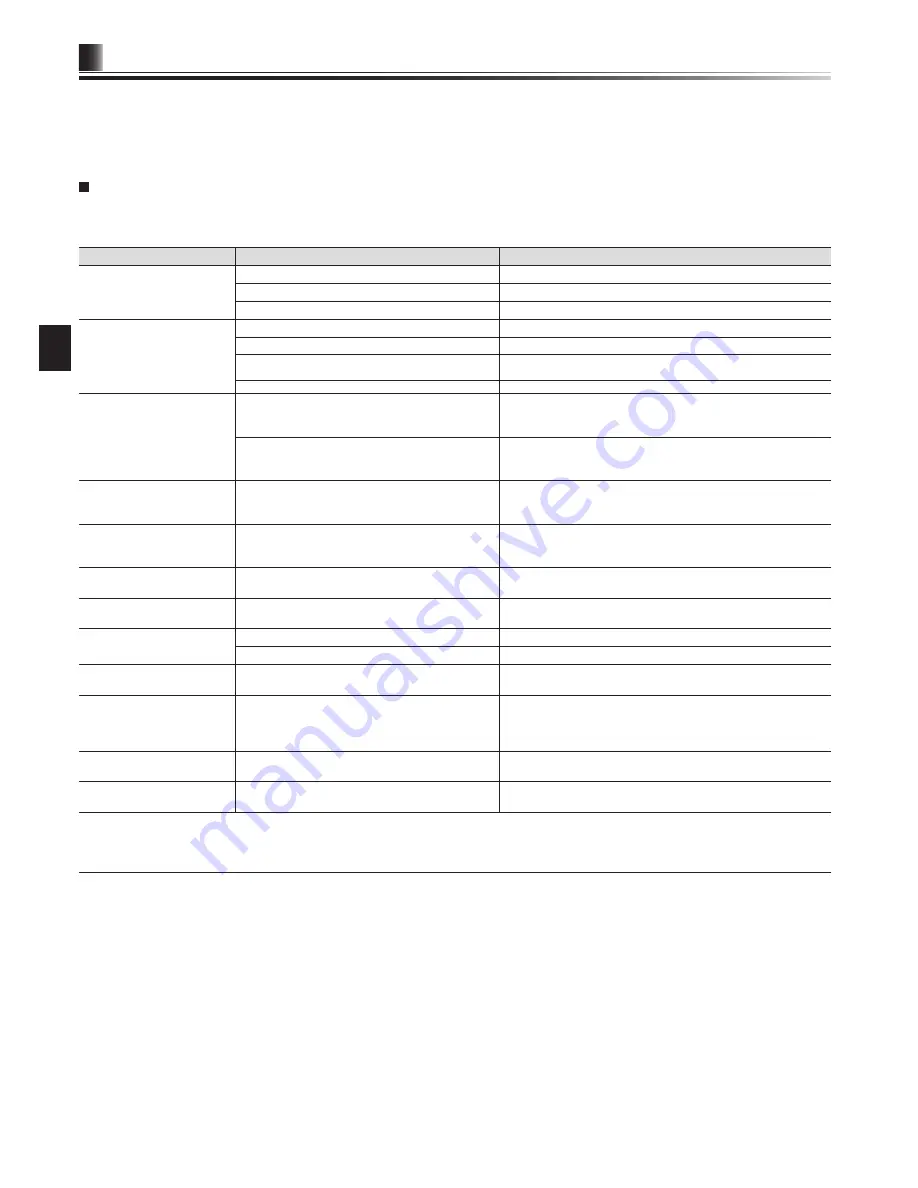
35
6
EN
Service and Maintenance
The indoor hydrobox must be serviced
once a year
by a qualified individual. Ser-
vicing and maintenance of the outdoor unit should only be done by a Mitsubishi
Electric trained technician with relevant qualifications and experience. Any electri-
cal work should be done by a tradesperson with the appropriate electrical quali-
fications. Any maintenance or ‘DIY’ fixes done by a non-accredited person could
invalidate the Warranty and/or result in damage to the hydrobox and injury to the
person.
Fault symptom
Possible cause
Solution
Cold water at taps
(systems with DHW tank)
Scheduled control off period
Check schedule settings and change if necessary.
All hot water from DHW tank used
Ensure DHW mode is operating and wait for DHW tank to re-heat.
Heat pump or electric heaters not working
Contact installer.
Heating system does not get up
to set temperature.
Prohibit, schedule or holiday mode selected
Check settings and change as appropriate.
Incorrectly sized radiators
Contact installer.
The room in which the temperature sensor is located is at
a different temperature to the rest of the house.
Reposition the temperature sensor to a more suitable room.
Battery problem *wireless control only
Check the battery power and replace if flat.
The cooling system does not cool
down to the set temperature.
(ONLY for ERS* models)
When the water in the circulation circuit is unduly hot,
Cooling mode starts with a delay for the protection of the
outdoor unit.
Normal operation
When the outdoor ambient temperature is significantly low,
Cooling mode does not start running to avoid freezing of
the water pipes.
If the freeze stat. function is not necessary, contact installer to change the
settings.
Heating emitter is hot in the DHW
mode. (The room temperature
rises.)
The 3-way valve may have foreign objects in it, or hot wa-
ter may flow to the heating side due to malfunctions.
Contact installer.
Schedule function inhibits the
system from operating but the
outdoor unit operates.
Freeze stat. function is active.
Normal operation no action necessary.
Pump runs without reason for
short time.
Pump jam prevention mechanism to inhibit the build up of
scale.
Normal operation no action necessary.
Mechanical noise heard coming
from hydrobox
Heaters switching on/off
Normal operation no action required.
Noisy pipework
Air trapped in the system
Try bleeding radiators (if present) If the symptoms persist contact installer.
Loose pipework
Contact installer.
Water discharges from one of the
relief valves
The system has overheated or overpressurised
Switch off power to the heat pump and any immersion heaters then con-
tact installer.
Small amounts of water drip from
one of the relief valves.
Dirt may be preventing a tight seal in the valve
Twist the valve cap in the direction indicted until a click is heard. This will
release a small amount of water flushing dirt from the valve. Be very care-
ful the water released will be hot. Should the valve continue to drip contact
installer as the rubber seal may be damaged and need replacing.
An error code appears in the
main remote controller display.
The indoor or outdoor unit is reporting an abnormal condi-
tion
Make a note of the error code number and contact installer.
Heat pump is forced to turn ON
and OFF.
Smart grid ready input (IN11 and IN12) is used, and
switch-on and off commands are input.
Normal operation no action necessary.
<Power failure>
All setting will be saved for 1 week with no power, after 1 week Date/Time ONLY will be saved.
Basic Troubleshooting for Hydrobox
The following table is to be used as a guide to possible problems. It is not exhaustive and all problems should be investigated by the installer or another competent person.
Users should not attempt to repair the system themselves.
At no time should the system be operating with the safety devices by-passed or plugged.
For more details, refer to the service manual.
<Draining the hydrobox>
WARNING: DRAINED WATER MAY BE VERY HOT
1. Before attempting to drain the hydrobox islolate from the electrical supply to prevent booster heater burning out.
2. Isolate hydrobox from primary water circuit and drain water from hydrobox. Use a suitable heat resistant hose to assist in these operations.
3. Drain any remaining water from booster heater using fitted drain cock and hose to safely drain the unit.
4. After the hydrobox is drained, water remains in the following component parts. Drain water completely by checking the inside of the parts.
• Strainer (Remove the strainer cover.)
• Pressure relief valve (Operate the valve.)