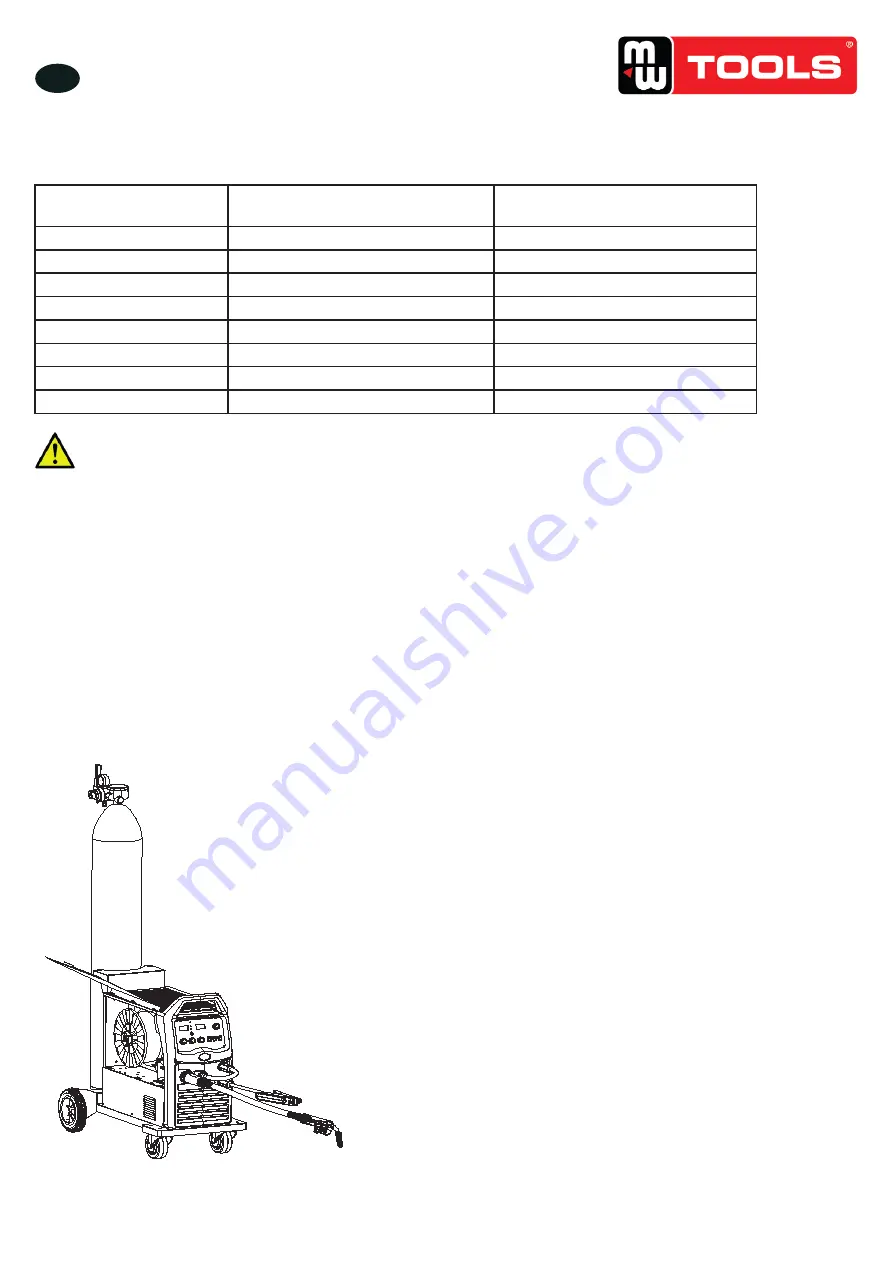
25
M1.3.MIG200I-MIG250I-MIG350I.NLFREN 09102018
EN
5.1.3 Welding parameters table (for reference only)
Electrode diameter
(mm)
Recommended welding current
(A)
Recommended welding voltage
(V)
1.0
20~60
20.8~22.4
1.6
44~84
21.76~23.36
2.0
60~100
22.4~24.0
2.5
80~120
23.2~24.8
3.2
108~148
23.32~24.92
4.0
140~180
24.6~27.2
5.0
180~220
27.2~28.8
6.0
220~260
28.8~30.4
Note: This table is suitable for mild steel welding. For other materials, consult related materials
and welding process for reference.
5.2 Gas shielded welding
5.2.1 Installation
1. Insert the welding torch into the Euro connector , and tighten it. After install the wire spool, manually thread the welding
wire into the torch body.
2. Connect the cylinder equipped with the gas regulator to the gas inlet on the back panel of the machine with a gas hose.
3. Insert the cable plug with earth clamp into the “-” output terminal, and tighten it clockwise.
4. Insert the front panel’s quick plug into “+” output terminal, and tighten it clockwise.
5. Install the wire spool on the spindle adapter, ensuring that the groove size in the feeding position on the drive roll matches
the contact tip size of the welding torch and the wire size being used. Release the pressure arm of the wire feeder to thread
the wire through the guide tube, and into the drive roll groove. Adjust the pressure arm, ensuring no sliding of the wire. Too
high pressure will lead to wire distortion, which will affect wire feeding. Press the manual wire feeding button to thread the
wire out of the torch contact tip.
Installation sketch map gas shielded welding
10
Note: This table is suitable for mild steel welding. For other materials, please consult related materials and
welding processing manual.
7.2 Gas Shielded Welding Installation and Operation
7.2.1 Installation
:
1) Insert the welding torch into the front panel’s “Euro connector for torch” output socket and tighten it. After
install the wire spool, pull through the welding wire into the torch body.
2) Connect the cylinder equipped with the gas regulator to the gas inlet on the back panel of the machine with a
gas hose.
3) Insert the cable plug with earth clamp into the front panel’s“-” output terminal and tighten it clockwise.
4) Insert the front panel’s quick plug into “+” output terminal and tighten it clockwise.
5) Install the wire spool on the spindle adapter, ensuring that the groove size in the feeding position on the drive
roll matches the contact tip size of the welding torch and the wire size being used. Release the pressure arm
of the wire feeder to thread the wire through the guide tube, and into the drive roll groove. Adjust the
pressure arm, ensuring no sliding of the wire. Too high pressure will lead to wire distortion, which will affect
wire feeding. Press the inching wire feeding button to thread the wire out of the torch contact tip.
Installation Sketch Map
:
Fig7 Gas Shielded Welding Sketch Map
7.2.2 Operation
:
1) After the correct installation per above methods, please turn on the power switch. While the power supply is
“ON”, welder starts to work normally with the indicator lighting up and fan working.Open the cylinder valve,
copyrighted
document
- all
rights
reserved
by
FBC