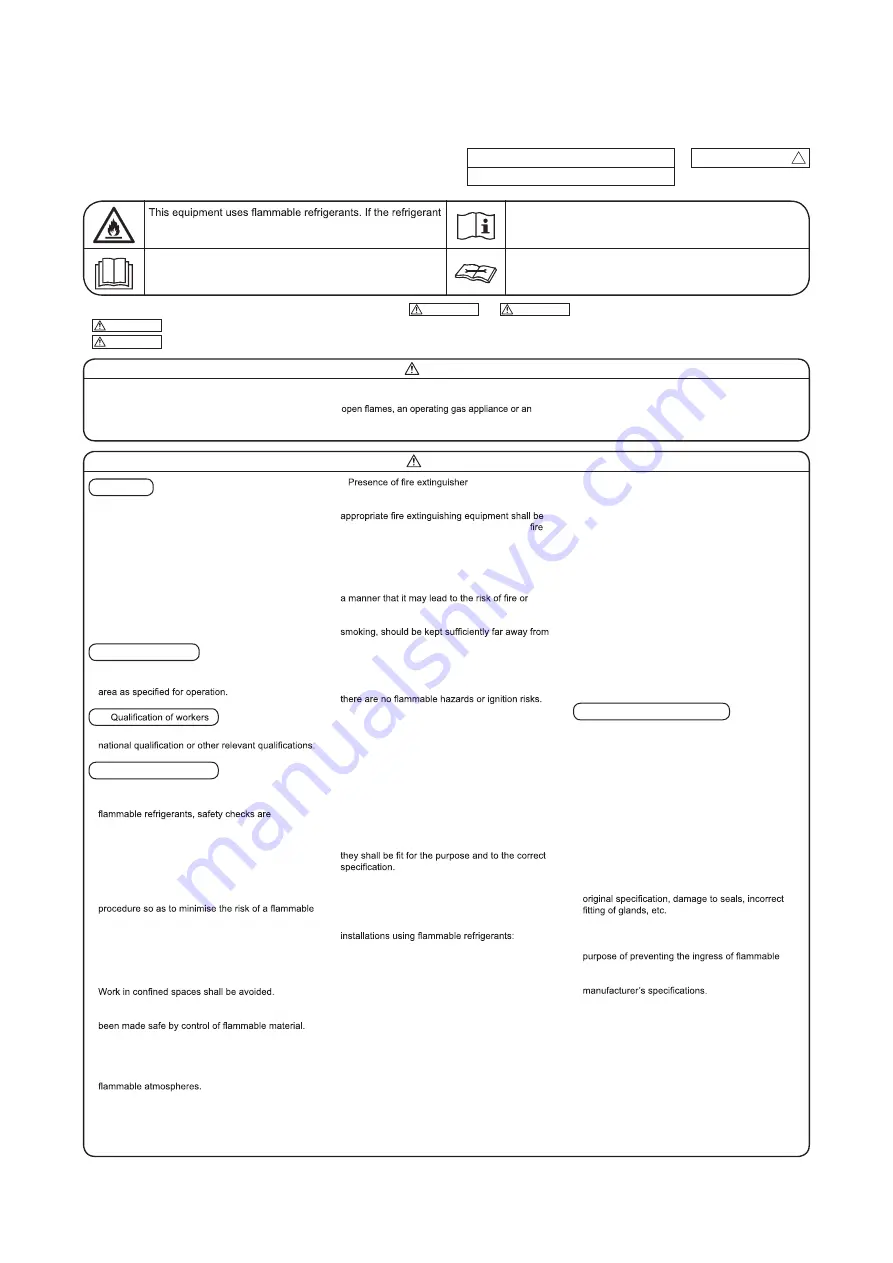
-
60
-
'18 • SRK-T-250
WARNING
WALL TYPE AIR-CONDITIONER
R32 REFRIGERANT USED
is leaked, together with an external ignition source, there is a
possibility of ignition.
There is information included in the user’s manual and/or
installation manual.
The user’s manual should be read carefully.
A service personnel should be handing this equipment with
reference to the installation manual.
• The precautionary items mentioned below are distinguished into two levels,
WARNING
and
CAUTION
.
WARNING
: Wrong installation would cause serious consequences such as injuries or death.
CAUTION
: Wrong installation might cause serious consequences depending on circumstances.
CAUTION
1. General
• That the installation of pipe-work shall be kept to a
minimum.
• That pipe-work shall be protected from physical
damage.
• That compliance with national gas regulations shall
be observed.
• That mechanical connections shall be accessible
for maintenance purposes.
• Keep any required ventilation openings clear of
obstruction.
• Servicing shall be performed only as recommended
by the manufacturer.
2. Unventilated areas
• The appliance shall be stored in a well-ventilated
area where the room size corresponds to the room
3.
• The staff in servicing operations must hold the
4. Information on servicing
4.1 Checks to the area
• Prior to beginning work on systems containing
necessary to ensure that the risk of ignition is
minimised.
• For repair to the refrigerating system, 4.3 to 4.7
shall be completed prior to conducting work on the
system.
4.2 Work procedure
• Work shall be undertaken under a controlled
gas or vapour being present while the work is being
performed.
4.3 General work area
• All maintenance staff and others working in the
local area shall be instructed on the nature of work
being carried out.
•
• The area around the workspace shall be sectioned off.
• Ensure that the conditions within the area have
4.4 Checking for presence of refrigerant
• The area shall be checked with an appropriate
refrigerant detector prior to and during work, to
ensure the technician is aware of potentially toxic or
• Ensure that the leak detection equipment being
used is suitable for use with all applicable
refrigerants, i.e.
non-sparking, adequately sealed or intrinsically
safe.
4.5
• If any hot work is to be conducted on the
refrigeration equipment or any associated parts,
available to hand. Have a dry powder or CO
2
extinguisher adjacent to the charging area.
4.6 No ignition sources
• No person carrying out work in relation to a
refrigeration system which involves exposing any
pipe work shall use any sources of ignition in such
explosion.
• All possible ignition sources, including cigarette
the site of installation, repairing, removing and
disposal, during which refrigerant can possibly be
released to the surrounding space.
• Prior to work taking place, the area around the
equipment is to be surveyed to make sure that
• “No Smoking” signs shall be displayed.
4.7 Ventilated area
• Ensure that the area is in the open or that it is
adequately ventilated before breaking into the
system or conducting any hot work.
• A degree of ventilation shall continue during the
period that the work is carried out.
• The ventilation should safely disperse any released
refrigerant and preferably expel it externally into the
atmosphere.
4.8 Checks to the refrigeration equipment
• Where electrical components are being changed,
• At all times the manufacturer’s maintenance and
service guidelines shall be followed.
• If in doubt consult the manufacturer’s technical
department for assistance.
• The following checks shall be applied to
– the charge size is in accordance with the room
size within which the refrigerant containing parts
are installed;
– the ventilation machinery and outlets are
operating adequately and are not obstructed;
– if an indirect refrigerating circuit is being used,
the secondary circuit shall be checked for the
presence of refrigerant;
– marking to the equipment continues to be visible
and legible. Markings and signs that are illegible
shall be corrected;
– refrigeration pipe or components are installed in
a position where they are unlikely to be exposed
to any substance which may corrode refrigerant
containing components, unless the components
are constructed of materials which are inherently
resistant to being corroded or are suitably
protected against being so corroded.
4.9 Checks to electrical devices
• Repair and maintenance to electrical components
shall include initial safety checks and component
inspection procedures.
• If a fault exists that could compromise safety, then
no electrical supply shall be connected to the circuit
until it is satisfactorily dealt with.
• If the fault cannot be corrected immediately but it
is necessary to continue operation, an adequate
temporary solution shall be used.
• This shall be reported to the owner of the
equipment so all parties are advised.
• Initial safety checks shall include:
– that capacitors are discharged: this shall be done
in a safe manner to avoid possibility of sparking;
– that no live electrical components and wiring are
exposed while charging, recovering or purging
the system;
– that there is continuity of earth bonding.
5. Repairs to sealed components
• During repairs to sealed components, all electrical
supplies shall be disconnected from the equipment
being worked upon prior to any removal of sealed
covers, etc.
• If it is absolutely necessary to have an electrical
supply to equipment during servicing, then a
permanently operating form of leak detection shall
be located at the most critical point to warn of a
potentially hazardous situation.
• Particular attention shall be paid to the following to
ensure that by working on electrical components,
the casing is not altered in such a way that the level
of protection is affected.
This shall include damage to cables, excessive
number of connections, terminals not made to
• Ensure that the apparatus is mounted securely.
• Ensure that seals or sealing materials have not
degraded to the point that they no longer serve the
atmospheres.
• Replacement parts shall be in accordance with the
NOTE
The use of silicon sealant can inhibit the effectiveness
of some types of leak detection equipment.
Intrinsically safe components do not have to be
isolated prior to working on them.
• Strict compliance of the domestic laws must be
observed when disposing the appliance.
• Do not use means to accelerate the defrost operation
process or to clean, other than those recommended
by the manufacturer.
• The appliance shall be stored in a room without
continuously operating ignition sources (for example:
operating electric heater.
• Do not pierce or burn.
• Be aware that refrigerants may not contain an
odour.
• The indoor unit shall be stored in a room that has a
minimum area of 4.0 m
2
.
RSA012A061A
C
(3) Safety precautions in handling air-conditioners with flammable refrigerants
Содержание SRK 25ZS-W
Страница 20: ...19 18 SRK T 250 3 Remote control Unit mm 60 24 167 a Wireless remote control...
Страница 50: ...49 18 SRK T 250...
Страница 51: ...50 18 SRK T 250...
Страница 52: ...51 18 SRK T 250...
Страница 53: ...52 18 SRK T 250...
Страница 54: ...53 18 SRK T 250...
Страница 55: ...54 18 SRK T 250...
Страница 56: ...55 18 SRK T 250...
Страница 57: ...56 18 SRK T 250 2 Installation of outdoor unit RWC012A068...
Страница 58: ...57 18 SRK T 250...
Страница 59: ...58 18 SRK T 250...
Страница 60: ...59 18 SRK T 250...