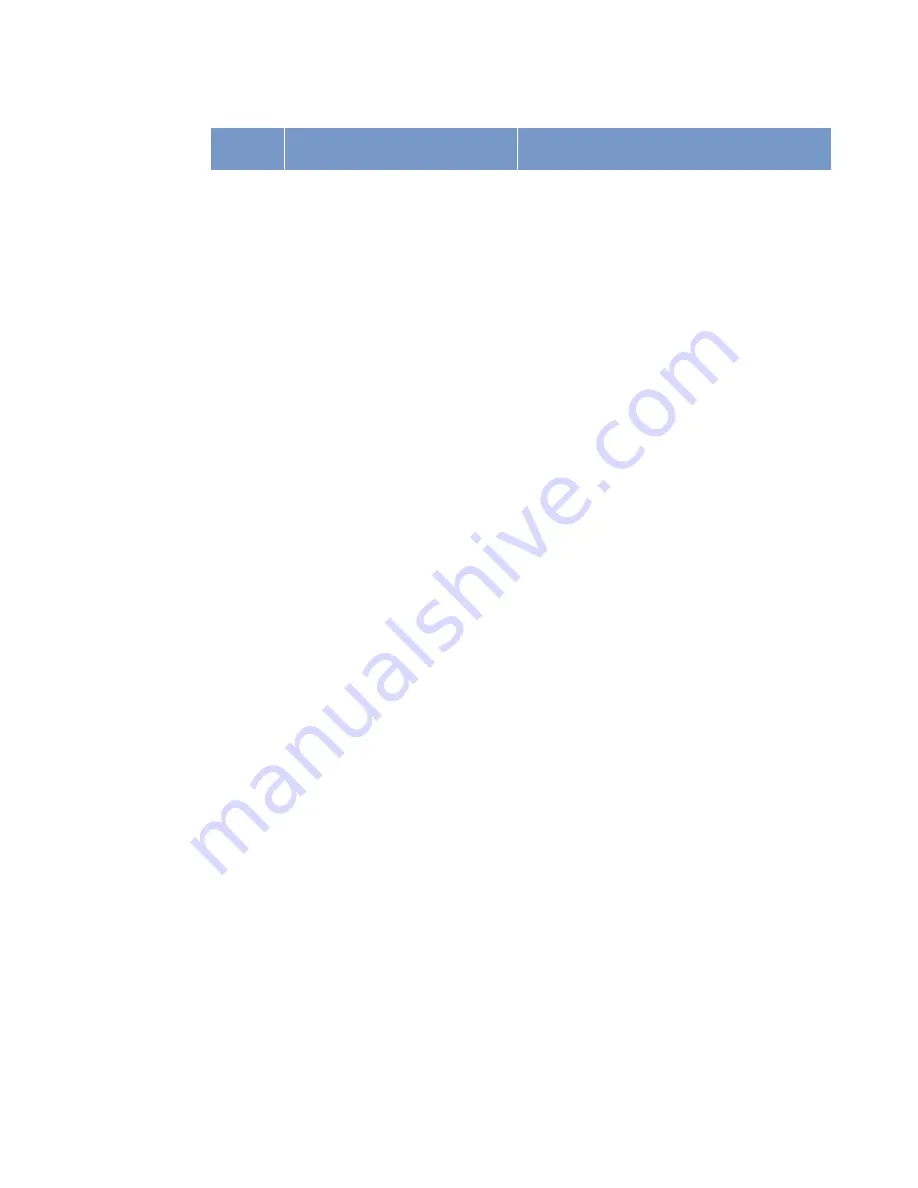
Abbrevia-
tion
Meaning
Explanation
MCS
Monitoring and Control System
MG
Message
MPU
Microprocessor Unit, Microprocessing
Unit
OT
Oberer Totpunkt
Top dead center (TDC)
PAN
Panel
Control panel
PCU/PMU Propeller Control Unit
Propeller controller
PIM
Peripheral Interface Module
PPC
Priming Pump Control
RCS
Remote Control System
RL
Redundancy Lost
Alarm: Redundant CAN bus failure
SAT
Sea Acceptance Test
SD
Sensor Defect
Alarm: Sensor failure
SDAF
Shut Down Air Flap(s)
Emergency air-shutoff flap(s)
SS
Safety System
Safety system alarm
SSK
Schnellschlussklappen
Emergency air-shutoff flap(s)
TD
Transmitter Deviation
Alarm: Sensor comparison fault
UT
Unterer Totpunkt
Bottom dead center (BDC)
MS150118/01E 2015-05
| Appendix A | 151
TIM-ID: 0000026477 - 004