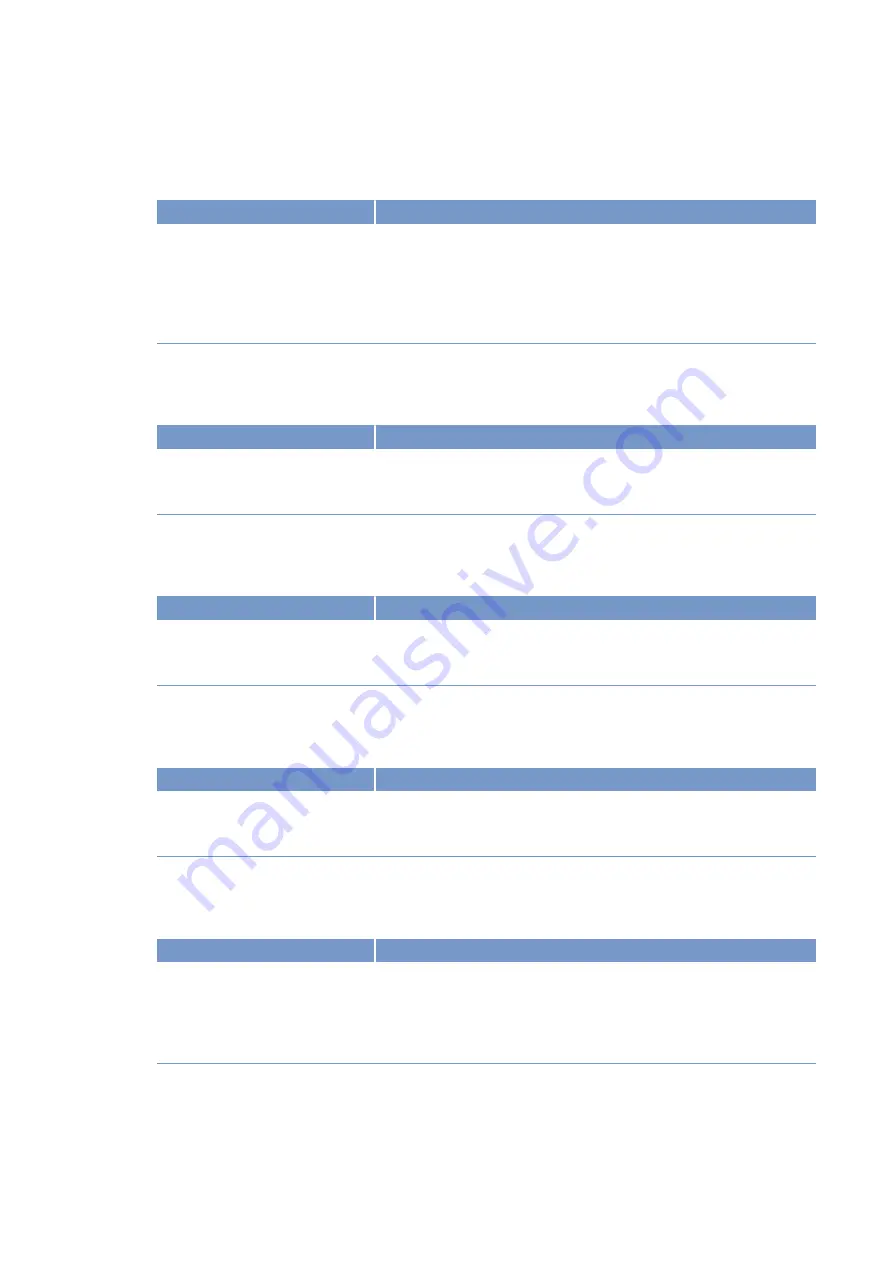
81 – AL Rail Leakage
PV-Number:
Cause
Corrective action
During engine start: The pressure
increase in the HP fuel system is
too low.
During engine stop: The pressure
drop in the HP fuel system is too
high.
1. Observe any other messages.
2. Check HP fuel system for leak-tightness.
3. Vent fuel system (→ Page 115).
4. Contact Service.
82 – HI P-Fuel (Common Rail)
PV-Number:
Cause
Corrective action
The HP fuel pressure at sensor
B48.1 has violated the upper limit
value. Fuel pressure is too high.
1. Observe any other messages.
2. Contact Service.
83 – LO P-Fuel (Common Rail)
PV-Number:
Cause
Corrective action
The HP fuel pressure at sensor
B48.1 went below the limit value.
Fuel pressure is too low.
1. Observe any other messages.
2. Contact Service.
89 – SS Engine Speed too low
PV-Number:
Cause
Corrective action
The engine speed has violated the
limit value. An emergency engine
shutdown has been initiated.
1. Acknowledge alarm.
2. Observe any other messages.
3. Contact Service.
102 – AL Fuel Cons. Counter Defect
PV-Number:
Cause
Corrective action
The fuel consumption calculated
by the ECU and stored on
stopping the engine cannot be
read out properly on restarting the
engine.
1. Observe any other messages.
2. Contact Service.
72 | Troubleshooting | M015650/06E 2018-05
TIM-ID: 0000082479 - 001