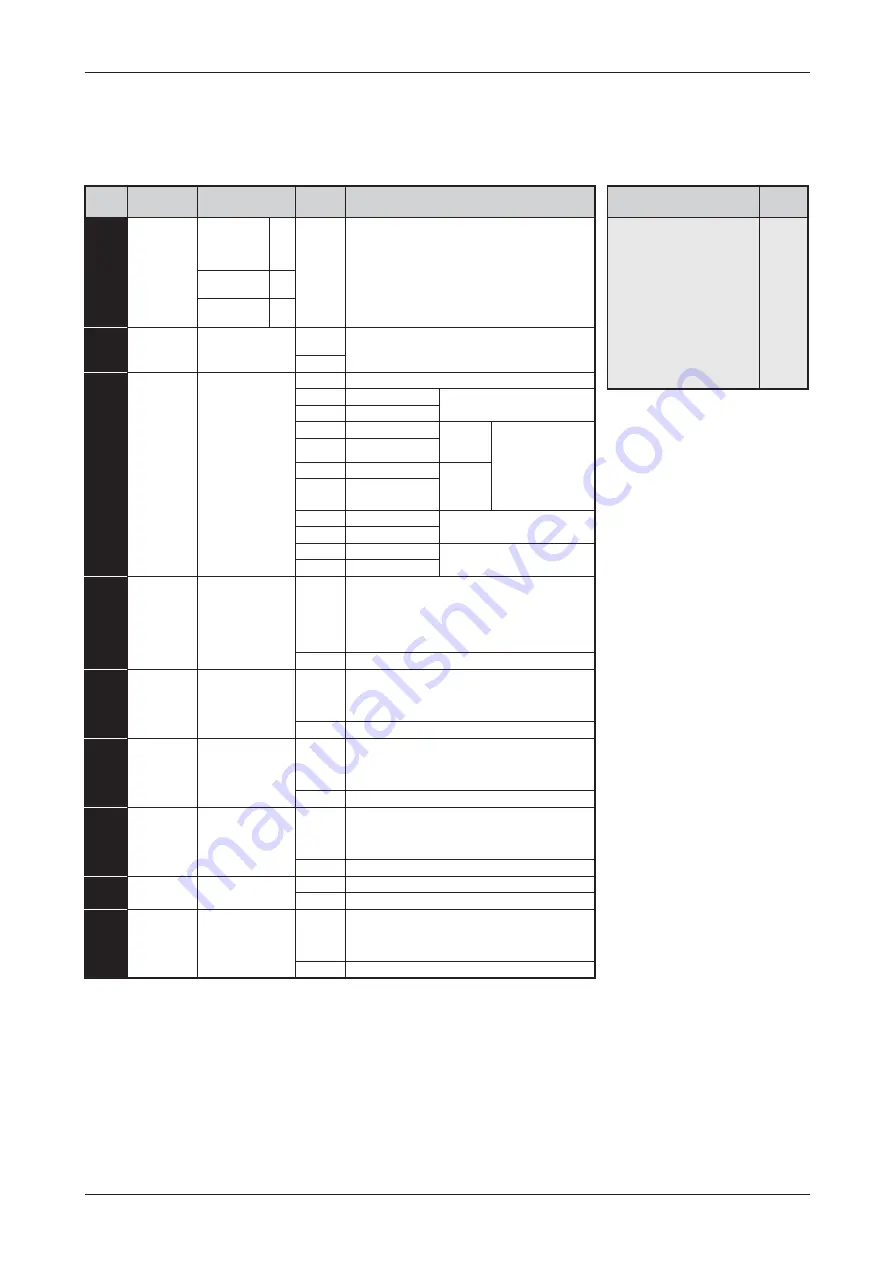
Parameter
Special operation
FR-E700 SC EC/ENE
6 - 305
6.20.2
Dancer control (Pr. 44, Pr. 45, Pr. 128 to Pr. 134)
Performs PID control by feedbacking the position detection of the dancer roller, controlling the danc-
er roller is in the specified position.
The above parameters can be set when Pr. 160 "User group read selection" = 0.
햲
This parameter allows its setting to be changed during operation in any operation mode even if
"0" (initial value) is set in Pr. 77 "Parameter write selection".
Pr. No. Name
Initial Value
Setting
Range
Description
Parameters referred to
Refer to
Section
44
Second
acceleration/
deceleration time
FR-E720S-110SC or
less
FR-E740-095SC
or less
5 s
0–3600/
360 s
This parameter is the acceleration time of the main speed during
dancer control. It will not function as second acceleration/
deceleration time.
59
73
79
178–184
190–192
C2 (Pr. 902)
–
C7 (Pr. 905)
Remote function
selection
Analog input
selection
Operation mode
selection
Input terminal
function selection
Output terminal
function selection)
Frequency setting
voltage (current)
bias/gain
FR-E740-120SC
and 170SC
10 s
FR-E740-230SC
and 300SC
15 s
45
Second
deceleration time
9999
0–3600/
360 s
This parameter is the deceleration time of the main speed during
dancer control. It will not function as second deceleration time.
9999
128
PID action
selection
0
0
PID action is not performed
20
PID reverse action
Measured value (terminal 4)
Set value (terminal 2 or Pr. 133)
21
PID forward action
40
PID reverse action
Addition
method:
fixed
For dancer control set
point (Pr. 133),
measured value
(terminal 4)
main speed (speed
command of the operation
mode)
41
PID forward action
42
PID reverse action
Addition
method:
ratio
43
PID forward action
50
PID reverse action
Deviation value signal input
(LONWORKS, CC-Link communication)
51
PID forward action
60
PID reverse action
Set point and measured value input
(LONWORKS, CC-Link communication)
61
PID forward action
129
PID proportional
band
햲
100%
0.1
–
1000%
If the proportional band is narrow (parameter setting is small), the
manipulated variable varies greatly with a slight change of the
measured value. Hence, as the proportional band narrows, the
response sensitivity (gain) improves but the stability deteriorates,
e.g. hunting occurs.
Gain Kp = 1/proportional band
9999
No proportional control
130
PID integral time
햲
1 s
0.1
–
3600 s
For deviation step input, time (Ti) required for only the integral (I)
action to provide the same manipulated variable as that for the
proportional (P) action. As the integral time decreases, the set
point is reached earlier but hunting occurs more easily.
9999
No integral control.
131
PID upper limit
9999
0–100%
Maximum value
If the feedback value exceeds the setting, the FUP signal is output.
The maximum input (20 mA/5 V/10 V) of the measured value
(terminal 4) is equivalent to 100%.
9999
No function
132
PID lower limit
9999
0–100%
Minimum value
If the process value falls below the setting range, the FDN signal is
output. The maximum input (20 mA/5 V/10 V) of the measured
value (terminal 4) is equivalent to 100%.
9999
No function
133
PID action set
point
햲
9999
0–100% Used to set the set point for PID control.
9999
Always 50%
134
PID differential
time
햲
9999
0.01
–
10.00 s
For deviation ramp input, time (Td) required for providing only the
manipulated variable for the proportional (P) action. As the
differential time increases, greater response is made to a deviation
change.
9999
No differential control.
Содержание fr-e700 series
Страница 2: ......
Страница 4: ......
Страница 20: ...Contents XVI ...
Страница 112: ...Operation panel Operation 4 20 ...
Страница 154: ...External operation Basic settings 5 42 ...
Страница 528: ...CC Link IE Field Network Basic Parameter 6 374 ...
Страница 562: ...Meters and measuring methods Troubleshooting 7 34 ...
Страница 606: ...A 30 Index Appendix ...
Страница 607: ......