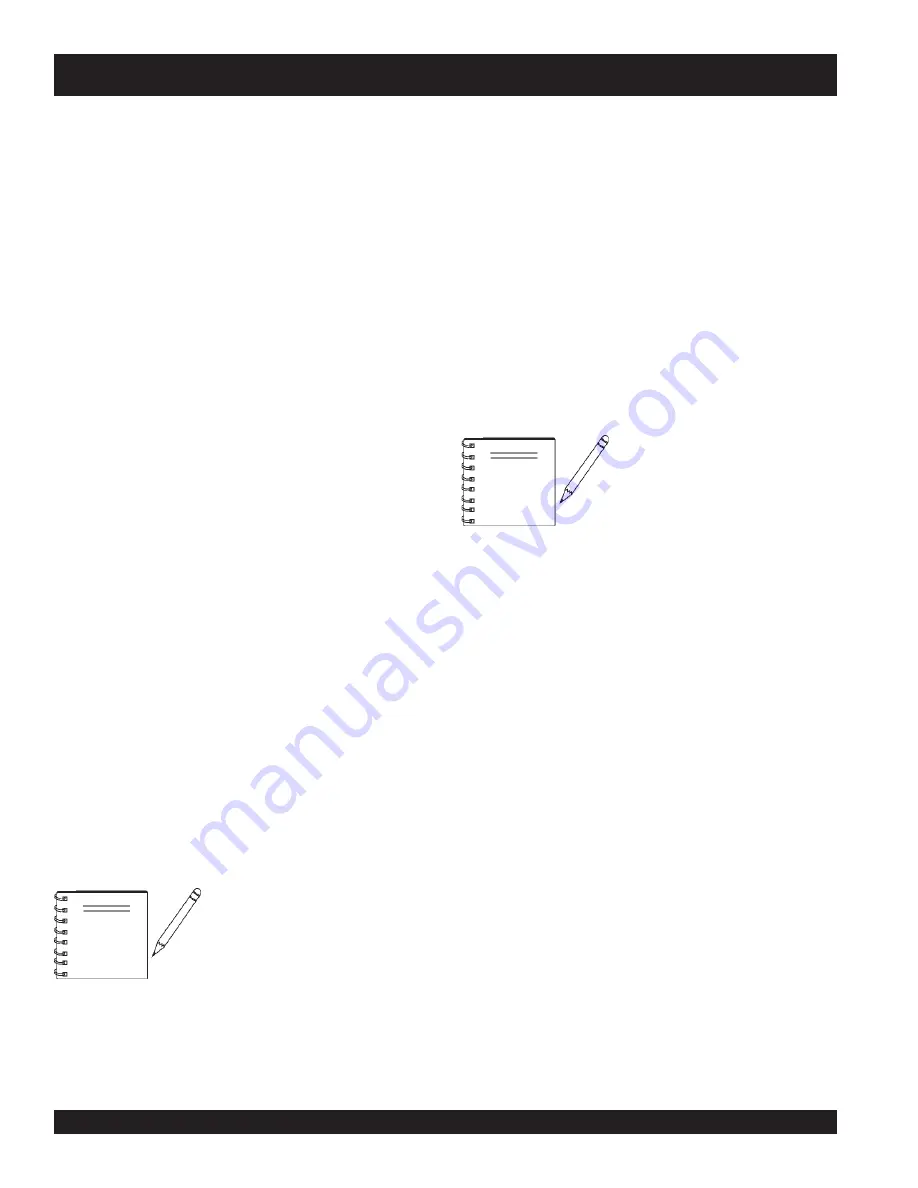
PAGE 20 — MAYCO C-30HDNI PUMP — OPERATION AND PARTS MANUAL — REV. #0 (05/15/03)
C-30HDNI PUMP — GENERAL INFORMATION
The following operating principles and operating suggestions
should prove helpful in the successful operation of your concrete
pump. Your new “small line” concrete pump has been designed
to give you many years of service when operated properly. A
study of the following paragraphs is important to the successful
operation of your new Direct-flow Concrete Placer.
All concrete pumps require a high level of operator skill and
more frequent service than most of the other construction
equipment. The highly abrasive nature of concrete under
pressure makes it extremely important that expendable wear
components be inspected at regular intervals between jobs
to prevent having to replace these items during a pour.
Experience has proved that inconsistency of batched concrete
mixes and frequent moving of the line requires the operator to
be readily available at all times during pumping to stop the
pump and prevent abuse to the unit which may occur if
unexpected blockages develop.
PUMP MIX GUIDELINES
When ordering concrete, be certain to advise the concrete
supplier that you require a “
pump mix”. The Direct-flow manifold
will pump a wide variety of materials, but certain basic principles
must be followed to assure successful pumping, as follows:
Generally speaking, the washed concrete sand and #4
aggregate (pea gravel) should conform to A.S.T.M. standards
in regard to sieve analysis. Sands in some areas are washed
clean of the #100 and #200 mesh fines, which results in
separation and jamming in the manifold while pumping under
pressure.
If this condition develops, check with your concrete suppliers
engineers and get their recommendations for supplementing
the lack of the fines. The use of locally accepted ad-mixes may
be required. (For example, Pozzolith, Bentonite Clay,
Plastiments, etc.) When properly prescribed, additives form the
plastic paste sometimes necessary to hold the cement and
aggregate together.
As a general rule, the use of approximately six sacks of cement,
70% washed concrete sand and 30% #4 pea gravel per yard of
concrete will result in a pumpable mix. The ideal nature of sand
and rock in certain areas may permit you to increase the
percentage of rock or adjust the mix considerably to meet the
job requirements. When possible, you may experiment with
various mixes in your area to determine the degree of versatility
of the Direct-flow Pump.
Uniform gradation of the washed concrete sand and the 1/2”
minus aggregate along with sufficient cement content and water
are important to a successful pump operation.
A recommended pumpable mix design would be 70% sand
and 30% aggregate-cement content to be a minimum of 6 sacks.
(564 lbs.)
SAMPLE DESIGN MIX-3000 PSI 3/8" SLUMP 4"- 5"
Type II Cement
6.49 sack/cu. yd
611 lbs.
Sand
Sat. Surf. Dry
2000 lbs.
#4 Gravel
Sat. Surf. Dry
864 lbs.
#3 Gravel
Sat. Surf. Dry
0 lbs.
Water
48 Gallons
400 lbs.
Total Weight
3,906 lbs
Admixture WRDA-79
26 oz.
Water 7.40 gal/sack
Test laboratory data has proven in many areas that the above
mix guidelines have produced concrete rated at 3000 psi (28
day test) and upwards of 5000 psi with an increase in cement.
In some areas where the gradation of sand and rock is ideal
and sufficient cement is used along with admixtures, the Mayco
small line concrete pump will handle up to a 50-50 ratio of sand
and rock.
When the mix is designed for wet gunning applications, it is
normal to increase the cement (up to 7.5 or 8 sacks) and change
the sand to rock ratio to 85% sand and 15% rock.
The Mayco concrete pump will valve efficiently when using
cellular-foam concrete mixes upwards of 70 lbs. per cubic foot
wet density. (Below 70 lbs. materials (roof decks) the valving
becomes inefficient.)
Your local sand and rock engineers
will give you the S.S.D. weights of
sand and rock required in your local
area which will yield one cubic yard
per the above recommendation.
If jamming conditions in the pump
or hose occur for any reason at all,
do not attempt to use more power to
correct the condition. Determine the
cause of jamming, correct it and
resume pumping. Trying to force
material through under jammed conditions may result in
damage to the drive system, thus voiding any warranty services.
NOTE
NOTE
Go to Discount-Equipment.com
to order your parts