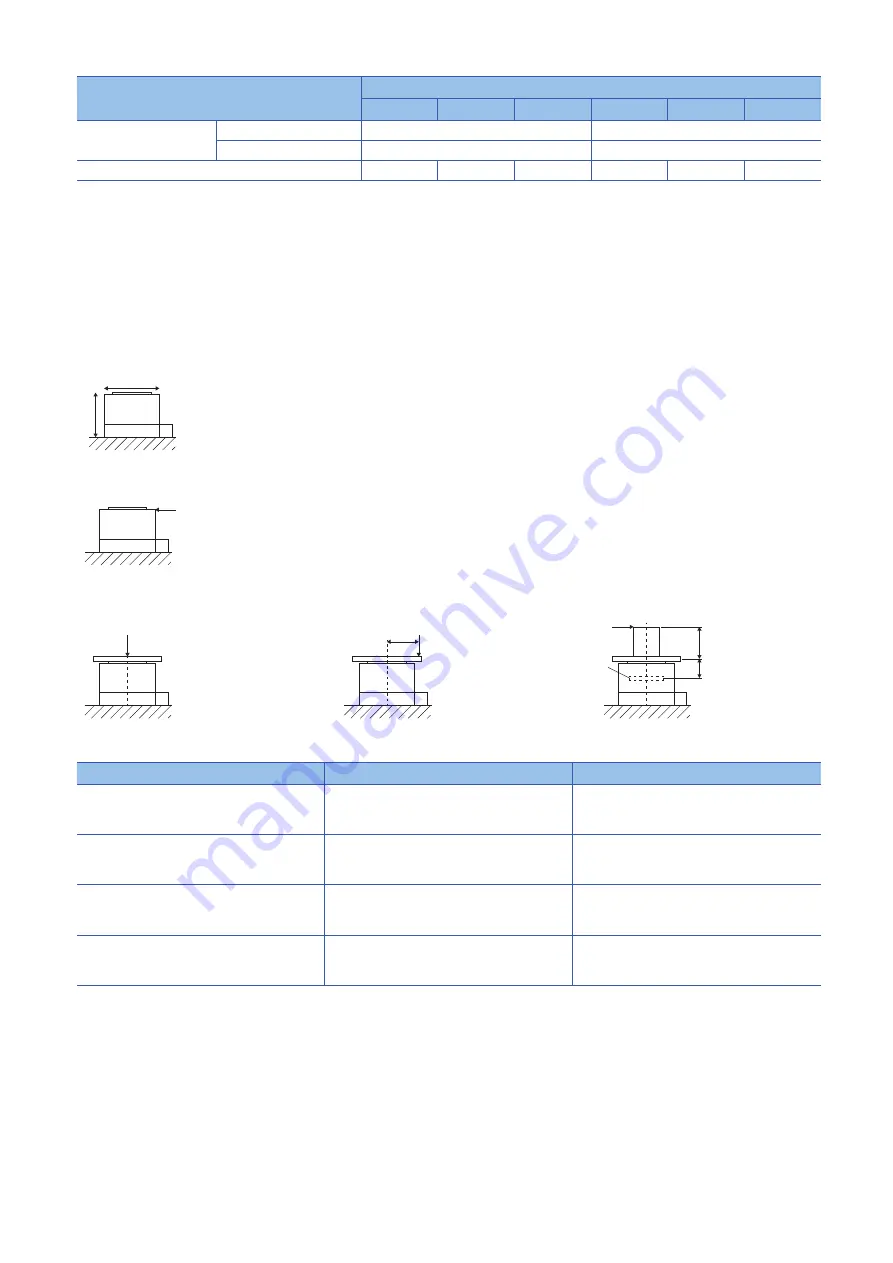
44
7 TM-RFM SERIES
7.2 Specification list
*1 When the power supply voltage drops, the output and the rated speed cannot be guaranteed.
*2 If the load to motor inertia ratio exceeds the indicated value, contact your local sales office.
*3 To configure the absolute position detection system, connect to a battery unit and an absolute position storage unit. Refer to the
following for the absolute position storage unit.
Page 41 Absolute position storage unit MR-BTAS01
For the battery, refer to "Battery" in the following manual.
MR-J5 User's Manual (Hardware)
*4 The shaft-through portion of the rotor and the connector area are excluded. IP classifies the degree of protection provided against the
intrusion of solid objects and water in electrical enclosures.
*5 The vibration direction is as shown in the figure. The numerical value indicates the maximum value. When the direct drive motor stops,
fretting is likely to occur at the bearing. Therefore, suppress the vibration to about half of the permissible value.
*6 V10 indicates that the amplitude of a direct drive motor as a single unit is 10
μ
m or less. The following figure shows the direct drive motor
mounting position for measurement and the measuring position.
*7 The axial and moment loads, which are applied to the direct drive motor's rotor (output shaft) during operation, must be maintained to be
equal to or below the permissible value. The following figure shows an example of the load applied during operation.
*8 The absolute accuracy changes depending on the mounting condition of the load and the surrounding environment.
Rotor permissible load
Moment load [N•m]
93
350
Axial load [N]
5500
16000
Mass [kg]
17
36
52
53
91
146
Direct drive motor
Motor OD [mm]
Dimension A [mm]
TM-RFM002C20
TM-RFM004C20
TM-RFM006C20
φ
130
19.1
TM-RFM006E20
TM-RFM012E20
TM-RFM018E20
φ
180
20.2
TM-RFM012G20
TM-RFM048G20
TM-RFM072G20
φ
230
24.4
TM-RFM040J10
TM-RFM120J10
TM-RFM240J10
φ
330
32.5
Item
TM-RFM series
012G20
048G20
072G20
040J10
120J10
240J10
X
Y
Measuring position
F
L F
L
A
(External force)
(External force)
Axial load = F + mass of load
Axial load = F + mass of load
Moment load = F × L
Axial load = mass of load
Moment load = F × (L + A)
F (External force)
Bearings
Содержание TM-RF004C20
Страница 1: ...Direct Drive Motor User s Manual TM RFM TM RG2M TM RU2M Mitsubishi Electric AC Servo System ...
Страница 2: ......
Страница 67: ...10 APPENDIX 10 1 Fabricating the encoder cable 65 10 MEMO ...
Страница 71: ......