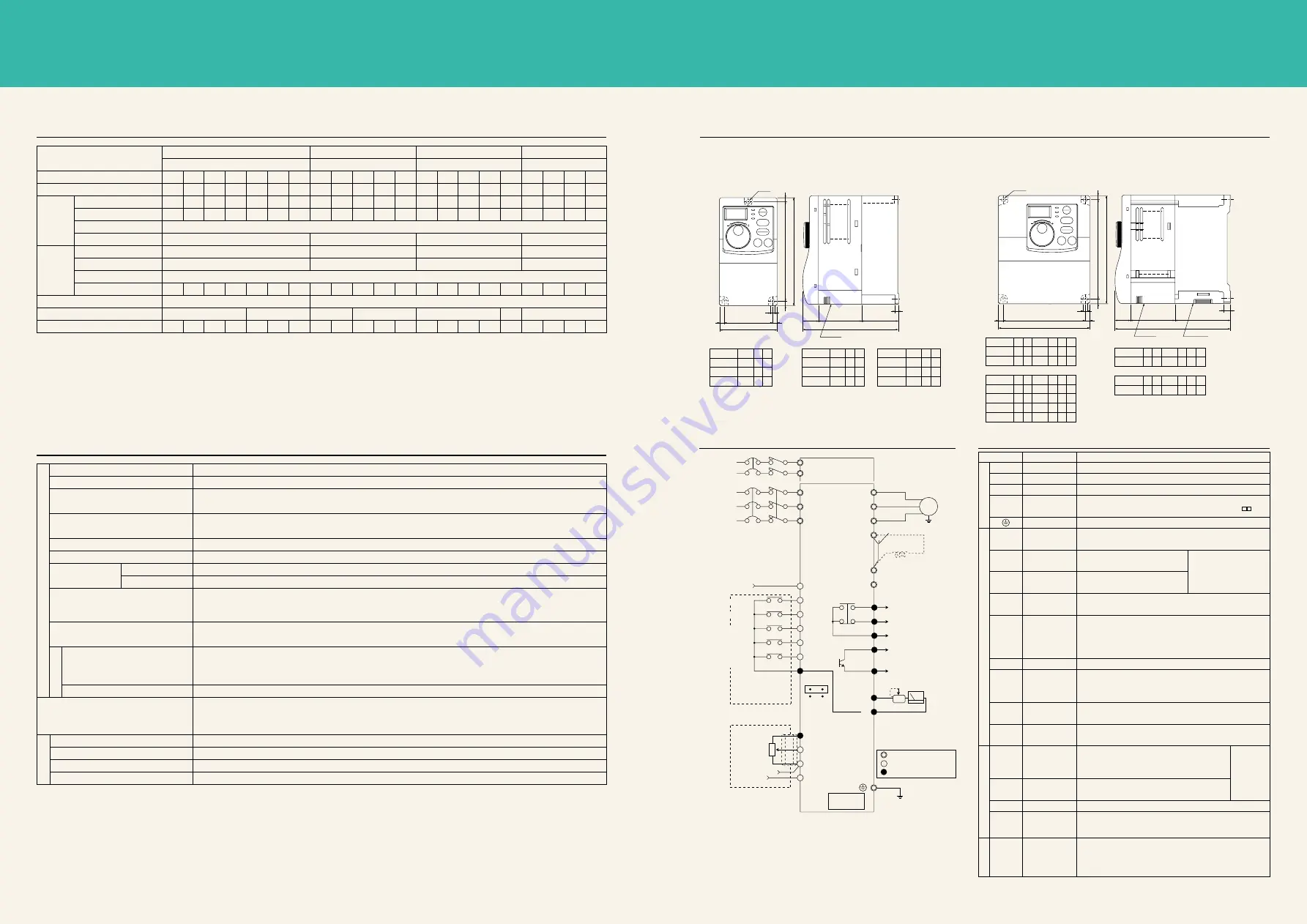
General Specifications
External Dimension Drawings
(Unit: mm)
Common Specifications
Terminal connection diagram
Explanation of Terminals
Control method
Output frequency range
Starting torque
Acceleration/deceleration time setting
Select from V/F control (Soft-PWM control/high carrier frequency PWM control selective) and automatic torque boost control
0.5 to 120Hz (starting frequency can be varied between 0 and 60Hz)
150% (at 6Hz) during automatic torque boost control
0,0.1 to 999 s (acceleration/deceleration can be set individually), linear or S-pattern acceleration/deceleration mode can be selected
0.1K, 0.2K,
150%, 0.4K, 0.75K,
100%, 1.5K,
50%, 2.2K 3.7K
20%
Operation frequency (0 to 120Hz), operation time (0 to 10 seconds), operation voltage (0 to 15%)
One type can be selected from output frequency or motor current. Pulse train output (1440 pulse/s 1mA full scale).
–10˚C to
+
50˚C(non freezing), (–10˚C to
+
40˚C for fully enclosed structure specifications), 90%RH or less(non condensing)
–10˚C to
+
65˚C
Indoors with no corrosive gases, flammable gases, oil mist or dust
1000m or less above sea level, 5.9m/s
2
or less (JIS C 0040 compliant)
1. The applicable motor indicates the maximum applicable capacity when using a Mitsubishi standard 4-pole motor.
2. The rated output capacity is 230V for the 3-phase 200V output voltage, and 440V for the 3-phase 400V output voltage.
3. The overload current rating percentage indicates the percentage in respect to the inverter's rated output current. When used repeatedly, it is necessary to wait for the inverter motor to return to a temperature
less than the temperature for the 100% load.
4. The maximum output voltage will not exceed the power supply voltage for the 3-phase 200V/400V power input specification product and the single-phase 200V power input specification product. The
single-phase 100V power input specification product cannot output more than twice the power voltage.
5. The power capacity will change according to the power side impedance (including the input reactor or wire) values.
6. For the single-phase 100V power input specification product, when a load is applied on the motor, the output voltage will drop by approx. 10 to 15%. However, when using a general-purpose motor, the
load must be reduced before use.
(Notes)
1. The indicated braking toque is the short-term average torque (which changes with motor loss) when the motor alone is decelerated from 60Hz. It is not the continuous regenerative torque. Deceleration
from frequencies exceeding the base frequency will have a lower average deceleration torque value.
2. If an undervotlage occurs, an error will not be output, but the output will be cutoff. Operation can be resumed after restoring the power, but depending on the operation state (size of load, etc.), the overcur-
rent protection or regenerative overvoltage protection may function when the power is restored.
3. This is the temperature to which units can be exposed for a short time, such as during transportation.
4. This corresponds only to the products with built-in cooling fan.
5. This applies only to the type with RS-485 function.
6. This functions only when the external thermal input (OH) is selected with Pr. 60 to Pr. 63 (input terminal function selection).
7. This functions only when Pr. 40 (start-time ground fault detection selection) is set to 1.
1.
This is not required when calibrating with the setting dial. Use this when calibrating
the frequency meter manually because the frequency meter is at a remote location etc.
Note that when the scale calibration resistor is connected, the needle on the frequency
meter may not adjust to the full scale. In this case, calibrate with the setting dial.
2.
If the setting unit is used frequently, use the 2W1
k
potentiometer.
3.
This is provided only with the type having the RS-485 function.
4.
This is a connection example for when the control circuit logic is sink (default setting).
5.
When using the current input for the frequency setting signal, set one of the parameters
between Pr. 60 and Pr. 63 (terminal function selection) to 4, and assign one of the ter-
minals RH, RM, RL or STR to AU (current input selection).
6. This cannot be mounted on the single-phase 100V power input specification product.
7. The single-phase 100V power input specification product does not have terminals.
8. The RL, RM, RH, RT, AU, STOP, MRS, OH, REX, JOG, RES, X14 and X16 signals
can be selected with the input terminal function selection (Pr. 60 to 63).
9. The RUN, SU, OL, FU, RY, Y12, Y13, FDN, FUP, RL, LF, and ABC signals can be
selected with the output terminal function selection (Pr. 64, 65).
(Notes)
Control specifications
Output signals
Environment
Frequency setting resolution
Frequency precision
Braking torque
Input signals
Operation functions
Operation functions
For meter
Protection and warning functions
Ambient temperature and humidity
Storage temperature (Note 3)
Atmosphere
Altitude and vibration
Regenerative (Note 1)
DC braking
5VDC input: 1/500 of maximum setting frequency, 10VDC, DC4 to 20mA input: 1/1000 of maximum setting frequency
Digital input: 0.1Hz (less than 100Hz), 1Hz (100Hz or more)
Analog input: Within
1% of maximum output frequency (25˚C
10˚C)
Digital input: Within
0.5% of set output frequency (when setting dial is used)
Upper/lower limit frequency setting, frequency jump operation, external thermal input selection, restart after instantaneous power failure,
forward/reverse run prevention, slip compensation, operation mode selection, PID control, computer link operation (RS-485) (Note 5)
Overcurrent cutoff (during acceleration, deceleration, and constant speed), regenerative overvoltage cutoff (during acceleration,
deceleration, and constant speed), overload cutoff (electronic thermal relay), fin overheating, fan trouble (Note 4), stall prevention,
output side ground fault protection at starting (Note 7), external thermal input (Note 6), PU dislocation (Note 5), No. of retries exceeded,
communication error (Note 5), CPU error, undervoltage (Note 2)
䊏
FR-S520-0.1K, 0.2K, 0.4K, 0.75K
䊏
FR-S520S-0.1K, 0.2K, 0.4K, 0.75K
䊏
FR-S510W-0.1K, 0.2K, 0.4K
䊏
FR-S520-1.5K, 2.2K, 3.7K
䊏
FR-S540-0.4K, 0.75 K, 1.5K, 2.2K, 3.7K
䊏
FR-S520S-1.5K
䊏
FR-S510W-0.75K
3-phase AC
power supply
NFB
MC
Inverter FREQROL-S
500
Inverter FREQROL-S
500
U
V
W
P1
R
S
T
Single-phase
AC power
supply
NFB
MC
R
S
External transistor common
Control input signal (Note 4)
STF
PC
STR (Note 8)
RH (Note 8)
RM (Note 8)
RL (Note 8)
SD
Frequency setting signal
(Note 2)
Frequency
potentiometer
1/2W1k
Current input(–)
DC4~20mA(+)
(1)
(2)
(3)
10(+5V)
2
(
)
0~5V
0~10V
5(Common)
4(4~20mA)
PU connector
(RS-485)
Grounding
SD
FM
SE
C
(Note 9) B
(Note 9) A
N
P
Scale calibration resistor
(Note 1)
Frequency meter
Variable coil type
1mA full-scale
{
{
Operation
status output
(open collector output)
Error output
(Relay output)
Short-circuit bar
Ground
Motor
IM
DC reactor FR-BEL (Note 6)
for power factor
improvement
(Option: refer to page 8.)
Main circuit terminal
Control circuit input terminal
Control circuit output terminal
(Note 3)
(Note 5)
RUN
EXT
EXT
PU
PU
RUN
STOP
MODE
SET
RESET
56
6
6
18.5
D2
Wiring hole
4
D1
D
5
5 hole
5
1
18
5
128
68
RUN
EXT
EXT
PU
PU
RUN
STOP
MODE
SET
RESET
W1
6
6
5
5 hole
5
118
5
128
W
18.5
D2
Wiring hole
Cooling fan*
D3
D1
D
3-phase 200V power supply
Capacity
0.1/0.2K
0.4K
0.75K
D
80.5
112.5
132.5
D1
10
42
62
D2
52
52
52
Single-phase 200V power supply
Capacity
0.1/0.2K
0.4K
0.75K
D
80.5
142.5
162.5
D1
10
42
62
D2
52
82
82
Single-phase 100V power supply
Capacity
0.1K
0.2K
0.4K
D
80.5
110.5
142.5
D1
10
10
42
D2
52
82
82
3-phase 200V power supply
Capacity
1.5/2.2K
3.7K
W
108
170
W1
96
158
D
135.5
142.5
Terminal symbol
R, S, T
U, V, W
N
10
Main circuit
Control circuit (input signal)
Control circuit (output signal)
Communication
Power supply input
Inverter output
DC voltage common
Grounding
Multi-speed selection
Connect to the commercial power supply.
Connect to the 3-phase squirrel cage motor.
This is the DC voltage common terminal. It is not insulated from the power supply and inverter output.
This is for grounding the inverter chassis. Always ground the inverter.
Detailed explanation
D1
65
72
D2
52
52
D3
8
5
3-phase 400V power supply
Capacity
0.4/0.75K
1.5K
2.2K
3.7K
W
108
108
108
108
W1
96
96
96
96
D
129.5
135.5
155.5
165.5
D1
59
65
65
65
D2
52
52
72
82
D3
5
8
8
8
Capacity
1.5K
W
108
W1
96
D
155.5
D1
65
D2
72
D3
8
Single-phase 200V power supply
Capacity
0.75K
W
108
W1
96
D
149.5
D1
59
D2
72
D3
5
Single-phase 100V power supply
*The FR-S510W-0.75K FR-S540-0.4K,0.75K does not have a cooling fan.
(Notes)
Forward run start
Reverse run start
Multi-speed selection
(high speed)
Multi-speed selection
(medium speed)
Multi-speed selection
(low speed)
1. The L level refers to when the open collector output transistor is ON (continuity state). The H level
refers to when the transistor is OFF (non-continuity state).
2. This is provided only with the type having the RS-485 function.
(Notes)
SINK
SOURCE
SD
Contact input
common (sink)
Frequency setting
(voltage signal)
Frequency setting
input common
Frequency setting
(current signal)
Error output
(relay output)
Inverter running
Open collector common
Display connection
RS-485 connector
(Note 2)
This is the common terminal for the terminal RUN. This is insulated from terminal 5 and terminal SD.
External transistor
common 24VDC
power supply
contact input
common (source)
When connecting a transistor output (open collector output) such as
a programmable controller (PLC), malfunctioning caused by the supplied
current can be prevented by connecting the external power supply common
for the transistor output to this terminal.This can be used as the 24VDC 0.1A
power supply between terminals PC and SD. When the source logic is
selected, this will be the common terminal for the contact input signal.
PC
2
5
4
A, B, C
RUN
SE
FM
—
Power factor
improvement
DC reactor connection
Terminal name
Remove the short-circuit bar between terminals P and P1 and connect the optional power factor
improvement DC reactor (FR-BEL). (This cannot be connected with the FR-S510W- K(-R).)
This functions as the forward run command when the STF signal is ON,
and the stop command when the signal is OFF.
This functions as the reverse run command
when the STR signal is ON, and the stop
command when the signal is OFF.
The multi-speed type can be selected
by combining the terminal RH, RM and RL
signal short circuits.
If the STF and STR signals turn ON simultane-
ously, these will function as the stop com-
mand.The terminal function will change accord-
ing to the input terminal selection (Pr. 60 to Pr.
63) Refer to the input signals in the common
specifications on page 4 for details on the ter-
minal functions that can be changed.
This is the common terminal for the contact input
(terminals STF, STR, RH, RM, RL) and meter connection (terminal FM).
Terminal 5 and terminal SE are insulated.
Frequency setting
power supply
5VDC. Tolerable load current 10mA.
This is the common terminal for the frequency setting signal (terminal 2, 4).
This is insulated from terminal SD and terminal SE.
Do not ground this common.
Input 4 to 20mA DC.The default setting is adjusted to 0Hz at 4mA and
60Hz at 20mA.The maximum tolerable input current is 30mA,
and the input resistance is appoximately 250
.
When 0 to 5VDC (0 to 10V) is input, the maximum output frequency will be
reached at 5V (10V), and the input/output will be proportional.
Change between 5V and 10V with Pr. 73.
The input resistance is 10k
, and the maximum tolerable input voltage is 20V.
1 relay output which indicates that the inverter protective function
has activated and the output has stopped. 230VAC 0.3A 30VDC
0.3A. When there is an error, there is non-continuity between B-C
(continuity between A-C), and during normal operation, there is
continuity between B-C (non-continuity between A-C).
The L level is output when the inverter output frequency is higher than the
starting frequency (0.5Hz default can be changed). The H level is output when
stopped or during DC braking (Note 1). The tolerable load is 24VDC 0.1A.
The inverter is set so that the terminals FM to SD will output approximately
1mA at 60Hz (default value). The output frequency is proportional. The out-
put voltage is a pulse waveform, so a digital display can be connected.
Pulse specifications: 1440 pulses/s at 60Hz.
Communication with RS-485 is possible.
•Standard compliance: EIA Standards RS-485
•Transmission format: Multidrop link method
•Communication speed: Max. 19200 baud, •Total length: 500m
The parameter unit FR-PU04 can be connected using the parameter unit
connection cable FR-CB201 to 205.
P, P1
Forward run start
STF
STR
RH, RM, RL
Reverse run start
(Note 7)
(Note 9) RUN
The terminal function
will change according
to the output terminal
function selection
(Pr.64,65). Refer to the
output signals in the
common specifications
on page 4 for details on
the terminal functions
that can be changed.
Frequency setting signal (0 to 5 (10)VDC), 4 to 20mA, digital setting with setting dial, start signal, error reset (RES), multi-speed selection
(RL, RM, RH, REX), 2nd function selection (RT), output stop (MRS), current input selection (AU), external thermal input (OH), start self-
hold selection (STOP), JOG mode selection (JOG), PID action selection (X14), PU operation/external operation changeover (X16)
One type of open collector output can be selected from inverter running (RUN), frequency reached (SU), frequency detection (FU), overload
warning (OL), zero current detection (Y13), output current detection (Y12), PID upper limit (FUP), PID lower limit (FDN), PID forward/
reverse run (RL), READY (RY), minor failure (LF), and error (A, B, C). One type can be selected for the contact output (1 contact, 230VAC 0.3A, 30VDC 0.3A).
0.1K
0.1
0.3
0.8
0.4
0.5
0.2K
0.2
0.5
1.4
0.7
0.5
0.4K
0.4
1.0
2.5
1.2
0.8
0.75K
0.75
1.6
4.1
2.1
0.9
1.5K
1.5
2.8
7.0
4.0
1.5
2.2K
2.2
4.0
10
5.5
1.5
3.7K
3.7
6.6
16.5
9
2.1
0.4K
0.4
0.9
1.1
1.5
1.5
0.75K
0.75
1.6
2.1
2.5
1.5
1.5K
1.5
2.7
3.5
4.5
1.5
2.2K
2.2
3.7
4.8
5.5
1.6
3.7K
3.7
5.9
7.7
9.5
1.7
0.1K
0.1
0.3
0.8
0.5
0.5
0.2K
0.2
0.5
1.4
0.9
0.6
0.4K
0.4
1.0
2.5
1.5
0.8
0.75K
0.75
1.6
4.1
2.5
1.0
1.5K
1.5
2.8
7.0
4.4
1.5
0.1K
0.1
0.3
0.8
0.5
0.6
0.2K
0.2
0.5
1.4
0.9
0.7
0.4K
0.4
1.0
2.5
1.5
0.9
0.75K
0.75
1.6
4.1
2.5
1.6
Specifications
Type
Applicable motor capacity (kW) (Note 1)
Output
Power supply
Protective structure (JEM 1030)
Cooling method
Approximately weight (kg)
Rated capacity (kVA)(Note 2)
Rated current (A)
Overload current rating (Note 3)
Voltage (Note 4)(Note 6)
Rated input AC voltage/frequency
Tolerable AC voltage fluctuation
Tolerable frequency fluctuation
Power facility capacity (kVA)(Note 5)
3-phase 200V
FR-S520-
ⵧⵧ
Single-phase 200V
FR-S520S-
ⵧⵧ
Single-phase 100V
FR-S510W-
ⵧⵧ
3-phase 200 to 240V, 50/60 Hz
Single-phase 200 to 240V, 50/60Hz
170 to 264V, 50/60Hz
3-phase 380V to 480V, 50/60 Hz
3-phase 380V to 480V, 50/60 Hz
325V to 528V, 50/60Hz
3-phase 200V to 230V, 50/60Hz
Single-phase 100V to115V, 50/60Hz
90V to 132V, 50/60Hz
Self-cooling
3-phase 200 to 240V, 50/60 Hz
3-phase 200 to 240V, 50/60 Hz
170 to 264V, 50/60Hz
Enclosed type (IP20) (Fully enclosed structure series is IP40)
Within
5%
Enclosed type (IP20)
Self-cooling
Forced cooling
Self-cooling
Forced cooling
3-phase 400V
FR-S540-
ⵧⵧ
Self-cooling
Forced cooling
150% for 60 s, 200% for 0.5 s (Inverse time characteristics)
{
{
4
5