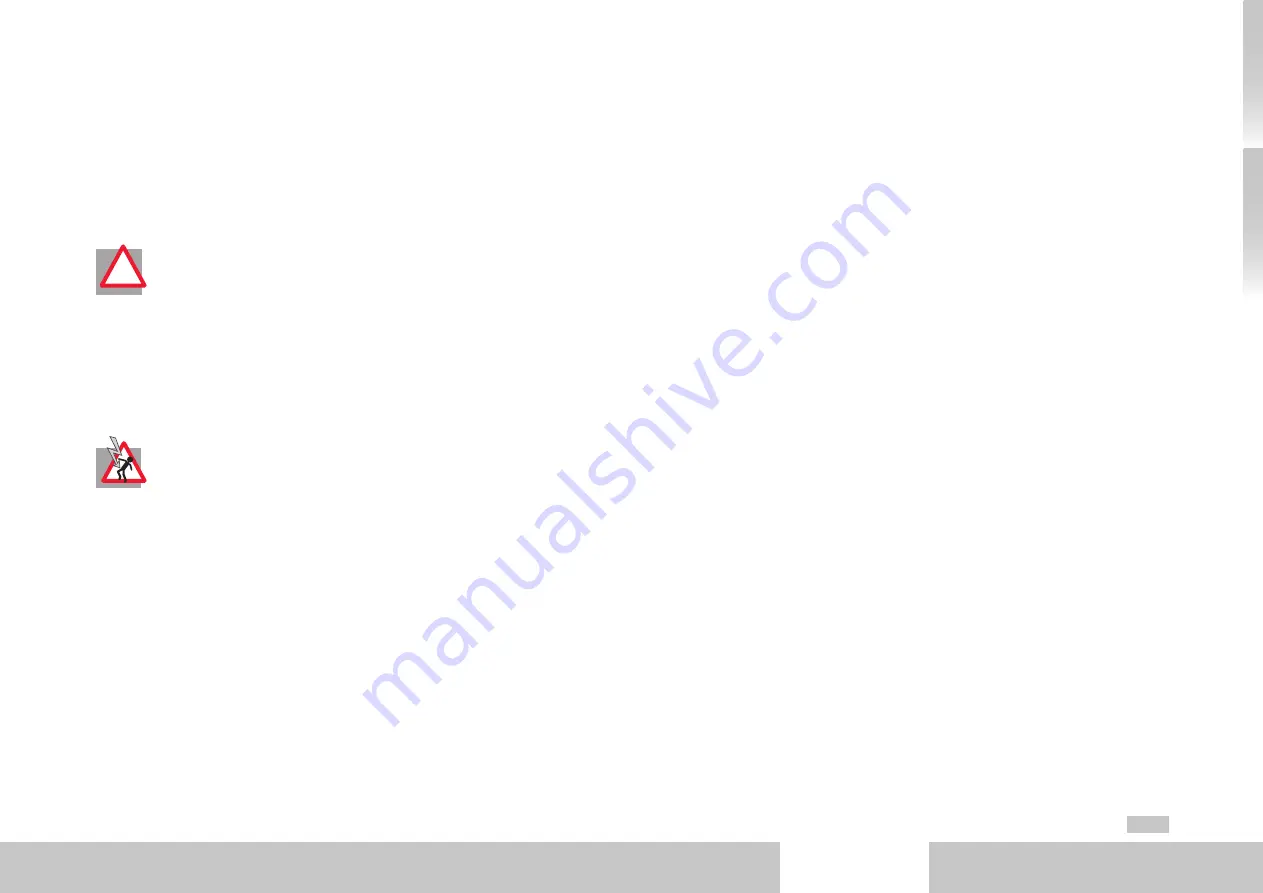
moog
MSD Servo Drive Compact Operation Manual
13
[
Installation
]
Id no.: CA97555-001, Rev. 3.0 - Date: 06/2012
3 Installation
3.1 Notes for installation
ATTENTION!
•
Qualified personnel
Installation must only be carried out by electrical engineering experts
who have been specially instructed in the necessary accident prevention
measures.
•
During installation work
Strictly avoid that ...
− screws, cable rests or foreign bodies drop into the device
− moisture enters into the device
DANGER CAUSED BY HIGH VOlTAGE!
•
Danger to life!
− Never wire or disconnect electrical connections while they are live.
Isolate the device from the mains supply (230/400/460/480 V AC) before
working on it. Even 10 minutes after switching off the mains supply
dangerously high voltages of ≥50 V may still be present (capacitor charge).
Work on the device must only be carried out, after the DC link voltage has
dropped below a residual voltage of 50 V (indicated by monitoring lED
H1
and
to be measured on terminals X1/l- and l+).
− Dangerous voltage may be applied to the device, even if the device does
not emit any visual or audible signals/indications (e.g. with mains voltage
applied to terminal X3) and missing control supply (+24 V on X2)!
The following general guidelines apply for the installation of servo drives:
•
Compliance with the EMC product standard
Commissioning (i.e. starting intended operation) is only permitted when strictly
complying with EMC product standard EN 61800-3. The installer/operator of a
!
machine and/or equipment must provide evidence of the compliance with the
protection targets stipulated in the EMC-standard.
•
Cabel type
Use only shielded mains, motor and signal lines with double copper braiding that is
overlapping by 60 to 70 %.
•
Routing of cables
− Route mains, motor and signal cables separated from one another. If possible,
keep a distance of at least 0.2 m, otherwise use separators. They should not
run in parallel. If crossovers are unavoidable, they should wherever possible be
configured perpendicular (at a 90° angle).
− Always route the motor cable without interruptions and the shortest way out of
the control cabinet. When using a motor contactor for example, the component
should be directly mounted to the drive and the shielding of the motor cable
should not be stripped off too soon.
− If possible enter signal lines only from one side into the control cabinet.
− lines of the same electric circuit must be twisted.
− Avoid unnecessary cable lengths and loops.
•
Grounding measures
Grounding measures of relevance for the drive are described in section 3.5
"Connection PE conductor".
•
Shielding measures
Do not strip the cable shields too soon, and lay them across wide areas both on
the component and on the backing plate or on the PE rail (main ground) of the
backing plate.
•
External components
− Place larger consumers near the supply.
− Contactors, relays, solenoid valves (switched inductivities) must be wired with
fuses. The wiring must be directly connected to the respective coil.
− Any switched inductance should be at least 0.2 m away from the process
controlled assemblies.
Additional information can be found in the corresponding connection description.
If you require further detailed information on installation you should consult the Moog
Helpline (see page 44).
Содержание G394-020
Страница 1: ...moog MSD Servo Drive Compact Operation Manual Servo drive 2 0 A to 8 A...
Страница 59: ......