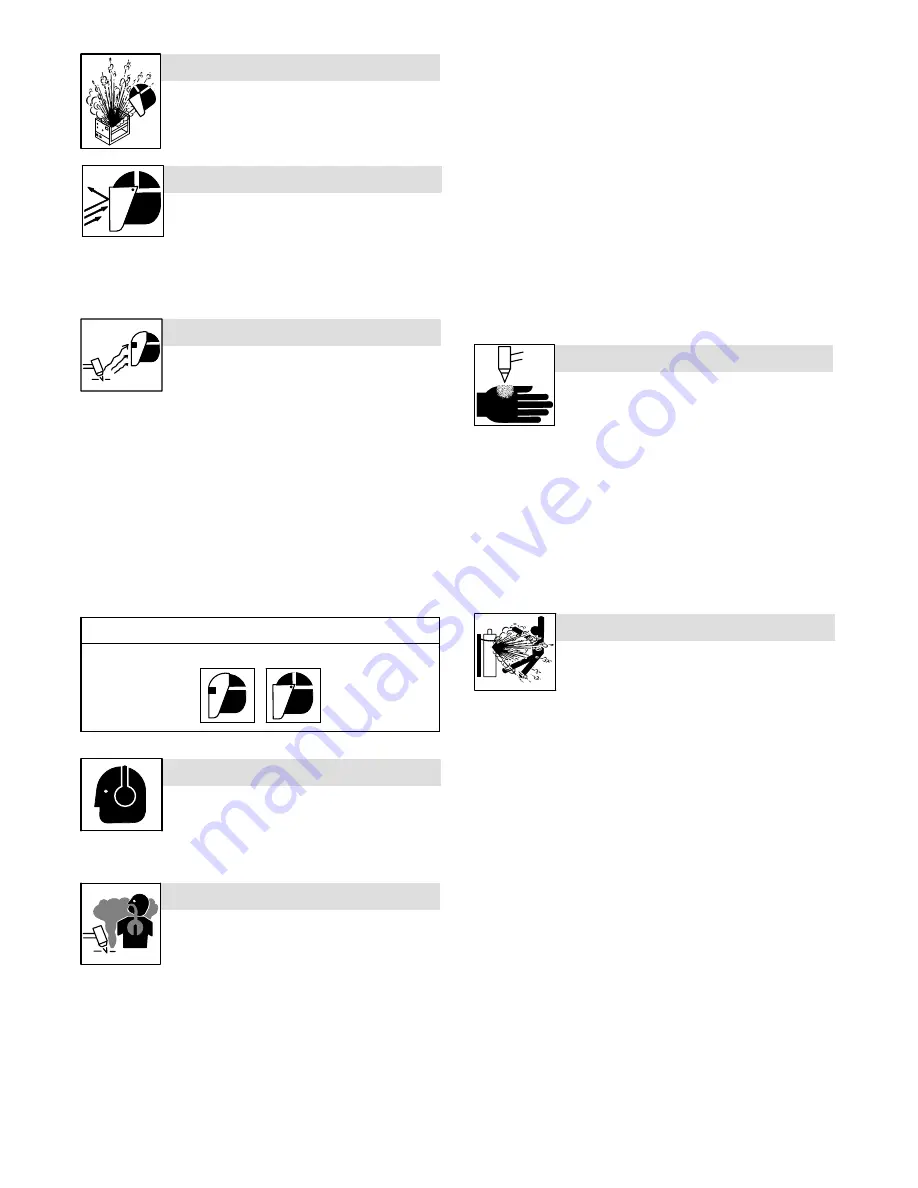
OM-201 872 Page 2
D
On inverter power sources, failed parts can ex-
plode or cause other parts to explode when
power is applied. Always wear a face shield
and long sleeves when servicing inverters.
EXPLODING PARTS can injure.
Sparks and hot metal blow out from the cutting arc.
Chipping and grinding cause flying metal.
FLYING SPARKS can cause injury.
D
Wear approved face shield or safety goggles with side shields.
D
Wear proper body protection to protect skin.
D
Wear flame-resistant ear plugs or ear muffs to prevent sparks from
entering ears.
Arc rays from the cutting process produce intense
visible and invisible (ultraviolet and infrared) rays
that can burn eyes and skin.
ARC RAYS can burn eyes and skin.
D
Wear face protection (helmet or shield) with a proper shade of filter
lenses to protect your face and eyes when cutting or watching. ANSI
Z49.1 (see Safety Standards) suggests a No. 9 shade (with No. 8 as
minimum) for all cutting currents less than 300 amperes. Z49.1 adds
that lighter filter shades may be used when the arc is hidden by the
workpiece. As this is normally the case with low current cutting, the
shades suggested in Table 1 are provided for the operator’s conve-
nience.
D
Wear approved safety glasses with side shields under your helmet
or shield.
D
Use protective screens or barriers to protect others from flash, glare
and sparks; warn others not to watch the arc.
D
Wear protective clothing made from durable, flame-resistant
material (leather, heavy cotton, or wool) and foot protection.
Table 1. Eye Protection For Plasma Arc Cutting
Current Level In Amperes
Minimum Shade Number
Below 20
20 − 40
40 − 60
60 − 80
#4
#5
#6
#8
Prolonged noise from some cutting applications can
damage hearing if levels exceed limits specified by
OSHA (see Safety Standards).
NOISE can damage hearing.
D
Use approved ear plugs or ear muffs if noise level is high.
D
Warn others nearby about noise hazard.
FUMES AND GASES can be hazardous
.
Cutting produces fumes and gases. Breathing
these fumes and gases can be hazardous to
your health.
D
Keep your head out of the fumes. Do not breathe the fumes.
D
If inside, ventilate the area and/or use local forced ventilation at the
arc to remove cutting fumes and gases.
D
If ventilation is poor, wear an approved air-supplied respirator.
D
Read and understand the Material Safety Data Sheets (MSDSs)
and the manufacturer’s instruction for metals to be cut, coatings,
and cleaners.
D
Work in a confined space only if it is well ventilated, or while wearing
an air-supplied respirator. Fumes from cutting and oxygen depletion
can alter air quality causing injury or death. Be sure the breathing air
is safe.
D
Do not cut in locations near degreasing, cleaning, or spraying oper-
ations. The heat and rays of the arc can react with vapors to form
highly toxic and irritating gases.
D
Do not cut on coated metals, such as galvanized, lead, or cadmium
plated steel, unless the coating is removed from the cutting area, the
area is well ventilated, and while wearing an air-supplied respirator.
The coatings and any metals containing these elements can give off
toxic fumes when cut.
D
Do not cut containers with toxic or reactive materials inside or
containers that have held toxic or reactive materials − they must be
emptied and properly cleaned first.
PLASMA ARC can cause injury.
The heat from the plasma arc can cause serious
burns. The force of the arc adds greatly to the burn
hazard. The intensely hot and powerful arc can
quickly cut through gloves and tissue.
D
Keep away from the torch tip.
D
Do not grip material near the cutting path.
D
The pilot arc can cause burns − keep away from torch tip when trig-
ger is pressed.
D
Wear proper flame-retardant clothing covering all exposed body ar-
eas.
D
Point torch away from your body and toward work when pressing
the torch trigger − pilot arc comes on immediately.
D
Turn off power source and disconnect input power before disas-
sembling torch or changing torch parts.
D
Use only torch(es) specified in the Owner’s Manual.
Gas cylinders contain gas under high pressure. If
damaged, a cylinder can explode. Since gas cylin-
ders are normally part of metalworking processes,
be sure to treat them carefully.
CYLINDERS can explode if damaged.
D
Protect compressed gas cylinders from excessive heat, mechani-
cal shocks, physical damage, slag, open flame, sparks, and arcs.
D
Install and secure cylinders in an upright position by chaining them
to a stationary support or equipment cylinder rack to prevent falling
or tipping.
D
Keep cylinders away from any cutting or other electrical circuits.
D
Never allow electrical contact between a plasma arc torch and a
cylinder.
D
Never cut on a pressurized cylinder − explosion will result.
D
Use only correct gas cylinders, regulators, hoses, and fittings de-
signed for the specific application; maintain them and associated
parts in good condition.
D
Turn face away from valve outlet when opening cylinder valve.
D
Keep protective cap in place over valve except when cylinder is in
use or connected for use.
D
Use the right equipment, correct procedures, and sufficient number
of persons to lift and move cylinders.
D
Read and follow instructions on compressed gas cylinders, asso-
ciated equipment, and Compressed Gas Association (CGA)
publication P-1 listed in Safety Standards.
Содержание ICE-100T
Страница 48: ...OM 201 872 Page 44 SECTION 8 ELECTRICAL DIAGRAM Figure 8 1 Circuit Diagram For Power Source...
Страница 49: ...OM 201 872 Page 45 201 858 A...
Страница 54: ...Notes...