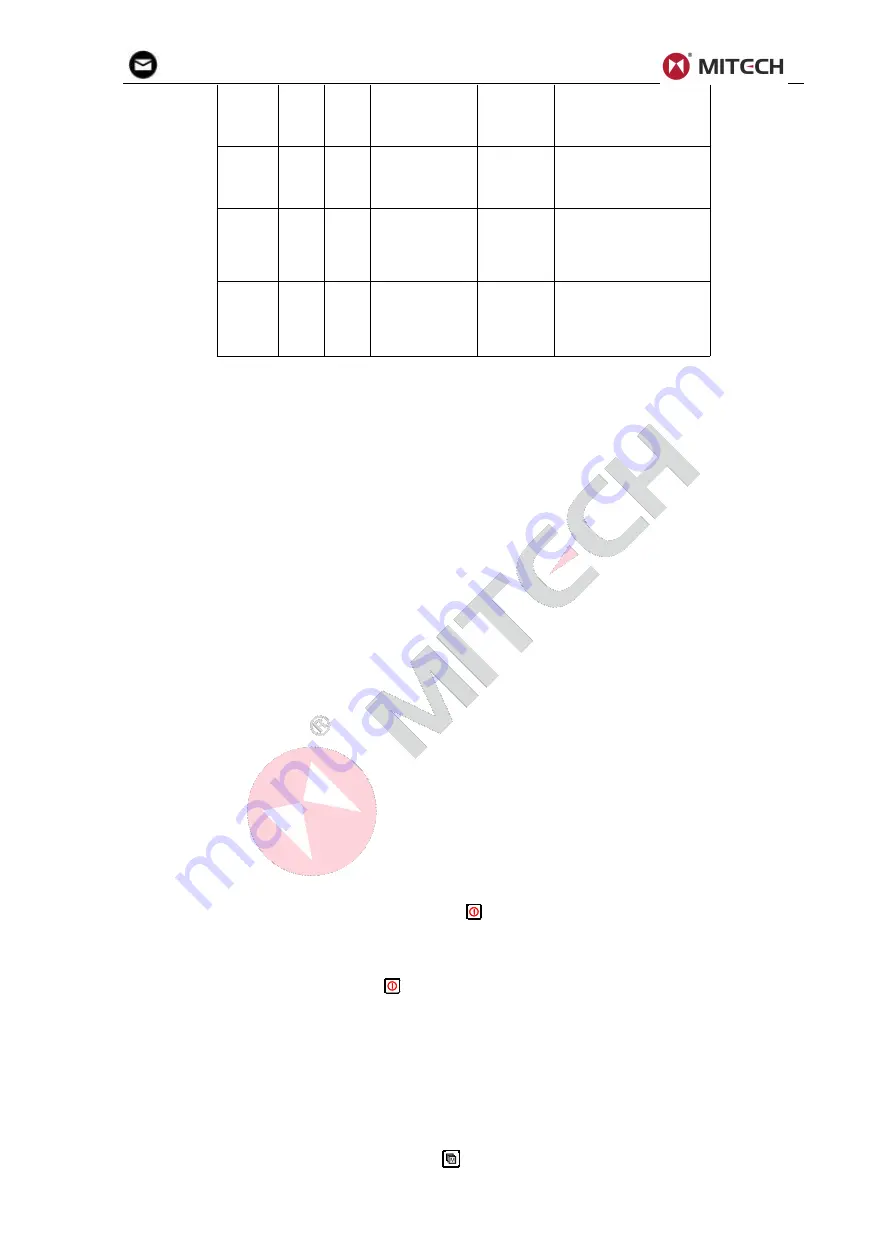
10
mvip@mitech-ndt.com
N05
5 10
1.2mm
~
230.0mm
(
In
Steel
)
Φ
20mm
×
3.0mm
Normal Measurement
N05
/90
°
5 10
1.2mm
~
230.0mm
(
In
Steel
)
Φ
20mm
×
3.0mm
Normal Measurement
N07
7 6
0.75mm
~
80.0mm
(
In Steel
)
Φ
15mm
×
2.0mm
For thin pipe wall or
small curvature pipe
wall measurement
HT5
5 14
3
~
200mm
(
In
Steel
)
30mm
For high temperature
(lower than 300
℃
)
measurement.
3.2 Condition and Preparation of Surfaces
In any ultrasonic measurement scenario, the shape and roughness of the test surface are of
paramount importance. Rough, uneven surfaces may limit the penetration of ultrasound through
the material, and result in unstable, and therefore unreliable, measurements. The surface being
measured should be clean, and free of any small particulate matter, rust, or scale. The presence of
such obstructions will prevent the transducer from seating properly against the surface. Often, a
wire brush or scraper will be helpful in cleaning surfaces. In more extreme cases, rotary sanders or
grinding wheels may be used, though care must be taken to prevent surface gouging, which will
inhibit proper transducer coupling.
Extremely rough surfaces, such as the pebble-like finish of some cast iron, will prove most
difficult to measure. These kinds of surfaces act on the sound beam like frosted glass on light, the
beam becomes diffused and scattered in all directions.
In addition to posing obstacles to measurement, rough surfaces contribute to excessive wear
of the transducer, particularly in situations where the transducer is “scrubbed” along the surface.
Transducers should be inspected on a regular basis, for signs of uneven wear of the wearface. If
the wearface is worn on one side more than another, the sound beam penetrating the test material
may no longer be perpendicular to the material surface. In this case, it will be difficult to exactly
locate tiny irregularities in the material being measured, as the focus of the sound beam no longer
lies directly beneath the transducer.
4 Operation
4.1 Power On/Off
The instrument is turned on by pressing the
key. When the gauge is initially turned on, the
model type, the manufacture information and the serial number will be displayed prior to entering
into the main measurement screen.
It is turned off by pressing the
key when it is on. The tool has a special memory that
retains all of its settings even when the power is off.
4.2 Transducer Set
The model of the transducer should be pre-set to the instrument before measuring operation.
This enables the user to select the transducer type among supported transducers according to
frequency and diameter depending on application requirements. Use the following steps to select
your transducer model
:
1. On the measurement screen, press the
key multiple times to activate the
【
Transducer