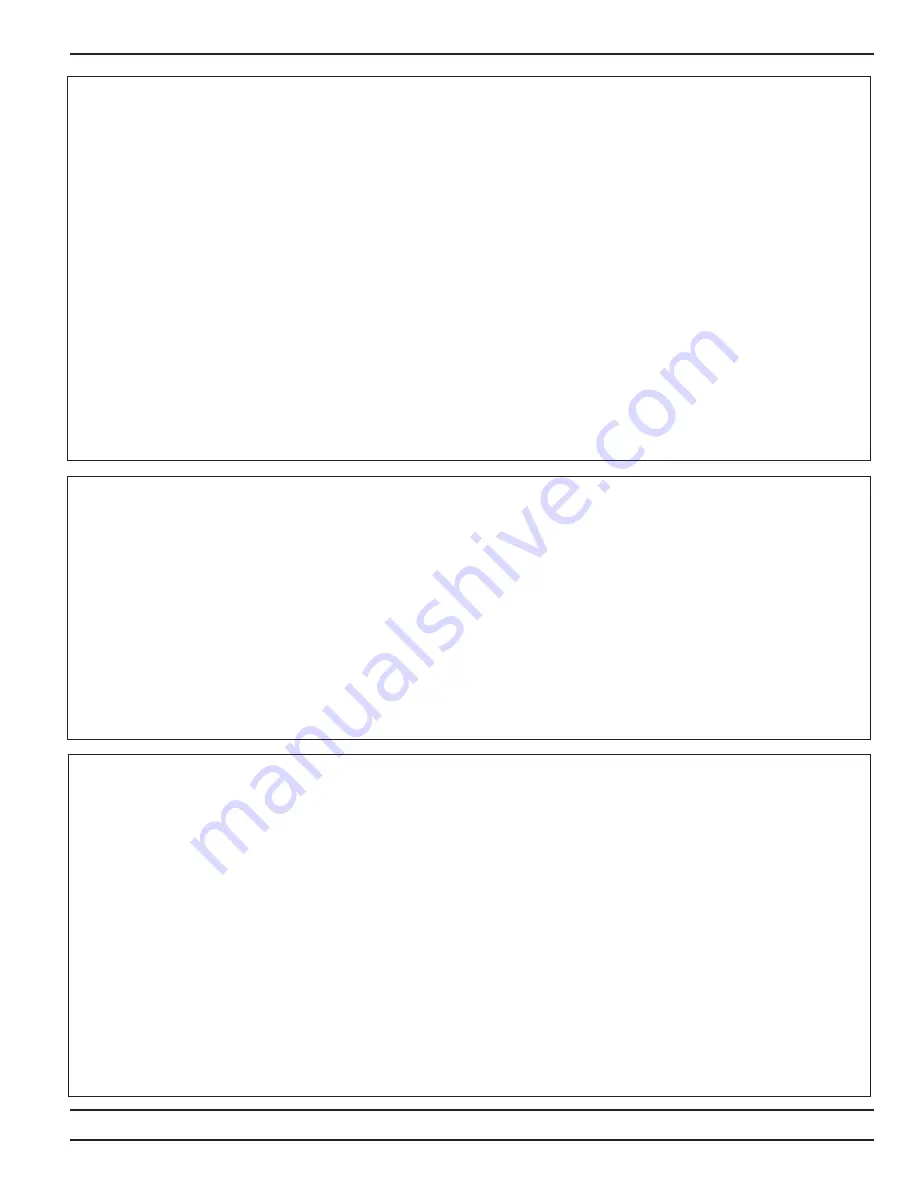
Page 5 of 24
9/18 IOM-FFDINST
Nailor Industries Inc. reserves the right to change any information concerning product or specification without notice or obligation.
INSTALLATION
The Fan Filter Diffuser is fully assembled from the factory with the exception of the HEPA filter and lamps (if applicable) which
are shipped separately.
Step 1
Carefully remove the unit from the shipping carton and inspect for damage that may have occurred during
shipping. If shipping damage is found, do not install. Call the manufacturer to report damage.
Step 2
Wipe down the unit to remove shipping dust and debris.
Step 3
Raise unit into ceiling and lower onto gasketed opening. Gasket should be a closed-cell material approved for the
environmental conditions. It is recommended to further support the unit from above using the tabs welded to the plenum.
Step 4
A qualified technician should wire the unit to the appropriate power supply per applicable codes and standards.
Refer to the wiring diagram (Figure 4) on page 23 of these instructions.
92FFD, 92FFD-SS – V18 120 VAC Supply
92FFD, 92FFD-SS – V19 208 VAC Supply
92FFD, 92FFD-SS – V20 240 VAC Supply
92FFD, 92FFD-SS – V21 277 VAC Supply
Step 5
Blow out/clean entire duct system leading to the unit to remove construction debris. This is especially important
for motor accessible units as they do not have a pre-filter. Wash pre-filter (if applicable), per “Cleaning the Fan
Filter Unit Pre-filter” below.
Step 6
Install the HEPA filter per the “Removal and Replacement of the HEPA Filter with Gel Seal” section on page 6.
CLEANING THE FAN FILTER DIFFUSER PRE-FILTER
WARNING! Disconnect the unit from the electrical power source before attempting to service the unit.
Note: For maximum performance, wash pre-filter every three to six months at minimum.
Step 1
Turn off the unit with the rocker switch located on the unit.
Step 2
Disconnect the unit at the power source or at the service panel.
Step 3
Using a driver, remove the screw holding the hinged door. This allows access to the pre-filter. Slide the pre-filter
out of the motor enclosure.
Step 4
Wash the filter with hot water and a mild detergent and rinse thoroughly. Do not use a caustic solution to clean the
filter. Blow dry or let air dry and slide the filter back into the motor enclosure.
Filter should be completely dry
before reinstalling into unit.
Step 5
Using a driver, re-secure the cover with the screw.
A NOTE ABOUT VAV BOXES AND DUCTED APPLICATIONS
In applications where the Fan Filter Diffuser unit will be installed downstream of variable airflow devices such as VAV boxes, air
valves, or variable air handlers, proper care in unit set-up needs to be taken.
The unit should not be programmed to run as constant airflow in this application.
Two variable controllers trying to reach
their respective set point will continuously adjust. This will cause issues such as surging, starving and eventual shut down of
the fan filter unit. The units should be ordered with a constant torque program. This will remove the dirty filter ramp-up feature
and the cfm display will no longer be accurate. However, this is still preferable to a PSC system due to the energy efficiency of
an EC versus a PSC motor.
Ducted applications While the fan filter unit can handle some positive or negative static pressure, optimal performance and
reliability will be achieved with an inlet static pressure of 0.0 w.c. or slightly negative.
To reach an accurate 0.0 w.c. inlet static, it is recommended that the primary air balancing of the duct system be done before
installing the fan filter unit. When the duct is at optimal static, install the unit per these instructions and adjust the airflow to the
design setting. Verify the airflow with an airflow hood.
It is recommended that all fan filter units in the system be energized before any upstream devices to prevent the FFD blower
wheel from spinning backwards. While the motor can generally overcome this, if the airflow needed to overcome high static is
too great, it may not. This will cause the motor to shut down. Continual running of the motor backward may result in reduced
reliability of the EC motor.