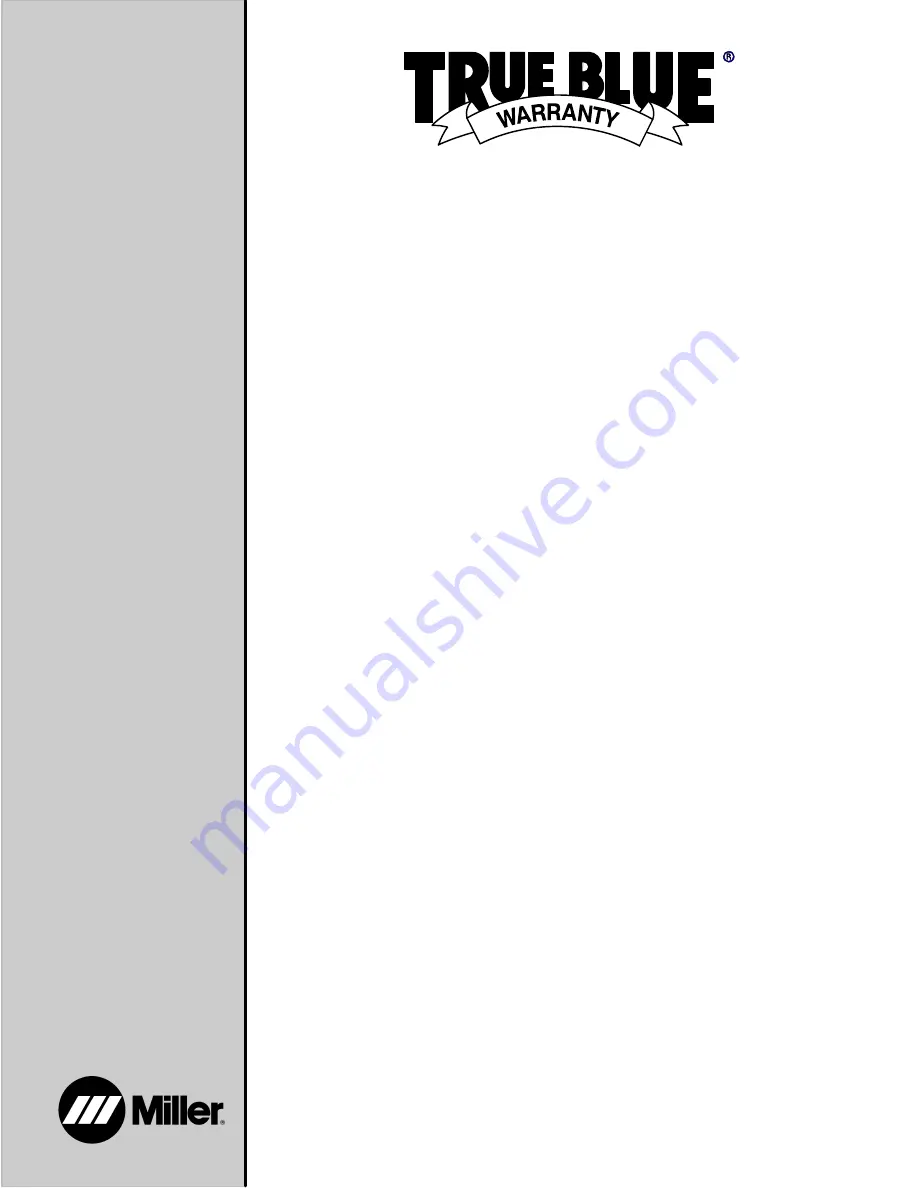
Warranty Questions?
Call
1-800-4-A-MILLER
for your local
Miller distributor.
miller_warr 2007−01
Your distributor also gives
you ...
Service
You always get the fast,
reliable response you
need. Most replacement
parts can be in your
hands in 24 hours.
Support
Need fast answers to the
tough welding questions?
Contact your distributor.
The expertise of the
distributor and Miller is
there to help you, every
step of the way.
Effective January 1, 2007
(Equipment with a serial number preface of “LH” or newer)
This limited warranty supersedes all previous Miller warranties and is exclusive with no other
guarantees or warranties expressed or implied.
LIMITED WARRANTY − Subject to the terms and conditions
below, Miller Electric Mfg. Co., Appleton, Wisconsin, warrants to
its original retail purchaser that new Miller equipment sold after
the effective date of this limited warranty is free of defects in
material and workmanship at the time it is shipped by Miller. THIS
WARRANTY IS EXPRESSLY IN LIEU OF ALL OTHER
WARRANTIES, EXPRESS OR IMPLIED, INCLUDING THE
WARRANTIES OF MERCHANTABILITY AND FITNESS.
Within the warranty periods listed below, Miller will repair or
replace any warranted parts or components that fail due to such
defects in material or workmanship. Miller must be notified in
writing within thirty (30) days of such defect or failure, at which
time Miller will provide instructions on the warranty claim
procedures to be followed.
Miller shall honor warranty claims on warranted equipment listed
below in the event of such a failure within the warranty time
periods. All warranty time periods start on the delivery date of the
equipment to the original end-user purchaser, and not to exceed
one year after the equipment is shipped to a North American
distributor or eighteen months after the equipment is shipped to
an International distributor.
1.
5 Years Parts — 3 Years Labor
*
Original main power rectifiers
2.
3 Years — Parts and Labor
*
Transformer/Rectifier Power Sources
*
Plasma Arc Cutting Power Sources
*
Process Controllers
*
Semi-Automatic and Automatic Wire Feeders
*
Inverter Power Sources (Unless Otherwise Stated)
*
Water Coolant Systems (Integrated)
*
Intellitig
*
Engine Driven Welding Generators
(NOTE: Engines are warranted separately by the
engine manufacturer.)
3.
1 Year — Parts and Labor Unless Specified
*
Motor Driven Guns (w/exception of Spoolmate
Spoolguns)
*
Positioners and Controllers
*
Automatic Motion Devices
*
RFCS Foot Controls
*
Induction Heating Power Sources, Coolers, and
Electronic
Controls/Recorders
*
Water Coolant Systems (Non-Integrated)
*
Flowgauge and Flowmeter Regulators (No Labor)
*
HF Units
*
Grids
*
Spot Welders
*
Load Banks
*
Arc Stud Power Sources & Arc Stud Guns
*
Racks
*
Running Gear/Trailers
*
Plasma Cutting Torches (except APT & SAF
Models)
*
Field Options
(NOTE: Field options are covered under True Blue
®
for the remaining warranty period of the product they
are installed in, or for a minimum of one year —
whichever is greater.)
*
Bernard-Branded Mig Guns (No Labor)
*
Weldcraft-Branded TIG Torches (No Labor)
*
Subarc Wire Drive Assemblies
4.
6 Months — Batteries
5.
90 Days — Parts
*
MIG Guns/TIG Torches and Subarc (SAW) Guns
*
Induction Heating Coils and Blankets, Cables, and
Non-Electronic Controls
*
APT & SAF Model Plasma Cutting Torches
*
Remote Controls
*
Accessory (Kits)
*
Replacement Parts (No labor)
*
Spoolmate Spoolguns
*
Canvas Covers
Miller’s True Blue
®
Limited Warranty shall not apply to:
1.
Consumable components; such as contact tips,
cutting nozzles, contactors, brushes, slip rings, relays
or parts that fail due to normal wear. (Exception:
brushes, slip rings, and relays are covered on Bobcat,
Trailblazer, and Legend models.)
2.
Items furnished by Miller, but manufactured by others, such
as engines or trade accessories. These items are covered
by the manufacturer’s warranty, if any.
3.
Equipment that has been modified by any party other than
Miller, or equipment that has been improperly installed,
improperly operated or misused based upon industry
standards, or equipment which has not had reasonable and
necessary maintenance, or equipment which has been
used for operation outside of the specifications for the
equipment.
MILLER PRODUCTS ARE INTENDED FOR PURCHASE AND
USE BY COMMERCIAL/INDUSTRIAL USERS AND PERSONS
TRAINED AND EXPERIENCED IN THE USE AND
MAINTENANCE OF WELDING EQUIPMENT.
In the event of a warranty claim covered by this warranty, the
exclusive remedies shall be, at Miller’s option: (1) repair; or (2)
replacement; or, where authorized in writing by Miller in
appropriate cases, (3) the reasonable cost of repair or
replacement at an authorized Miller service station; or (4)
payment of or credit for the purchase price (less reasonable
depreciation based upon actual use) upon return of the goods at
customer’s risk and expense. Miller’s option of repair or
replacement will be F.O.B., Factory at Appleton, Wisconsin, or
F.O.B. at a Miller authorized service facility as determined by
Miller. Therefore no compensation or reimbursement for
transportation costs of any kind will be allowed.
TO THE EXTENT PERMITTED BY LAW, THE REMEDIES
PROVIDED HEREIN ARE THE SOLE AND EXCLUSIVE
REMEDIES. IN NO EVENT SHALL MILLER BE LIABLE FOR
DIRECT, INDIRECT, SPECIAL, INCIDENTAL OR
CONSEQUENTIAL DAMAGES (INCLUDING LOSS OF
PROFIT), WHETHER BASED ON CONTRACT, TORT OR ANY
OTHER LEGAL THEORY.
ANY EXPRESS WARRANTY NOT PROVIDED HEREIN AND
ANY IMPLIED WARRANTY, GUARANTY OR
REPRESENTATION AS TO PERFORMANCE, AND ANY
REMEDY FOR BREACH OF CONTRACT TORT OR ANY
OTHER LEGAL THEORY WHICH, BUT FOR THIS
PROVISION, MIGHT ARISE BY IMPLICATION, OPERATION
OF LAW, CUSTOM OF TRADE OR COURSE OF DEALING,
INCLUDING ANY IMPLIED WARRANTY OF
MERCHANTABILITY OR FITNESS FOR PARTICULAR
PURPOSE, WITH RESPECT TO ANY AND ALL EQUIPMENT
FURNISHED BY MILLER IS EXCLUDED AND DISCLAIMED
BY MILLER.
Some states in the U.S.A. do not allow limitations of how long an
implied warranty lasts, or the exclusion of incidental, indirect,
special or consequential damages, so the above limitation or
exclusion may not apply to you. This warranty provides specific
legal rights, and other rights may be available, but may vary from
state to state.
In Canada, legislation in some provinces provides for certain
additional warranties or remedies other than as stated herein,
and to the extent that they may not be waived, the limitations and
exclusions set out above may not apply. This Limited Warranty
provides specific legal rights, and other rights may be available,
but may vary from province to province.
Содержание Millermatic 252
Страница 14: ...OM 230 693 Page 10...
Страница 25: ...A complete Parts List is available at www MillerWelds com OM 230 693 Page 21 Notes...
Страница 26: ...A complete Parts List is available at www MillerWelds com OM 230 693 Page 22 4 15 Weld Parameters...
Страница 27: ...A complete Parts List is available at www MillerWelds com OM 230 693 Page 23 226 650 B...
Страница 37: ...OM 230 693 Page 33 Notes...
Страница 38: ...OM 230 693 Page 34 SECTION 7 ELECTRICAL DIAGRAM Figure 7 1 Circuit Diagram...
Страница 39: ...OM 230 693 Page 35 229 485 A...