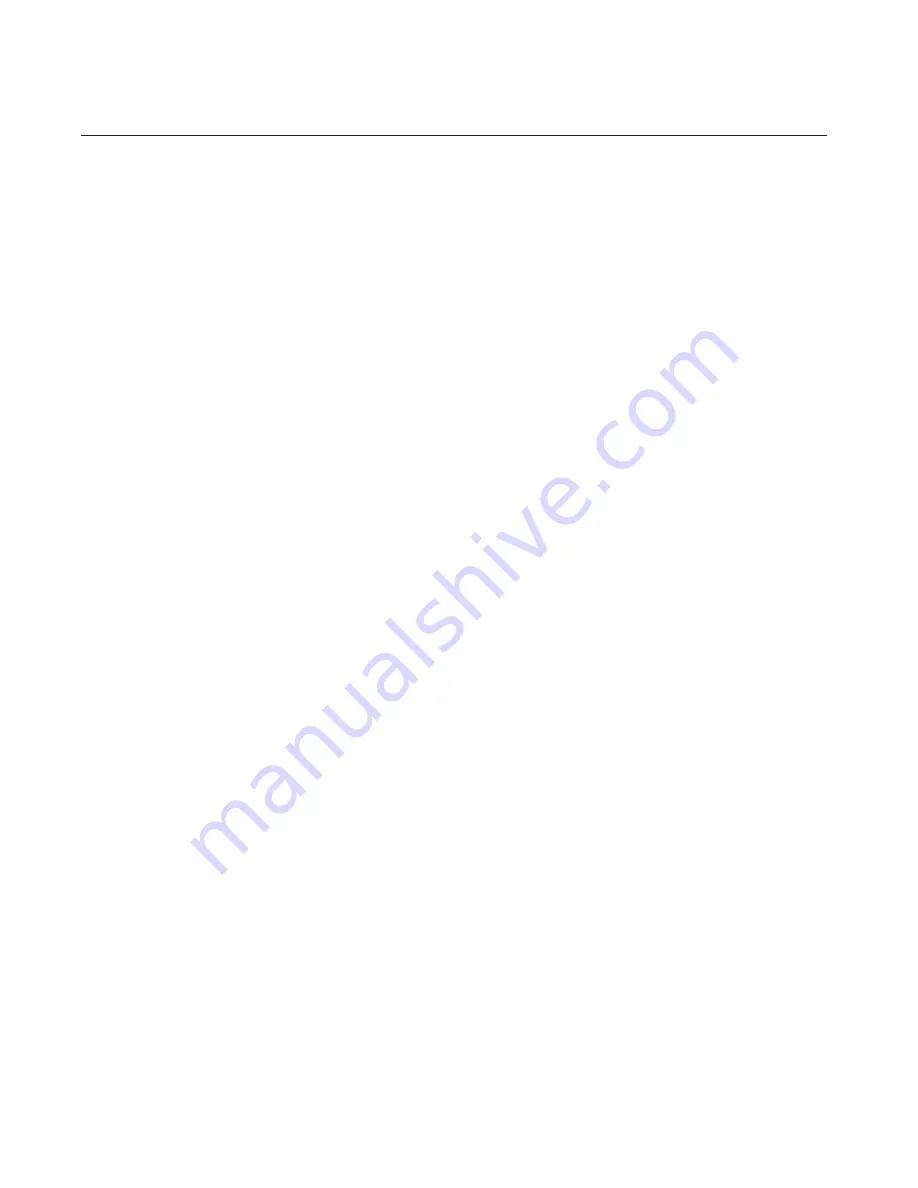
IPF
Page 12
Recommendations are:
•
Use flexible or semi-flexible, plastic, pneumatic
tubing and plastic fittings, if possible.
•
Provide clip- or bracket-type support at 30 cm
(1 ft) intervals, and provide independent support
for any components or equipment installed in the
lines. Use cushioning brackets to dampen
vibration, if possible.
•
Avoid “straight-line” connections.
•
Provide auxiliary support for the filter/regulator (if
equipped), especially in areas where shock and
vibration are prevalent.
•
Do not over-tighten the fittings. A torque of 10 to
15 N•m (7.4 to 11.1 ft/lbs) is adequate.
Filters
. The IPF requires filtered, dry, regulated,
instrument-quality air to prevent clogging, and to
ensure extended periods of maintenance-free
operation. Moore Industries suggests the following
levels of filtering protection:
•
Pre-filter – A general purpose “rough” filter, used
to reduce particulate matter to 5 microns in size.
Also removes bulk liquids. Although not re-
quired, this filter is especially recommended to
protect the 0.01 micron final filter when used.
•
Final Filter – A second, final filter is recom-
mended, to remove particulate matter in sizes
down to 0.01 micron. This filter removes virtually
all condensable liquids from the air stream as
well.
•
Filter/Regulator Module Option – A combined
filter/regulator assembly, the FR1 Option, offered
as an accessory for the IPF, removes particles
down to 0.01 micron, supplying regulated,
instrument-quality air to the unit. This space-
saving module is affixed to the IPF supply port,
and comes with a pressure gauge scaled in both
psi (0-60) and bars (0-4).
Operation
Once its calibration has been checked or adjusted,
and the unit has been installed properly, the IPF
operates unattended. It requires only a minor
periodic maintenance procedure, detailed in the next
section of this manual.
Remember that if an IPF is installed in an open loop,
it may appear to drift over extended periods of time,
due to the lack of corrective feedback.
If the unit is determined to be the cause of a loop
irregularity, carry out the maintenance procedure in
the next section of this manual. If problems persist,
refer to the Troubleshooting Section.
Instrument-quality Air.
Air from the application
continuously flows through the IPF during operation.
Depending upon the purity of the air supply, the
unit’s internal assembly may have to be removed
and cleaned at comparatively short intervals to
ensure continued optimum performance.
Initially, random checks can help establish a satisfac-
tory maintenance interval geared to the user’s air
supply cleanliness. Refer to the next section for
instruction on the disassembly and cleaning of the
IPF.
Maintenance
Before beginning IPF maintenance, the unit must be
removed from its application. It is strongly recom-
mended that the maintenance procedures be per-
formed in a clean, controlled environment, such as at
a technicians’ bench, in a laboratory, etc.. Several
internal parts are small and precision-machined;
easily lost or damaged if an attempt is made to
perform maintenance in the field.
After maintenance, each IPF should be recalibrated
before it is returned to service. Refer to the Calibra-
tion Section of this manual for instructions.