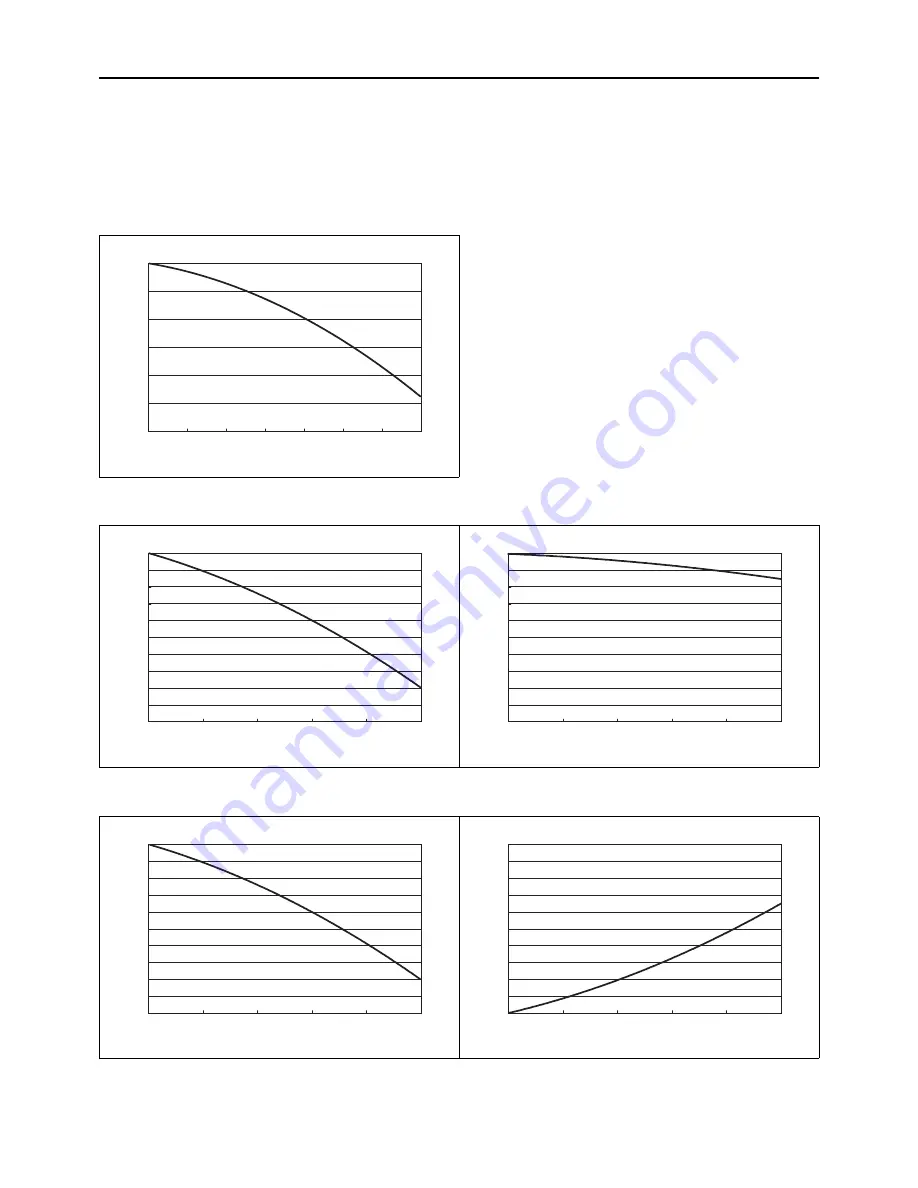
[
I
Read Before Servicing ]
- 17 -
HWE1410A
GB
3. Correction by antifreeze-liquid concentration
In HYBRID CITY MULTI system, antifreeze-liquid should be used to prevent the system from freezing. Refer to the following graphs
for the capacity correction by antifreeze-liquid. Refer to (1) for antifreeze-liquid concentration, (2) and (3) for capacity correction by
antifreeze-liquid concentration.
When adding antifreeze-liquid, be sure to perform the process in accordance with the relevant local laws and regulations.
(1) Antifreeze-liquid concentration
Use propylene glycol solution for antifreeze.
Refer to the following graph to estimate the antifreeze-liquid concentration required for freeze protection.
(2) Capacity correction by antifreeze-liquid concentration (cooling)
(3) Capacity correction by antifreeze-liquid concentration (heating)
0
10
20
30
40
50
60
70
Freezing T
e
mperature
[°C
]
0
-5
-10
-15
-20
-25
-30
Antifreeze-liquid concentration [wt%]
0
10
20
30
40
50
R
a
ti
o of c
o
olin
g c
a
p
a
c
it
y
1
0.99
0.98
0.97
0.96
0.95
0.94
0.93
0.92
0.91
0.9
Antifreeze-liquid concentration [wt%]
PURY-(E)P200~500YLM-A1,PQRY-P200~500YLM-A
0
10
20
30
40
50
R
a
ti
o of
cooling input
1
0.99
0.98
0.97
0.96
0.95
0.94
0.93
0.92
0.91
0.9
Antifreeze-liquid concentration [wt%]
0
10
20
30
40
50
R
a
ti
o
o
f heati
ng
capaci
ty
1
0.99
0.98
0.97
0.96
0.95
0.94
0.93
0.92
0.91
0.9
Antifreeze-liquid concentration [wt%]
PURY-(E)P200~500YLM-A1,PQRY-P200~500YLM-A
0
10
20
30
40
50
R
a
ti
o
o
f heati
n
g
input
1.2
1.18
1.16
1.14
1.12
1.1
1.08
1.06
1.04
1.02
1
Antifreeze-liquid concentration [wt%]
body1.fm 17 ページ 2016年1月14日 木曜日 午後3時29分
Содержание CITY MULTI CMB-WP1016V-GA1
Страница 1: ......
Страница 9: ...HWE1410A GB ...
Страница 11: ... 2 HWE1410A GB ...
Страница 27: ... I Read Before Servicing 18 HWE1410A GB ...
Страница 29: ... 20 HWE1410A GB ...
Страница 47: ... 38 HWE1410A GB ...
Страница 50: ... III HBC Controller Components 41 HWE1410A GB 4 Top side 1 CMB WP1016V GA1 2 CMB WP108V GA1 VB3f VB3e ...
Страница 52: ... III HBC Controller Components 43 HWE1410A GB 2 Top side 1 CMB WP1016V GB1 2 CMB WP108V GB1 VB3f VB3e ...
Страница 55: ... III HBC Controller Components 46 HWE1410A GB 2 Power supply circuit board ...
Страница 57: ... 48 HWE1410A GB ...
Страница 67: ... IV Electrical Wiring Diagram 58 HWE1410A GB ...
Страница 68: ... 59 HWE1410A GB V Refrigerant Circuit 1 Refrigerant Circuit Diagram 61 2 Principal Parts and Functions 64 ...
Страница 69: ... 60 HWE1410A GB ...
Страница 75: ... 66 V Refrigerant Circuit GB HWE1410A ...
Страница 77: ... 68 HWE1410A GB ...
Страница 95: ... 86 HWE1410A GB ...
Страница 117: ... VII Test Run Mode 108 HWE1410A GB ...
Страница 119: ... 110 HWE1410A GB ...
Страница 207: ... VIII Troubleshooting 198 HWE1410A GB ...
Страница 208: ... 199 HWE1410A GB IX LED Monitor Display on the Outdoor Unit Board 1 How to Read the LED on the Service Monitor 201 ...
Страница 209: ... 200 HWE1410A GB ...
Страница 292: ... IX LED Monitor Display on the Heat source Unit Board 283 HWE1410A 0000002394 book 283 ページ 2016年1月12日 火曜日 午後4時49分 ...
Страница 293: ... IX LED Monitor Display on the Heat source Unit Board 284 HWE1410A 0000002394 book 284 ページ 2016年1月12日 火曜日 午後4時49分 ...
Страница 294: ......