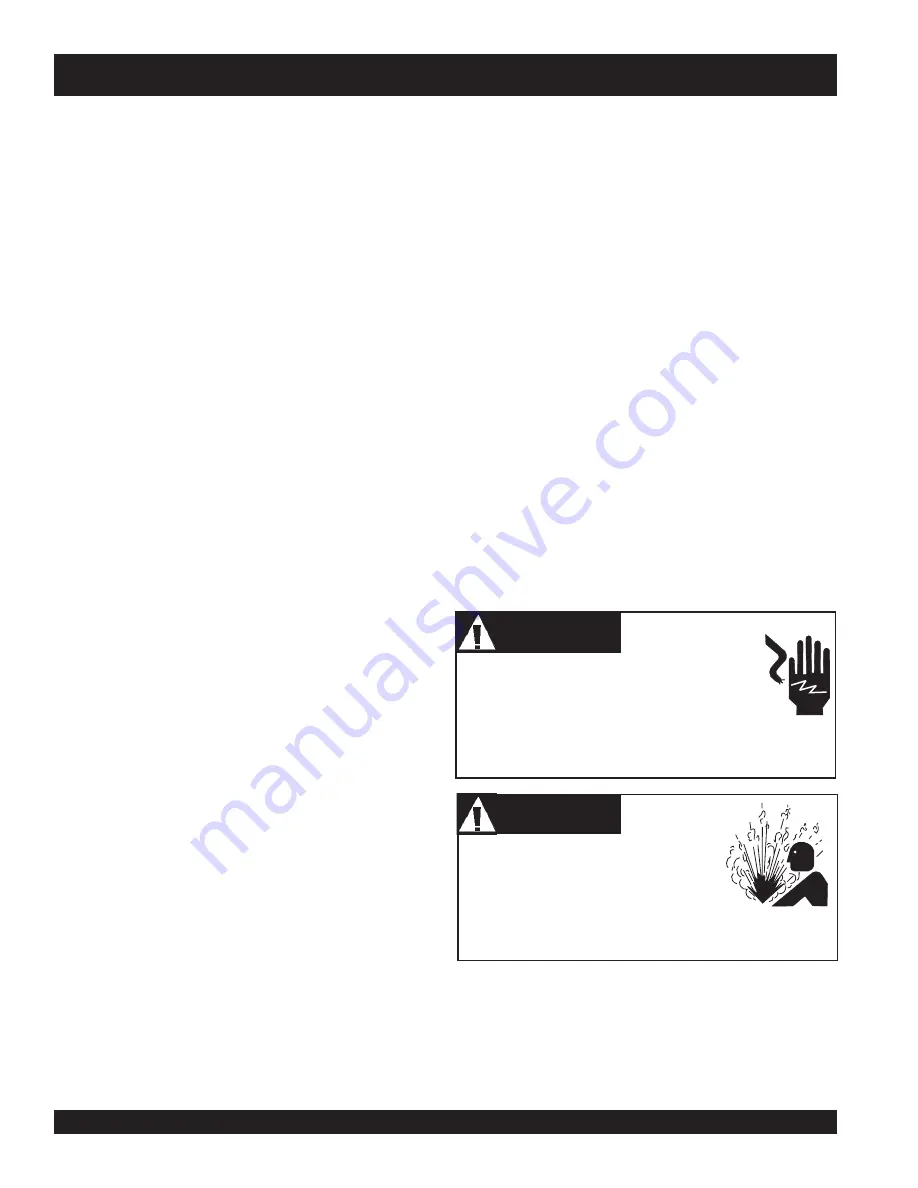
PAGE 10 — ST-2010 SERIES SUBMERSIBLE PUMPS — OPERATION & PARTS MANUAL — REV. #1 (12/15/05)
ST-2010 SERIES SUBMERSIBLE PUMPS
—
GENERAL INFORMATION
Introduction
The Multiquip Model ST-2010 submersible pump is designed to
pump water and is used for the draining (de-watering) of
swimming pools, well casings construction sites, cofferdams,
manholes, transformer vaults and excavations. The ST-
2010TCUL is designed for heavily debris-laden water and the
2-inch discharge port can handle solids up to one inch in
diameter.
A cast iron ductile type impeller is attached to the output shaft of
a 1 HP electric motor which provides adequate power for general
purpose pumping. This submersible pump is supplied complete
with an electric power cable, and a discharge port which accepts
a 2-inch hose.
This pump is ideal for portability because of its light weight and
carrying handle. For reliability and long life, a mechanical seal
provides shaft sealing, with an oil chamber separating the pump
section from the motor.
The pump when in use, should be installed as free standing
(upright position) on its strainer base. A 2-inch discharge hose
(not supplied) should be connected to the discharge port . The
discharge hose should be adequately supported to avoid stress
on the pump.
For maximum water flow, the discharge hose should be kept as
short as possible, and with minimum elevation above the pump.
Remember as the length and/or height of the discharge hose is
increased, the flow of water will be reduced. Also any reduction
in the hose size, and any fittings such as valves or outlet nozzles,
will restrict the water flow.
To avoid back-siphonage when the pump is switched off, ensure
that the end of the discharge hose is installed above the water
level at the final discharge point.
When the pump is switched off, the water remaining in the hose
will run back through the pump. This can be avoided by placing
a non-return valve in the hose nearest the pump.
NEVER
use this submersible pump to pump flammable liquids
or operate in a explosive or flammable environment.
Avoid using this pump in conditions where mud, grit, silt or other
debris are present. These conditions could cause blockage and
cause excessive pump wear.
DO NOT
install the pump directly into an area where there is a
heavy build-up of mud, grit, silt or debris. If this condition is present,
install the pump on a platform before operating.
This pump must always be positioned on a platform in an upright
position.
NEVER
operate the pump by a suspended rope. To
prevent large solids from entering the pump, install a wire mesh
screen or similar barrier around the pump.
If the pump was used to pump water containing mud, silt, use
clean water to flush out the pump after each use.
DO NOT
allow the pump to run dry, as this will damage the
pump. During maintenance, dry running is permissible but only
for a few seconds.
NEVER
lift the pump by its electrical power cord.
ALWAYS
lift
the pump by its carrying handle or attach a rope to the carrying
handle.
A pump fully submerged pump in liquid will not freeze, unless
the liquid freezes.
DO NOT
allow a partially submerged pump to
freeze. The expansion of water freezing in the volute may crack
the pump, causing expensive repairs. If there is any danger of
the pump being subjected to freezing temperatures, Lift the pump
from water and allow it to drain thoroughly.
If the pump jams or the pump rotor locks for any reason,
disconnect the pump from the power source immediately.
Allowing the pump motor to cycle
ON
and
OFF
under an overload
condition can burn out the motor.
When replacement of nuts and bolts is required, use only
recommended parts as referenced in the parts section of this
manual. This pump uses
metric
threads.
DO NOT
use English
measurement threads.
Control Box Installation Warnings
Failure to follow the above referenced precautions could result
in serious injury or death! Replace pump cord immediately if
cord becomes damaged or severed. This pump must be installed
in accordance with National Electric Code ANSI/NFPA 70 so as
to prevent moisture from entering or accumulating with the boxes,
conduit bodies fittings, float housing or cable.
When installing the control box, the possibility
exists of
electrical
shock
,
electrocution
and
possibly
death! NEVER
have untrained
personnel perform the installation.
ALWAYS
have
qualified service personnel (licensed electrician) perform the
installation.
Explosion
or
Fire Hazard
exists if this
pump is used with
flammable liquids
.
DO
NOT
use this pump with
flammable
liquids
.
DO NOT
install this pump in
hazardous locations as defined by the National Electrical
Code, ANSI/NFPA 70.
DANGER
DANGER
DANGER
DANGER
DANGER
WARNING
WARNING
WARNING
WARNING
WARNING
Discount-Equipment.com