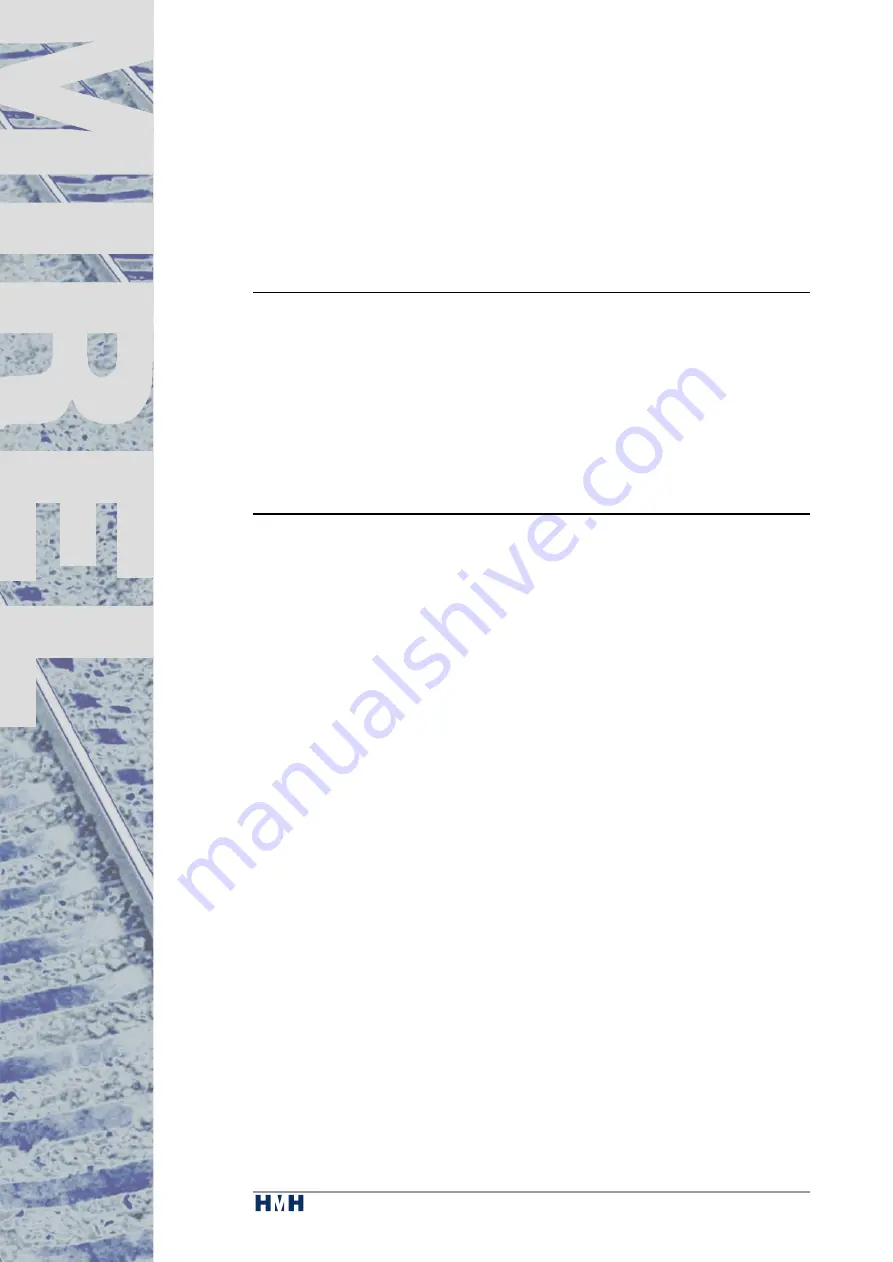
154VZ1 : 190111
22 / 33
is installed. D4 prophylactic control may be conducted in the standard scope or in an ex-
panded scope for version v04. Any future installations with conditions and difference that
have an impact on the scope and procedure for executing the D4 prophylactic control shall
be incorporated into D4 prophylactic control methodology.
Documents 675VZ1 and 498VZ1 have the methodology and template protocol for conduct-
ing the D4 prophylactic control on the MIREL VZ1 train protection system.
D4 prophylactic control is only conducted in full. In full means that prophylactic control was
conducted on the central unit, the signal repeaters and system interaction with the locomo-
tive.
Completion protocol:
The completion protocol for the prophylactic test must contain the following details:
§
Date of completion or the completion dates for the individual sections
§
Place or places of performance
§
The serial numbers of the system and the individual components
§
The number of the locomotive on which the equipment is installed
§
The name and position of the person who conducted the test
§
The results of the prophylactic control
§
A description of findings, nonconformity, faults, problems and deficiencies if identified
§
Signature of the person who conducted the test
Resolving nonconformity:
If a fault is detected, operational repairs (S1) of the system or maintenance repairs (S2) are
required depending on the nature of the detected problem.