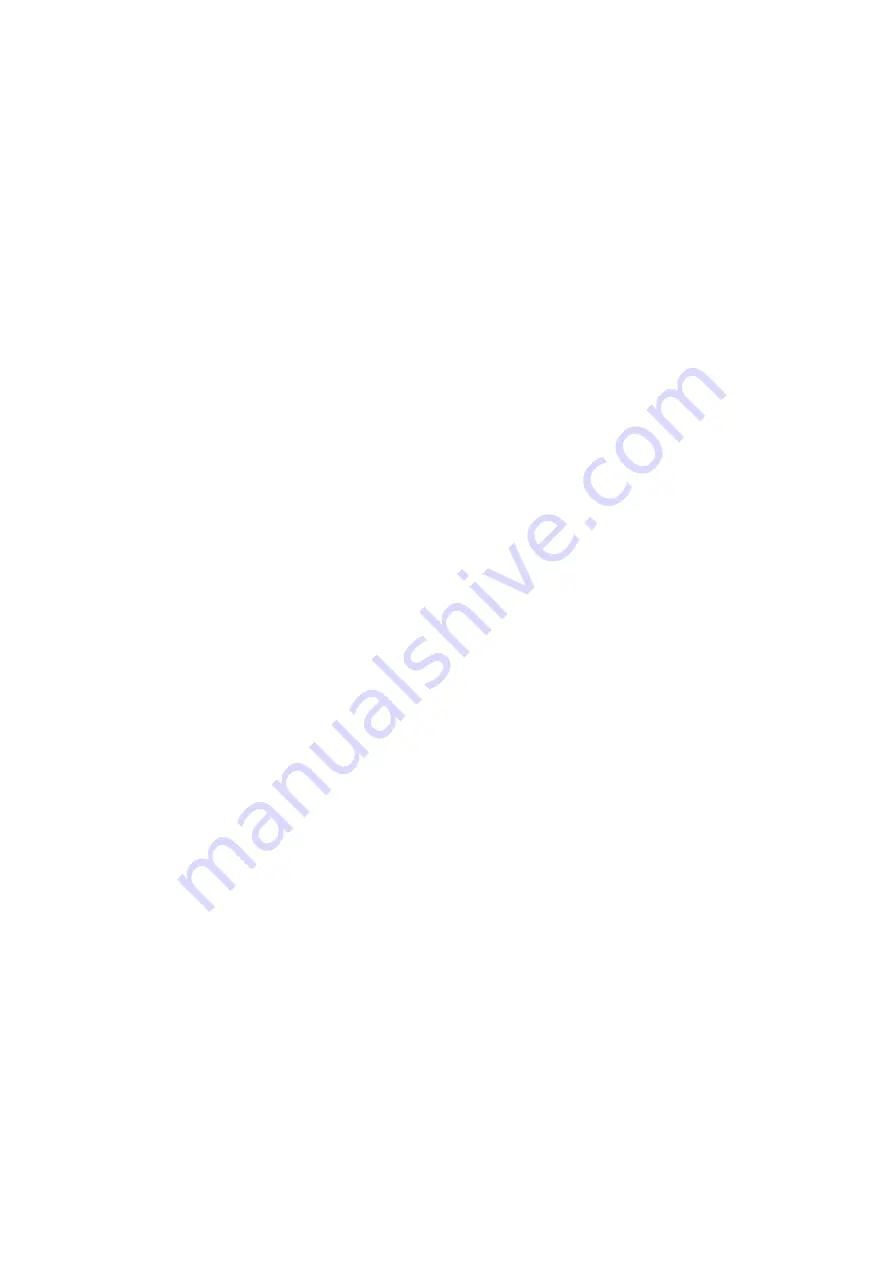
[2]
User Guidelines
– TCU-200
12-06-2019
Vers. 003
General information
This documentation is copyrighted. Unauthorized duplication is prohibited by law. To
the best of our knowledge and belief, the information contained in this documentation
is true and correct as of the date of publication. The contents, however, do not
constitute a binding obligation on the part of MOULDPRO APS and are subject to
change without notice.
© Copyright 2019 MOULDPRO APS
Содержание TCU-200
Страница 10: ... 10 User Guidelines TCU 200 12 06 2019 Vers 003 3 2 Rear view ...
Страница 19: ... 19 User Guidelines TCU 200 12 06 2019 Vers 003 7 Display and Parameter settings Zone A Zone B ...
Страница 38: ... 38 User Guidelines TCU 200 12 06 2019 Vers 003 17 Electrical diagram ...
Страница 39: ... 39 User Guidelines TCU 200 12 06 2019 Vers 003 18 Water Circuit Diagram ...
Страница 40: ... 40 User Guidelines TCU 200 12 06 2019 Vers 003 19 Control Circuit diagram ...
Страница 41: ... 41 User Guidelines TCU 200 12 06 2019 Vers 003 20 Components and spare part list ...