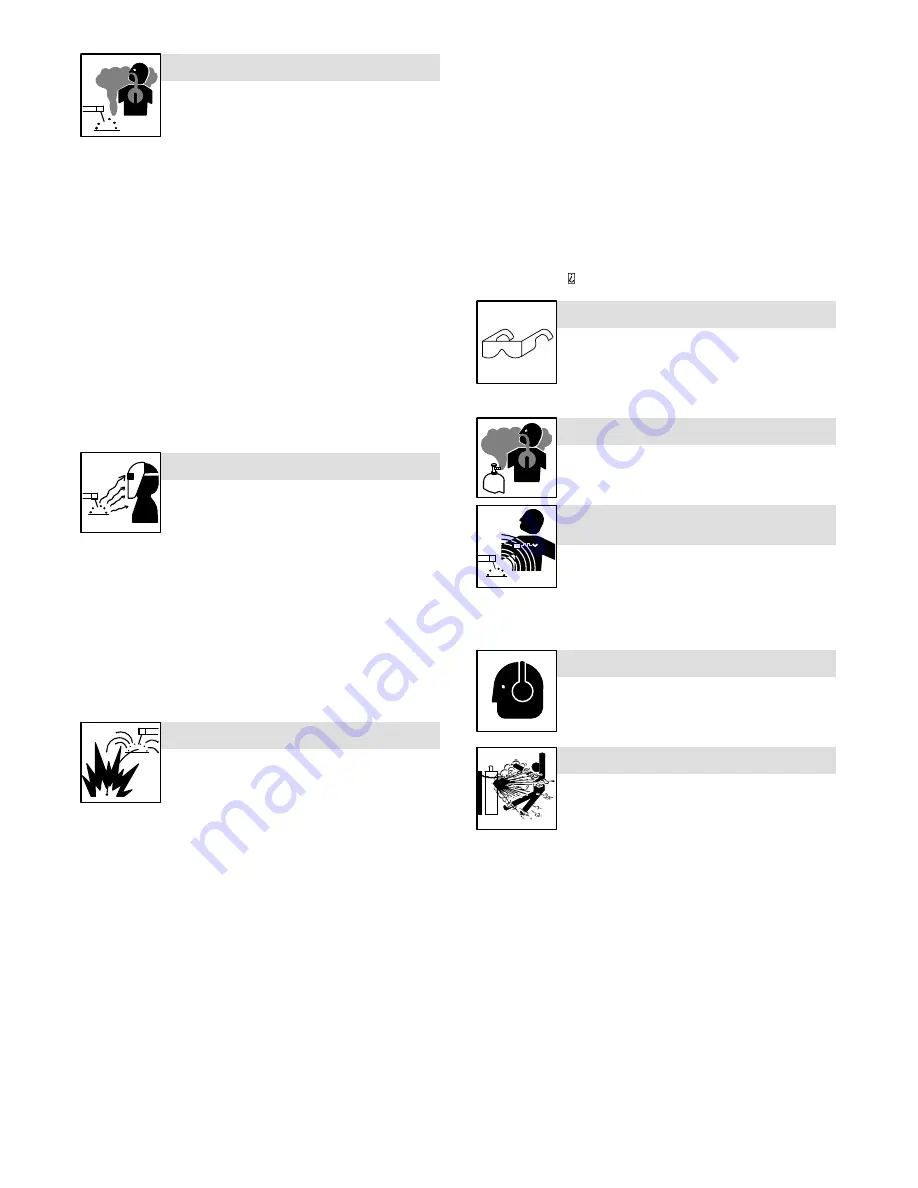
OM-239 982 Page 2
Welding produces fumes and gases. Breathing
these fumes and gases can be hazardous to your
health.
FUMES AND GASES can be hazardous.
D
Keep your head out of the fumes. Do not breathe the fumes.
D
If inside, ventilate the area and/or use local forced ventilation at the
arc to remove welding fumes and gases. The recommended way
to determine adequate ventilation is to sample for the composition
and quantity of fumes and gases to which personnel are exposed.
D
If ventilation is poor, wear an approved air-supplied respirator.
D
Read and understand the Safety Data Sheets (SDSs) and the
manufacturer’s instructions for adhesives, coatings, cleaners,
consumables, coolants, degreasers, fluxes, and metals.
D
Work in a confined space only if it is well ventilated, or while
wearing an air-supplied respirator. Always have a trained watch-
person nearby. Welding fumes and gases can displace air and
lower the oxygen level causing injury or death. Be sure the breath-
ing air is safe.
D
Do not weld in locations near degreasing, cleaning, or spraying op-
erations. The heat and rays of the arc can react with vapors to form
highly toxic and irritating gases.
D
Do not weld on coated metals, such as galvanized, lead, or
cadmium plated steel, unless the coating is removed from the weld
area, the area is well ventilated, and while wearing an air-supplied
respirator. The coatings and any metals containing these elements
can give off toxic fumes if welded.
Arc rays from the welding process produce intense
visible and invisible (ultraviolet and infrared) rays
that can burn eyes and skin. Sparks fly off from the
weld.
D
Wear an approved welding helmet fitted with a proper shade of
filter lenses to protect your face and eyes from arc rays and
sparks when welding or watching (see ANSI Z49.1 and Z87.1
listed in Safety Standards).
D
Wear approved safety glasses with side shields under your
helmet.
D
Use protective screens or barriers to protect others from flash,
glare and sparks; warn others not to watch the arc.
D
Wear body protection made from durable, flame
−
resistant mate-
rial (leather, heavy cotton, wool). Body protection includes
oil-free clothing such as leather gloves, heavy shirt, cuffless
trousers, high shoes, and a cap.
ARC RAYS can burn eyes and skin.
Welding on closed containers, such as tanks,
drums, or pipes, can cause them to blow up. Sparks
can fly off from the welding arc. The flying sparks, hot
workpiece, and hot equipment can cause fires and
burns. Accidental contact of electrode to metal objects can cause
sparks, explosion, overheating, or fire. Check and be sure the area is
safe before doing any welding.
WELDING can cause fire or explosion.
D
Remove all flammables within 35 ft (10.7 m) of the welding arc. If
this is not possible, tightly cover them with approved covers.
D
Do not weld where flying sparks can strike flammable material.
D
Protect yourself and others from flying sparks and hot metal.
D
Be alert that welding sparks and hot materials from welding can
easily go through small cracks and openings to adjacent areas.
D
Watch for fire, and keep a fire extinguisher nearby.
D
Be aware that welding on a ceiling, floor, bulkhead, or partition can
cause fire on the hidden side.
D
Do not weld on containers that have held combustibles, or on
closed containers such as tanks, drums, or pipes unless they are
properly prepared according to AWS F4.1 and AWS A6.0 (see
Safety Standards).
D
Do not weld where the atmosphere may contain flammable dust,
gas, or liquid vapors (such as gasoline).
D
Connect work cable to the work as close to the welding area as
practical to prevent welding current from traveling long, possibly
unknown paths and causing electric shock, sparks, and fire
hazards.
D
Do not use welder to thaw frozen pipes.
D
Remove stick electrode from holder or cut off welding wire at
contact tip when not in use.
D
Wear body protection made from durable, flame
−
resistant material
(leather, heavy cotton, wool). Body protection includes oil-free
clothing such as leather gloves, heavy shirt, cuffless trousers, high
shoes, and a cap.
D
Remove any combustibles, such as a butane lighter or matches,
from your person before doing any welding.
D
After completion of work, inspect area to ensure it is free of sparks,
glowing embers, and flames.
D
Use only correct fuses or circuit breakers. Do not oversize or by-
pass them.
D
Follow requirements in OSHA 1910.252 (a) (2) (iv) and NFPA 51B
for hot work and have a fire watcher and extinguisher nearby.
D
Read and understand the Safety Data Sheets (SDSs) and the
manufacturer s instructions for adhesives, coatings, cleaners,
consumables, coolants, degreasers, fluxes, and metals.
FLYING METAL or DIRT can injure eyes.
D
Welding, chipping, wire brushing, and grinding
cause sparks and flying metal. As welds cool,
they can throw off slag.
D
Wear approved safety glasses with side
shields even under your welding helmet.
BUILDUP OF GAS can injure or kill.
D
Shut off compressed gas supply when not in use.
D
Always ventilate confined spaces or use
approved air-supplied respirator.
ELECTRIC AND MAGNETIC FIELDS (EMF)
can affect Implanted Medical Devices.
D
Wearers of Pacemakers and other Implanted
Medical Devices should keep away.
D
Implanted Medical Device wearers should consult their doctor
and the device manufacturer before going near arc welding, spot
welding, gouging, plasma arc cutting, or induction heating
operations.
Noise from some processes or equipment can
damage hearing.
D
Wear approved ear protection if noise lev-
el is high.
NOISE can damage hearing.
Compressed gas cylinders contain gas under high
pressure. If damaged, a cylinder can explode. Since
gas cylinders are normally part of the welding
process, be sure to treat them carefully.
CYLINDERS can explode if damaged.
D
Protect compressed gas cylinders from excessive heat, mechani-
cal shocks, physical damage, slag, open flames, sparks, and arcs.
D
Install cylinders in an upright position by securing to a stationary
support or cylinder rack to prevent falling or tipping.
D
Keep cylinders away from any welding or other electrical circuits.
D
Never drape a welding torch over a gas cylinder.
D
Never allow a welding electrode to touch any cylinder.
D
Never weld on a pressurized cylinder
−
explosion will result.
D
Use only correct compressed gas cylinders, regulators, hoses,
and fittings designed for the specific application; maintain them
and associated parts in good condition.
D
Turn face away from valve outlet when opening cylinder valve. Do
not stand in front of or behind the regulator when opening the valve.
D
Keep protective cap in place over valve except when cylinder is in
use or connected for use.
D
Use the right equipment, correct procedures, and sufficient num-
ber of persons to lift and move cylinders.
D
Read and follow instructions on compressed gas cylinders,
associated equipment, and Compressed Gas Association (CGA)
publication P-1 listed in Safety Standards.
Содержание PipeWorx
Страница 4: ......
Страница 14: ...OM 239 982 Page 10...
Страница 27: ...OM 239 982 Page 23 Notes...
Страница 28: ...OM 239 982 Page 24 SECTION 6 ELECTRICAL DIAGRAM Figure 6 1 Circuit Diagram For Remote Feeder Interface...
Страница 29: ...OM 239 982 Page 25 239 983 A...
Страница 32: ...Notes...
Страница 33: ...Notes...
Страница 34: ...Notes...