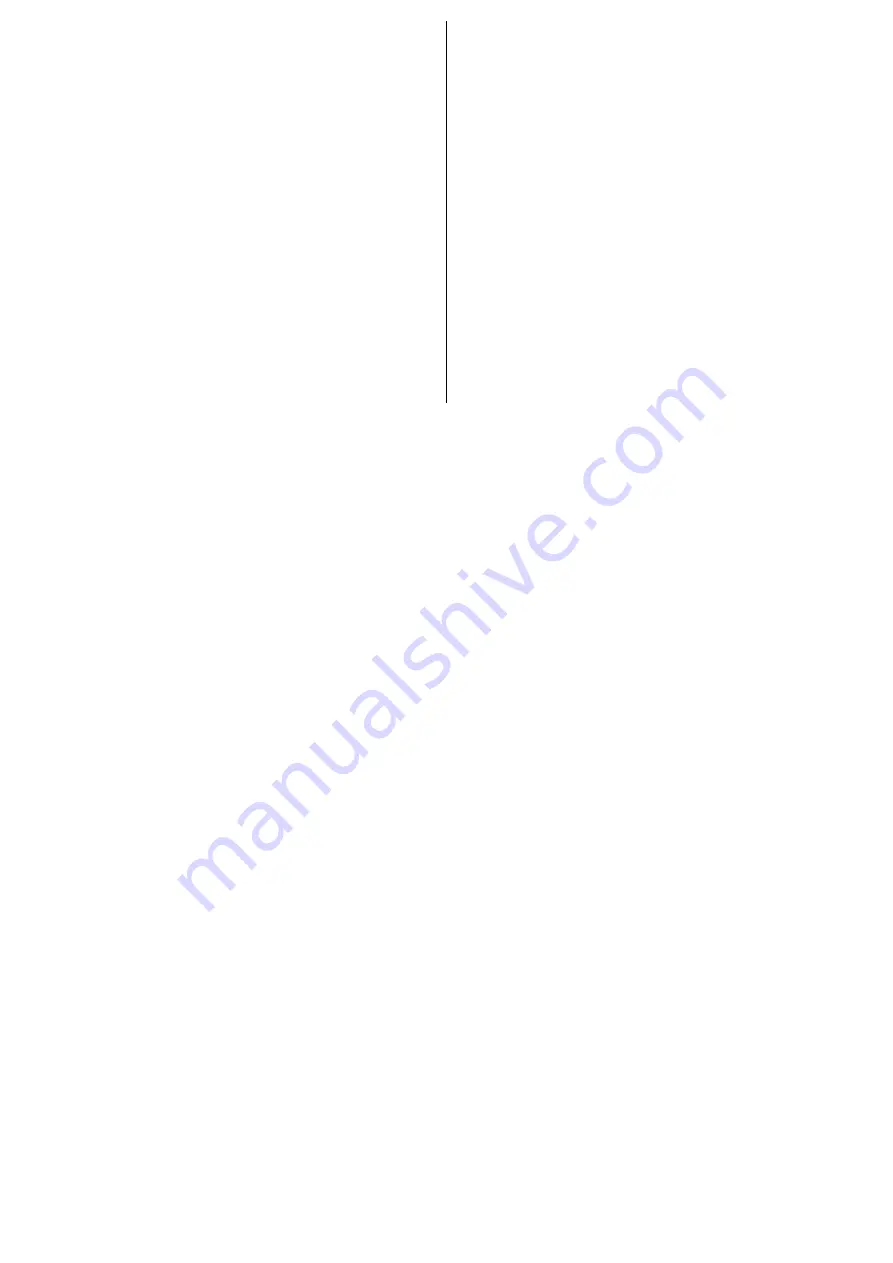
6
WELDING
HINTS
Welding with Solid Wires (Steel, Aluminium &
Stainless Steel)
The flexible we
ld
ing cable extending from the
wire
feed
unit should be
plugged
in
t
o
the
Pos
i
tive socket and the
earth lead plugged into one of the Negative sockets
.
Gasless Wire Welding (Flux Cored)
For gasless
welding wire
requiring reverse polarity
,
the
flexible welding
cable extending
from the
wire feed
unit
should be plugged
in to
the Negative socket
,
and the
earth
lead
into
t
he Pos
i
tive socket.
Gasless
welding wire requires
lower
wire feed speeds and
voltage when
compared to solid
wires.
To ensure a
positive wire
feed,
knurled feed
rolls
appropriate to the
wire
size
being
used should be fitted in
place of smooth feed
rolls
.
Aluminium Welding
Select a voltage setting approx
.
halfway through the
low
range on your machine (e.
g.
1+6 of 12
,
or2+4 of
24)
.
Set
the wire
feed speed to approx
.
10
and the gas
flow meter
to
approx
.
20-25 litres per minute
when welding
.
Remove oxide coating from
weldments with
a
stainless-
steel
wire brush
.
Initiate
arc and lift the to
r
ch nozzle away
from the weld pool until the nozzle
/we
ld
distance
is
12-15
times
the
diameter
of
t
he
w
ire
(e.
g.
11-14mm for 0
.
9mm
wire).
Direction of travel should be from r
i
ght to
left by
pushing
the gun
.
ALWAYS TEST
SETTINGS ON A SCRAP
PI
ECE
OF
MATERIAL
FIRST.
Stain
l
ess
Steel
Welding
Always use a clearance size liner (e.
g.
1
.
2mm liner
for
0
.
9mm wire)
.
Voltage and
wire feed
settings
will
be
similar to those used
for welding
mild ste
el.
Ho
we
ver
,
the
different
gas
will increase
the
arc
temperature
.
Set the gas flow meter to approx
.
20 litres
per minute
.
Ensure
when welding that
the torch nozzle is lifted
away
from the
weld pool
until the nozzle/weld poo
l
d
is
tance is
12-15 t
i
mes the diameter of the
wire
.
A
clearance si
z
e
contact tip may be necessary in
some
situations
of high
torch heat. (e.
g.
0
.
9A mm t
i
p for 0
.
9mm
wire
,
or
1
.
2A mm
tip
for 1
.2mm wire)
.