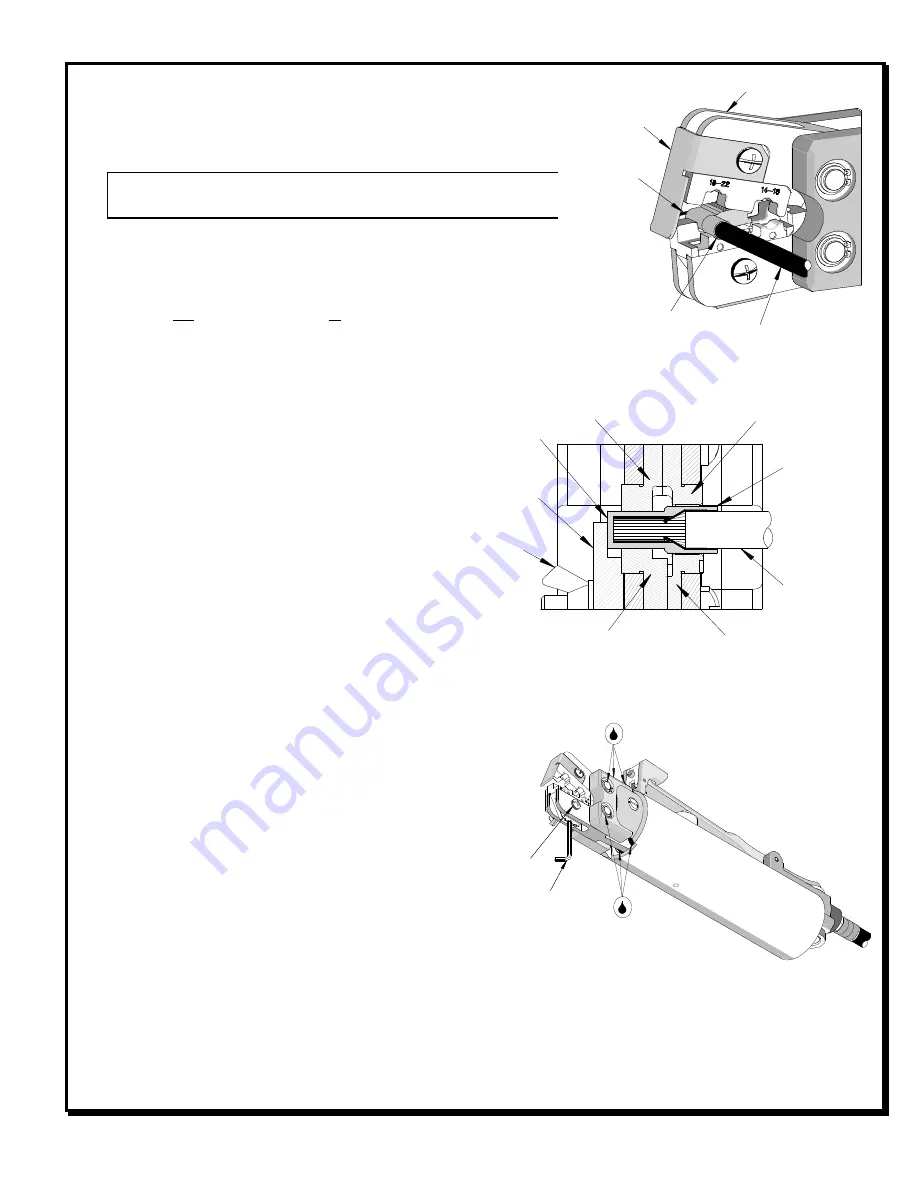
AT-AFIFG Air Crimp Tool Head
Doc. No: ATS-640054300
Release Date: 10-01-03
UNCONTROLLED COPY
Page 2 of 6
Revision: B
Revision Date: 05-05-04
BARREL OF
TERMINAL
SAFETY
SHIELD
WIRE
Figure 1
LOCATOR
JAWS OPEN
CONDUCTOR ANVIL
Figure 2
INSULATION ANVIL
WIRE
INSULATION
PUNCH
CONDUCTOR PUNCH
FLAT EDGE
OF TERMINAL
LOCATOR
M4 WING
NUT
TERMINAL
BARREL
OPERATION
Refer to the instruction manual for the 19279-0001 (AT-200) for
mounting this crimp tool head.
Caution:
Never operate this tool without the supplied safety shield
in place. Never place fingers in the tooling nests.
Crimping Terminals
1.
Insert the wire into the terminal. Insert the terminal with the
barrel into the color-coded nest and the square edge of the flag
facing out for 14-16 AWG and in for 18-22 AWG. Make sure the
back of the flag terminal is against the locator. See Figure 1. If
terminal is not flush against the locator loosen the M4 wing nut
and adjust the locator up or down so that the flat edge of the terminal is flush against the wall of the locator.
Tighten the M4 wing nut. See Figure 2.
2.
Partially close the tool to hold the terminal in
place.
3.
Push on wire to assure it is still fully seated
in the terminal. Cycle the tool.
4.
Remove the crimped terminal. Inspect for
proper crimp location, and check for
insulation closure. Locator is adjustable up
and down to keep terminals straight after
crimping.
5.
If the insulation part of the crimp needs to
be adjusted, first disconnect air source and
loosen the M4 screw on the bottom tool jaw,
then insert a 3/32” hex wrench (supplied)
into the bottom of the lower die. See Figure 3. A clockwise (CW) rotation decreases insulation crimp while
a counter-clockwise (CCW) rotation increases insulation crimp. After adjusting, retighten the M4 screw.
Reconnect air source.
Maintenance
It is recommended that each operator of the tool be
made aware of, and responsible for, the following
maintenance steps:
1.
Remove dust, moisture and other contaminants
with a clean brush, or soft, lint-free cloth.
2.
Do not use any abrasive materials that could
damage the tool.
3.
Make certain all pins; pivot points and bearing surfaces are protected with a thin coat of high quality
machine oil. Do not oil excessively. This tool was engineered for durability, but like any fine piece of
equipment, it needs cleaning and lubrication for a maximum service life of trouble-free crimping. Use a light
oil, such as 30 weight automotive oil at the oil points shown in Figure 3, every 5,000 crimps or monthly will
significantly enhance the tool life and ensure a stable calibration.
LUBRICATION POINTS
(BOTH SIDES) LIGHT OIL
(EVERY 3 MONTHS
OR 5,000 CRIMPS)
Figure 3
LOOSEN
M4 SCREW
3/32” HEX
WRENCH