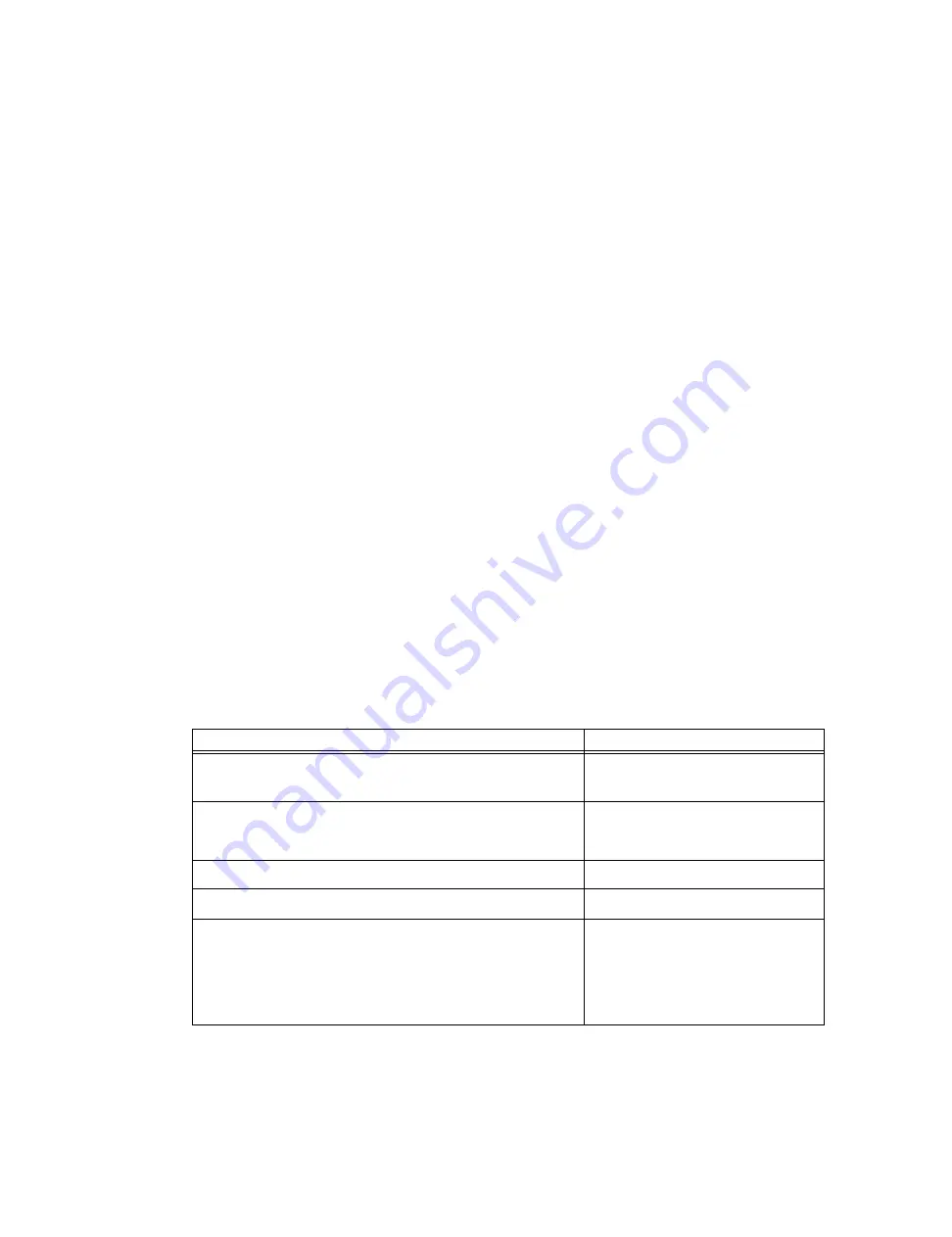
47
NOTE
Do not use a thick coating of compound; such could
degrade the thermal efficiency of the heatsink. Do
not allow dirt to contaminate the compound.
The voltage control pass device must be attached,
with ceramic insulator and using the clip hardware, prior
to securing the PC board mounting screws. This will
ensure proper thermal conduction. Both surfaces of the
insulator require thermal compound.
Tighten mounting screws on the power module and
30-watt final device before you attempt to transmit. This
will ensure proper thermal conduction.
Tighten the antenna connector nut (refer to Table
17 for torque value) to ensure that the connector is well
grounded. Failure to do so will cause improper opera-
tion in receive or transmit mode.
Do not bend or twist the PA board. Such stress
may crack the surface-mount components and hybrid
circuits.
D. Dash Control Head Board
When reassembling the control head, make sure
the microphone pins are properly inserted through the
elastomeric keypad. Also make sure the elastomeric
keypad inserts are secured to the PC board.
After reassembly, check every key or button to
ensure that each works properly (see the Control Head
Test).
E. Command Board
NOTE
This assumes PA is attached, control head is
detached, and control head interconnect board is dis-
connected.
1.
Before reassembly, apply a thin coat of thermal
compound (for example, Motorola part no.
11-83166A01) to the bottom of the audio PA
(U0450).
2.
Insert the command board into the PA accessory
connector (J503) before inserting it into the RF
board connector (P500). It may be necessary to
angle the command board towards the PA.
3.
Ensure the accurate placement of the insulator
between Q500, Q502, and Q521 and the chassis
wall.
4.
Start all six of the mounting screws before tighten-
ing any. Tighten evenly to ensure you do not warp
the board.
5.
Reconnect the control head interconnect board
(J103) to the control head connector (P103).
Observe pin alignment on P502 while connecting to
command board (J502). Secure the control head
with two screws. Reconnect the memory board (via
P505) and HearClear board prior to installing
covers.
TEST (Take Measurements at room temperature)
READING
12dB SINAD into antenna connector J9852F
–117.5dBm (maximum)
12dB SINAD into RX front end J9127
–119.0dBm (maximum)
12dB SINAD into RF board J350 (@ 109.65 MHz)
–118.5dBm (maximum)
VCO output TX injection J9641 (TX, TA mode)
+23dBm (maximum)
+19dBm (minimum)
VCO output RX injection J9642 (RX mode)
+5dBm (maximum),
+2dBm (minimum)
Synthesizer feedback P0602 (all modes)
+1dBm (maximum)
–12dBm (minimum)
Recovered audio level (for 1.5 kHz Deviation @ 1 kHz, J500-4)
125mV rms (maximum),
75mV rms (minimum)
Power Amp Output:
TX injection into PA J9641F
90 milliwatts
Power out (30W) at antenna connector (Note 1)
≥
34 watts
Power at RX Connector (Note 1)
≤
25 milliwatts
Power out (12W) at antenna connector (Note 1)
≥
14 watts
Power out (4W) at antenna connector (Note 1)
≥
5 watts
RX insertion loss (Note 2)
≤
1.5dB
Table 15. Minimum RF Performance Tests for Board Replacement
NOTES:
1.
Measure with K9.4, V drive, 9.6V applied at 12-pin dc connector PA board and 13.8V applied. External dc power connector and TX
injection provided.
2.
Measure with Pin, K9.4 and V drive set to zero, 9.6 and A+ voltages applied as in Note 1, above.
Содержание Spectra
Страница 6: ...v PERFORMANCE SPECIFICATIONS FOR SPECTRA PRIVACY PLUS TRUNKED CONVENTIONAL 900 MHz RADIO ...
Страница 7: ...vi PERFORMANCE SPECIFICATIONS FOR SPECTRA SMARTNET TRUNKED CONVENTIONAL 900 MHz RADIO ...
Страница 8: ...vii PERFORMANCE SPECIFICATIONS FOR SPECTRA 9000 RADIOS 900 MHz 30 WATTS ...
Страница 25: ...1 GENERAL INFORMATION 1 ...
Страница 73: ...53 INSERT GPW 7221 B Figure 22 Front Panel Diagnostics Key Closure Displays ...
Страница 75: ...INSERT GXW 4278 O PICKUP FROM PW 4320 O 55 CONTROL STATION WIRING DIAGRAM ...
Страница 79: ...PUSHBUTTON SPECTRA 900 MHz RADIO MECHANICAL EXPLODED VIEW 59 INSERT GXW 6225 B ...
Страница 96: ...82 MECHANICAL EXPLODED VIEW PARTS LIST FOR SPECTRA 900 MHz RADIO ...