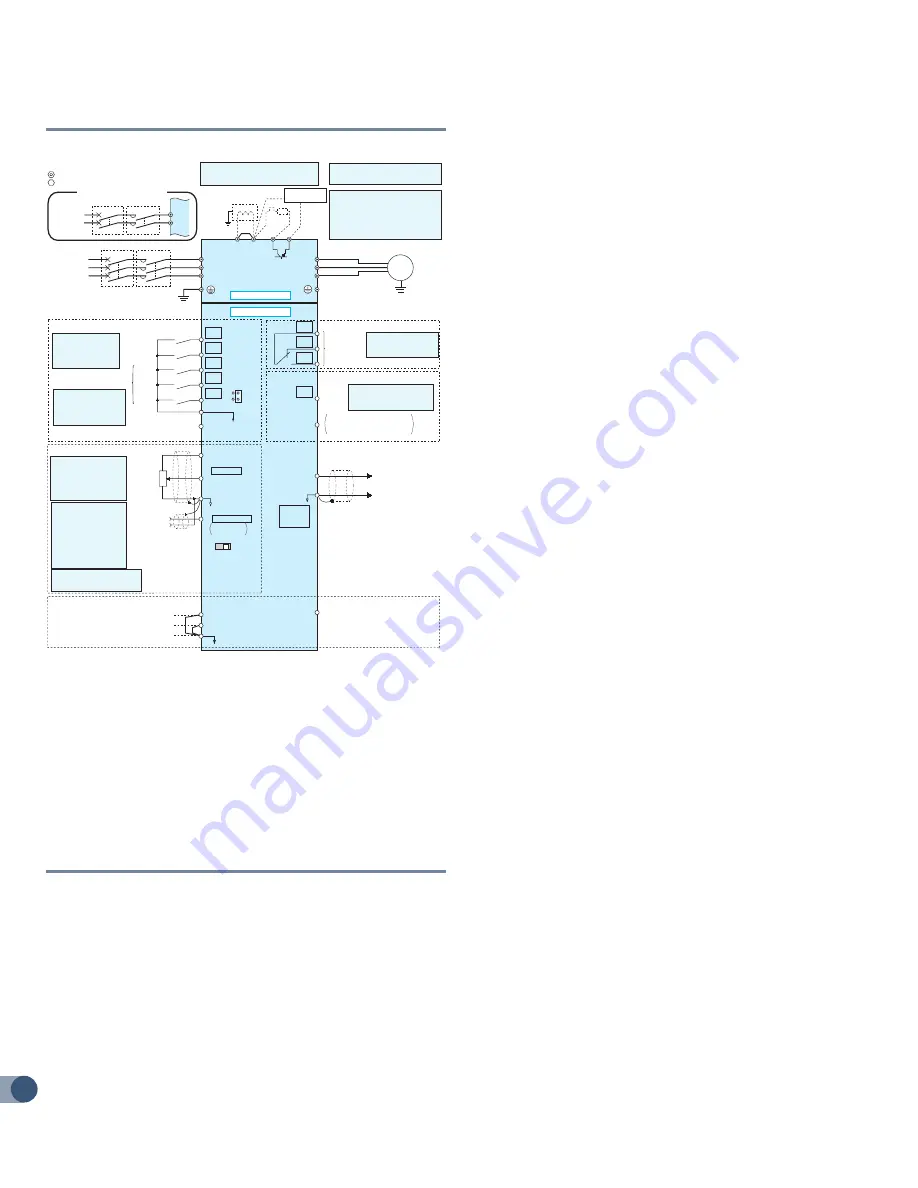
D700 QUICK START MANUAL
6
4. WIRING
Terminal connection diagram
NOTE
• To prevent a malfunction caused by noise, separate the signal
cables more than 10cm (3.93 inch) from the power cables. Also
separate the main circuit wire of the input side and the output side.
• After wiring, wire offcuts must not be left in the inverter. Wire offcuts
can cause an alarm, failure or malfunction. Always keep the inverter
clean. When drilling mounting holes in an enclosure etc., take care
not to allow chips and other foreign matter to enter the inverter.
• The output of the single-phase power input specification is three-
phase 200V.
5. PRECAUTIONS FOR USE OF THE INVERTER
The FR-D700 series is a highly reliable product, but incorrect
peripheral circuit making or operation/handling method may shorten
the product life or damage the product. Before starting operation,
always recheck the following items.
1. Use crimping terminals with insulation sleeve to wire the power
supply and motor.
2. Application of power to the output terminals (U, V, W) of the inverter
will damage the inverter. Never perform such wiring.
3. After wiring, wire offcuts must not be left in the inverter. Wire offcuts
can cause an alarm, failure or malfunction. Always keep the inverter
clean. When drilling mounting holes in an enclosure etc., take care
not to allow chips and other foreign matter to enter the inverter.
4. Use cables of the size to make a voltage drop 2% maximum. If
the wiring distance is long between the inverter and motor, a main
circuit cable voltage drop will cause the motor torque to decrease
especially at the output of a low frequency. Refer to page 6 for the
recommended wire sizes.
5. The overall wiring length should be 500m (1640.42 feet) maximum.
Especially for long distance wiring, the fast-response current
limit function may decrease or the equipment connected to the
secondary side may malfunction or become faulty under the
influence of a charging current due to the stray capacity of the
wiring. Therefore, note the overall wiring length.
6. Electromagnetic wave interference. The input/output (main circuit)
of the inverter includes high frequency components, which may
interfere with the communication devices (such as AM radios) used
near the inverter. In this case, install the FR-BIF optional capacitor
type filter (for use in the input side only) or FR-BSF01 common
mode filter to minimize interference.
7. Do not install a power factor correction capacitor, surge suppressor
or capacitor type filter on the inverter output side. This will cause
the inverter to trip or the capacitor and surge suppressor to be
damaged. If any of the above devices are connected, immediately
remove them. When using capacitor type filter (FR-BIF) for single-
phase power supply specification, make sure of secure insulation of
T-phase, and connect to the input side of the inverter.
8. Before starting wiring or other work after the inverter is operated,
wait for at least 10 minutes after the power supply has been switched
off, and check that there are no residual voltage using a tester or the
like. The capacitor is charged with high voltage for some time after
power off and it is dangerous.
9. A short circuit or earth (ground) fault on the inverter output side may
damage the inverter modules.
Fully check the insulation resistance of the circuit prior to inverter
operation since repeated short circuits caused by peripheral
circuit inadequacy or an earth (ground) fault caused by wiring
inadequacy or reduced motor insulation resistance may damage
the inverter modules.
Fully check the to-earth (ground) insulation and phase to phase
insulation of the inverter output side before power-on.
Especially for an old motor or use in hostile atmosphere, securely
check the motor insulation resistance etc.
10. Do not use the inverter input side magnetic contactor to start/stop
the inverter. Always use the start signal (turn ON/OFF STF, STR
signal) to start/stop the inverter.
11. Across P/+ and PR terminals, connect only an external regenerative
brake discharging resistor. The brake resistor can not be connected
to the FR-D720-008 and 014, FR-D720S-008 and 014. Do not
connect a mechanical brake. Leave terminals P/+ and PR open.
Also, never short between P/+ and PR.
12. Do not apply a voltage higher than the permissible voltage to the
inverter I/O signal circuits. Application of a voltage higher than the
permissible voltage to the inverter I/O signal circuits or opposite
polarity may damage the I/O devices. Especially check the wiring
to prevent the speed setting potentiometer from being connected
incorrectly to short terminals 10-5.
13. Provide electrical and mechanical interlocks for MC1 and MC2
which are used for bypass operation. When the wiring is incorrect
and if there is a bypass operation circuit as shown right, the inverter
will be damaged when the power supply is connected to the inverter
U, V, W terminals, due to arcs generated at the time of switch-over
or chattering caused by a sequence error.
Earth
(Ground)
Motor
IM
Earth (Ground)
Three-phase
AC power
supply
MCCB
MC
R/L1
P1
P/+
PR N/-
S/L2
T/L3
U
V
W
Earth
(Ground)
*7 Brake resistor (FR-ABR, MRS type, MYS
type)
Install a thermal relay to prevent an
overheat and burnout of the brake resistor.
(The brake resistor can not be connected
to the FR-D720-008 and 014, FR-D720S-
008 and 014.)
Forward
rotation start
Reverse
rotation start
Middle
speed
High
speed
Low
speed
Control input signals (No voltage input allowed)
24VDC power supply
(Common for external power supply transistor)
Contact input common
STR
STF
RH
RM
RL
SD
PC
Relay output
Running
Open collector output
Open collector output common
Sink/source common
RUN
SE
A
B
C
Frequency setting signals (Analog)
2 0 to 5VDC
10(+5V)
2
3
1
4 4 to 20mADC
Frequency
setting
potentiometer
1/2W1k
Ω
Terminal 4
input
(Current
input)
(+)
(-)
5(Analog common)
*5 It is recommended to use 2W1k
Ω
when the frequency setting signal
is changed frequently.
*5
*2 When using terminals PC-
SD as a 24VDC power
supply, take care not to
short across terminals
PC-SD.
PU
connector
*
1. DC reactor (FR-HEL)
When connecting a DC reactor, remove the
jumper across P1-P/+
Control circuit terminal
Main circuit terminal
Sink logic
Jumper
*1
*7
*6
*2
*3
*4
Terminal functions vary
with the input terminal
assignment (
Pr. 178 to
Pr. 182
)
Multi-speed selection
Terminal functions vary by
Pr. 190 RUN terminal function
selection
Terminal functions vary
by
Pr. 192
A,B,C terminal
function selection
SINK
SOURCE
V
I
*4
0 to 5VDC
(0 to 10VDC)
0 to 10VDC
*4 Terminal input
specifications can be
changed by analog input
specifications switchover
(
Pr. 267
). Set the
voltage/current input
switch in the "
V" position
to select voltage input (0
to 5V/0 to10V) and "
I"
(initial value) to select
current input (4 to 20mA).
Voltage/current
input switch
Main circuit
Control circuit
R
Relay output
(Fault output)
Brake unit
(Option)
*3 Terminal input specifications
can be changed by analog
input specifications
switchover (
Pr. 73
).
Terminal 10 and terminal 2
are used as PTC input
terminal (
Pr. 561
).
Output shutoff (Line 1)
Output shutoff (Line 2)
Common terminal
Safety stop signal
S1
S2
SC
For manufacturer setting
SO
Shorting
wire
Single-phase
AC power
supply
MCCB
MC
R/L1
S/L2
Single-phase power input
*6 A brake transistor is not built-in to the
FR-D720-008 and 014, FR-D720S-008
and 014.
AM
5
(+)
(-)
Analog signal output
(0 to 10VDC)
MitsubishiElectric Automation, Inc.